Industrial 3D models
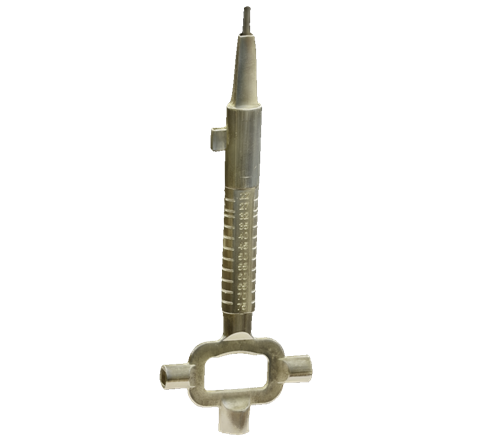
Universal screwdriver • Artec Studio
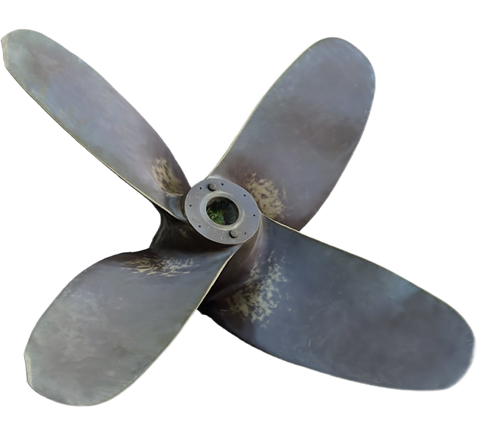
Ship’s propeller • Artec Studio
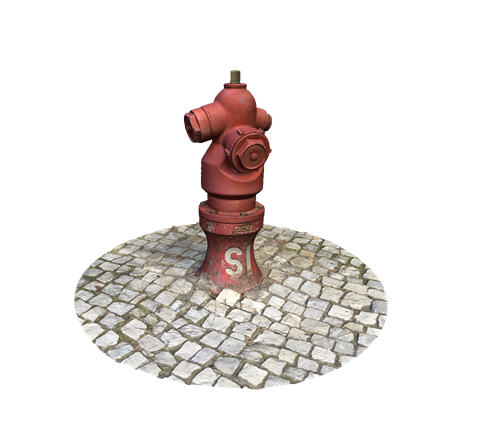
Hydrant • Artec Studio
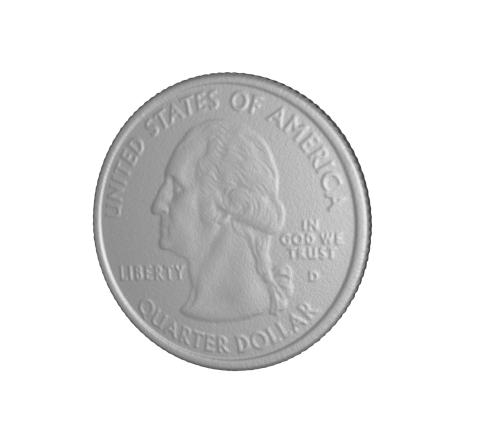
Quarter dollar • Spider II
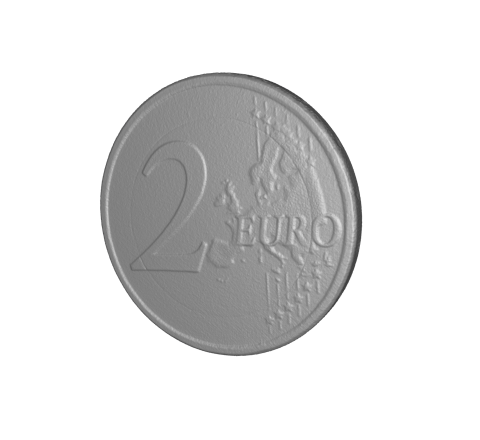
Euro coin • Spider II
