Inspection with Artec Leo slashes risk of costly lost-foam casting errors
Challenge: Ensuring foam patterns are accurate before they’re sent to service providers and manufactured into metal molds. Adapting foam mock-ups is quick, easy, and costs very little, but deviations in final molds can render them unusable and be very expensive to fix.
Solution: Artec Leo, Artec Studio, ZEISS Inspect Optical 3D
Result: A sub-millimeter accuracy inspection workflow that allows for the documentation of plaster cast designs, direct CAD-model comparison, and complete quality control. Final molds are also inspected with Leo to ensure geometric accuracy and industry standard compliance.
Why Artec 3D?: Upgrading from Artec Eva to Leo has allowed the manufacturer to measure with the same accuracy, only at a much faster pace. Leo’s wireless versatility and wider field of view also streamline the capture of large molds. Artec Studio then allows the team to turn scan data into 3D models and seamlessly send these to ZEISS software for in-depth inspection.
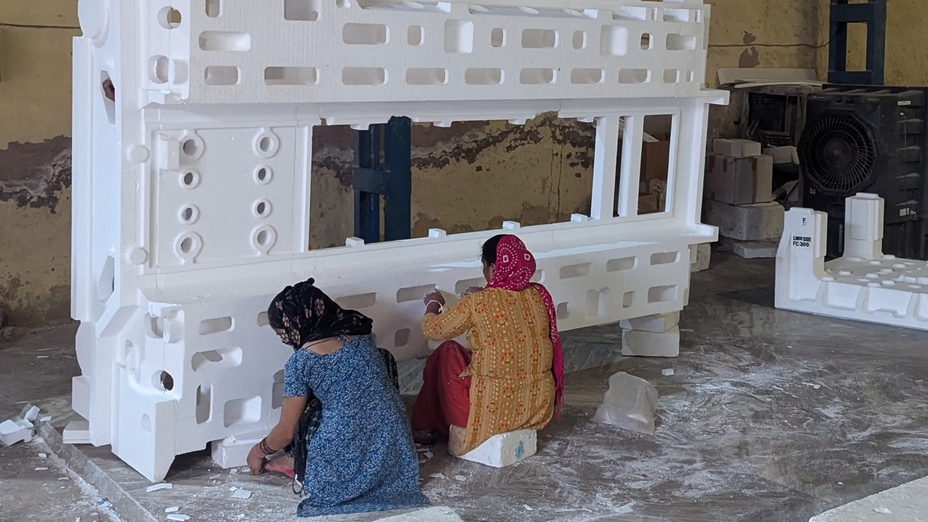
A foam casting of a large automotive component (car door mold).
As digital manufacturing continues to evolve, it’s gradually becoming easier to make bespoke products with unique designs. However, the reality in most major industries is this: economic viability requires serial production, and this in turn relies on scalable manufacturing.
This could involve machining, stamping, forming, product assembly, or textile manufacturing. Despite being one of the oldest techniques around, molding also remains highly popular. Molds can be made in various ways nowadays, but the molding process is often very similar. Material is poured into a hollow cavity in the shape of the final product. Once this solidifies, the mold is opened, and the shaped part is removed. If necessary, it’s then post-processed for end-usage.
Generally, mold-making methods differ in two ways: molding material compatibility, and sacrificial material, whether it be wax, plastic, metal, or foam. The latter is already widely used in major markets like China, India, Italy, Germany, and the US due to its low cost, pristine surface, and ease of adaptability. It also fits into a wider, easy-to-manage workflow.
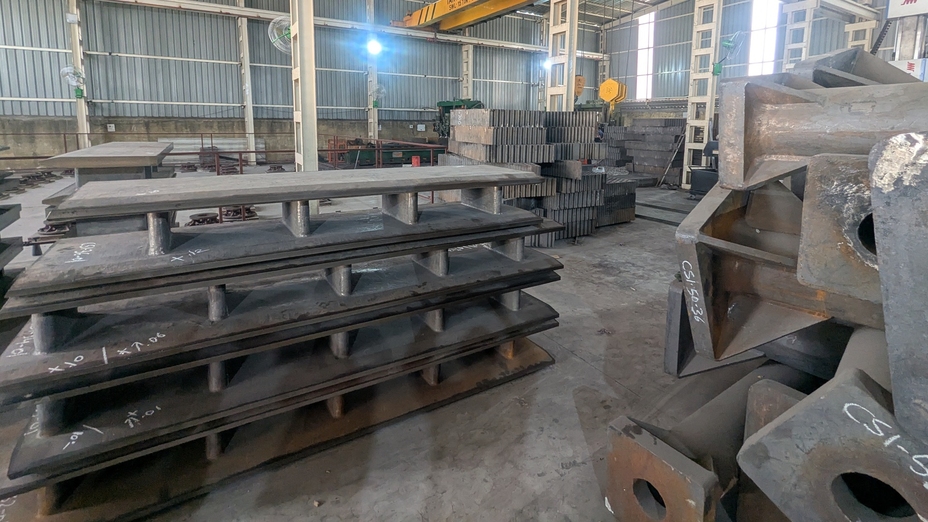
A warehouse full of industrial molds.
In lost-foam casting, a foam pattern is cut or assembled into a product shape. This is coated in a ceramic slurry that shields it against hot metal and submerged in silica sand for reinforcement. Finally, a hot alloy is poured into the pattern, vaporizing the foam as it goes. The remaining ceramic shell and sand then shape material in the cavity left behind to form a product mold.