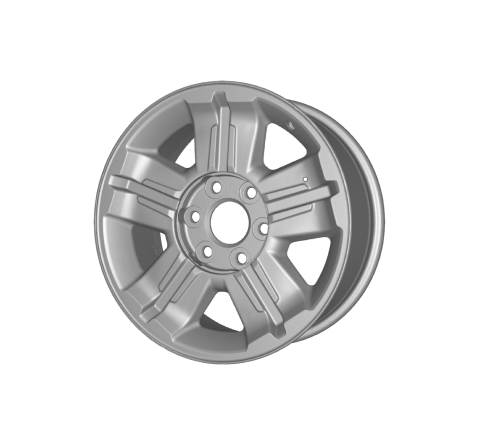
Car rim • Point
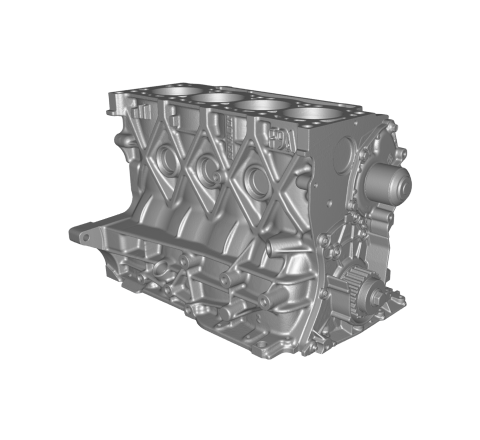
Four-cylinder engine • Point

Transmission • Point

Gray sneaker • Spider II
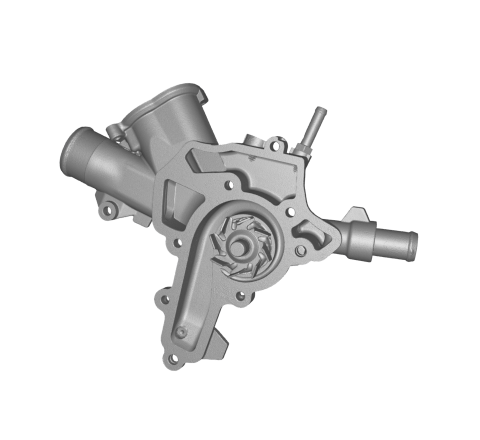
Water pump • Spider II
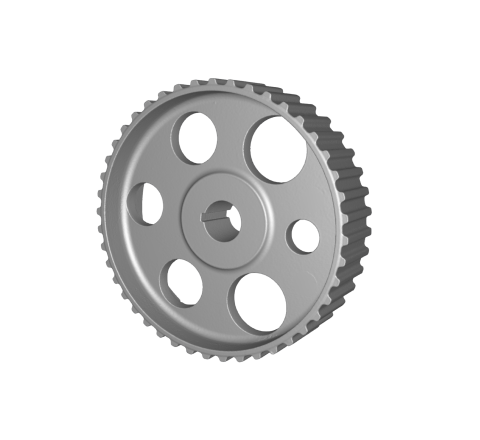
Cam gear • Point
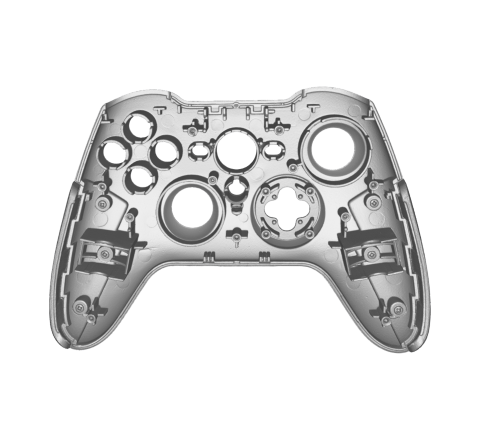
Game controller • Spider II
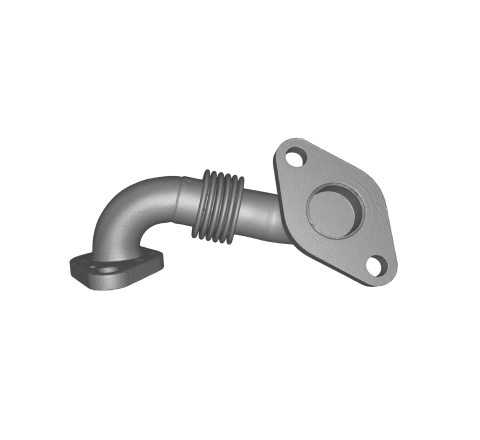
EGR metal connection pipe • Micro II
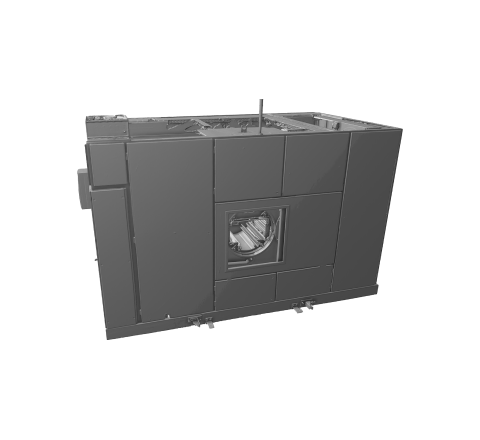
Colossal cleaning machine • Combo
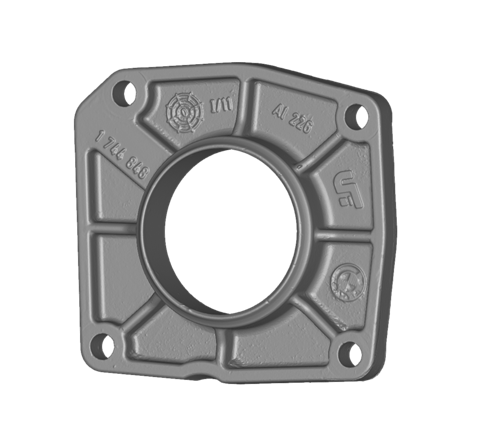
Industrial part • Micro II
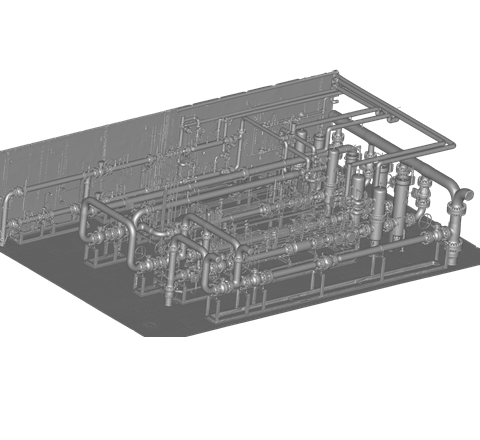
Pipes • Ray II
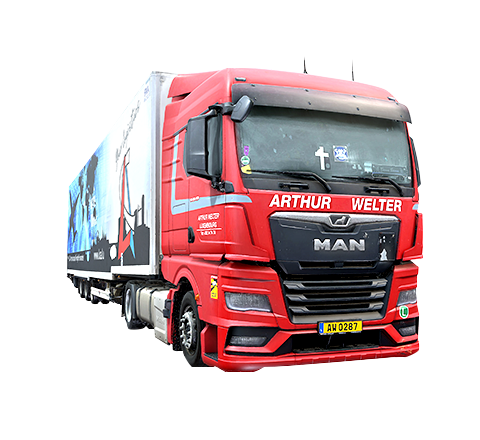
Semi-trailer truck • Combo • HD
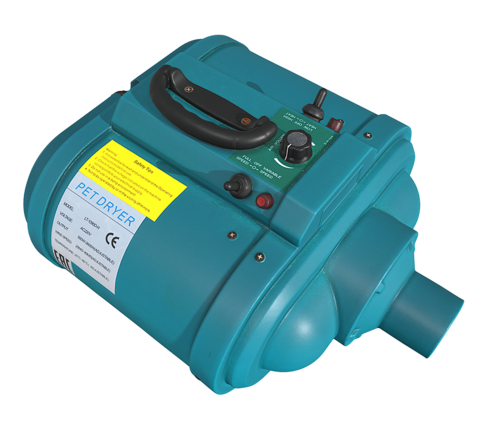
Pet hair dryer • Leo • HD

Pipe system • Combo
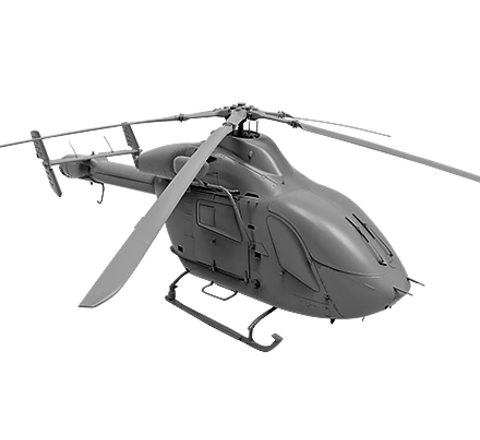
Air rescue helicopter • Combo
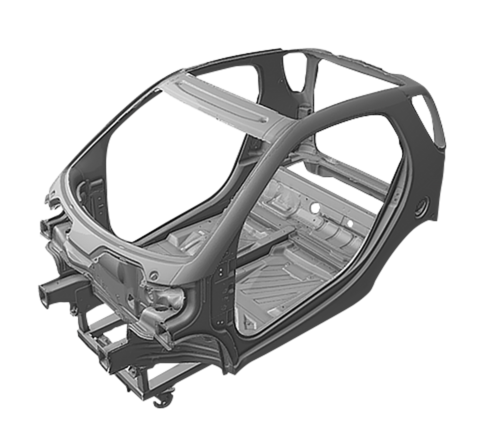
Smart car frame • Leo • HD
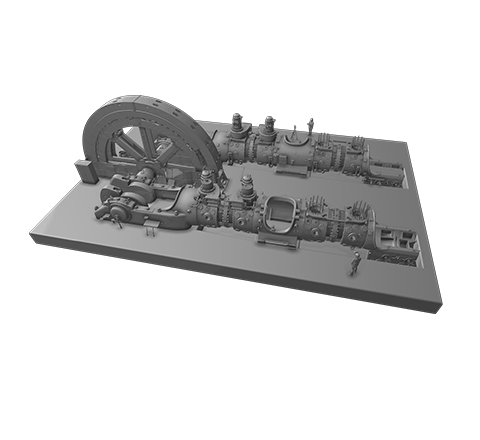
Blast furnace gas engine • Combo
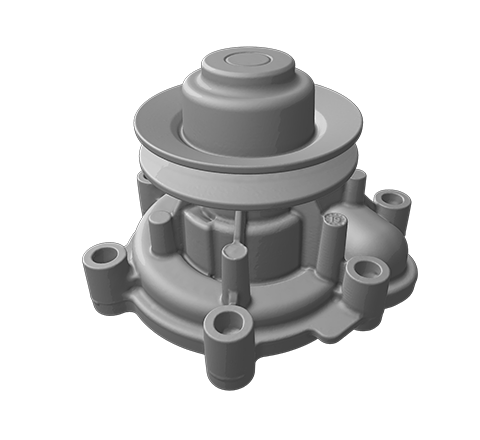
Automotive water pump • Space Spider
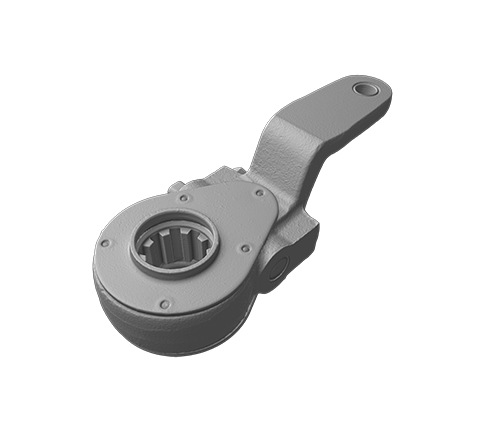
Adjusting lever • Space Spider