But there are challenges to foam casting that can make it tricky to implement effectively. For example, molds with negative angles make parts difficult to extract in one piece. Additionally, as part of the process, foam molds are often sent to third parties and manufactured from metal. So, how do you make 100% sure that received castings meet desired tolerances?
That’s where one of Artec 3D’s Indian customers is changing the game. With Artec Leo 3D scanning, the manufacturer inspects castings and final molds before and after shipping. In doing so, they ensure that foam patterns leave the facility as designed – and more importantly – that metal molds meet required standards. Mistakes at this stage can cost several hundred thousand dollars to correct, or even more for large defunct parts that need to be recast entirely.
How Leo is modernizing lost-foam casting
Artec’s latest mold manufacturing client largely works at scale, making foam casting ideal. This is because working with the kind of tough steel required to make castings is hugely expensive and demands a great deal of care – wasted material also impacts margins. By contrast, foam is cheap and easy to adapt. As part of a recent project, they demonstrated this to great effect.
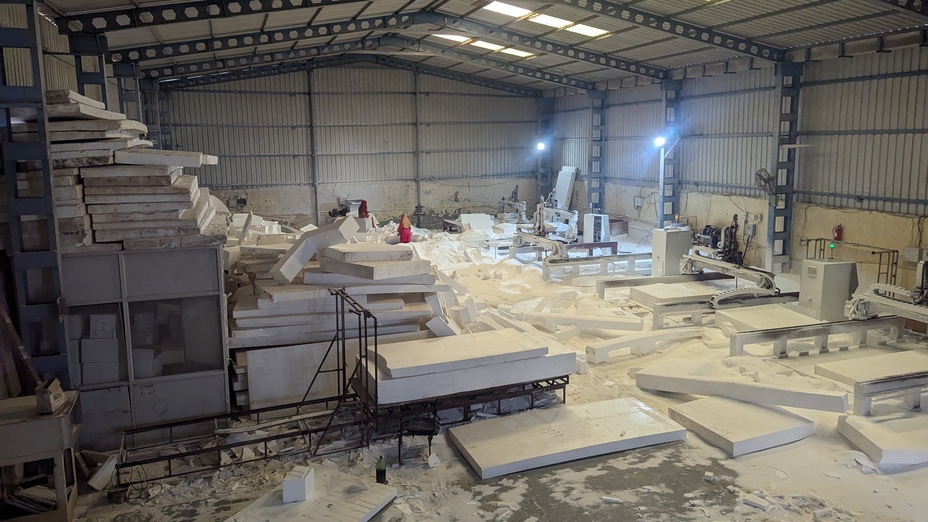
A factory floor with foam cuttings, or part of the foam casting manufacturing process.
Tasked with creating a large, complex chassis press form, the company opted to CNC-machine a CAD design in foam and then send this to a service provider for manufacturing. In the vehicle assembly workflow, the resulting mold is designed to be hydraulically pressed against a material to make thousands of car doors, in a way that relies heavily on part strength and accuracy.
In the past, the Artec user would’ve ensured foam pattern accuracy with Artec Eva, the 0.1 mm accurate, time-tested, wired 3D scanner. But sensing that inspection could be accelerated further, they’ve since turned to Gold-certified Partner Altem Technologies, who set them up with Artec Leo – a high-speed, completely cable-free device that has revolutionized their workflow.
Leo not only boasts the same accuracy as Eva, it has a larger field of view. This improves tracking, while its faster capture speed allows for complete 3D scans of large builds in hours. These 3D measurements ultimately enable the firm to identify errors at the foam-patterning stage and make corrections before they ever leave the factory, at virtually no additional cost.
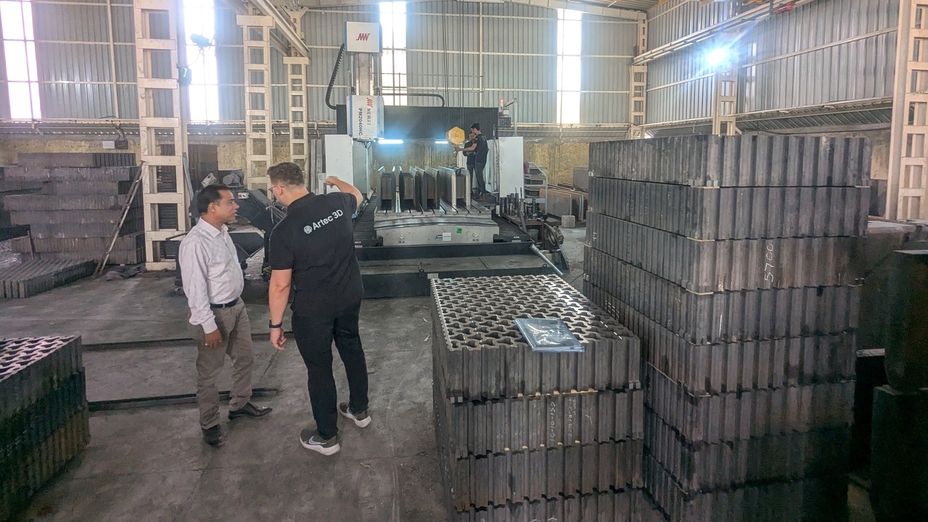
A CNC machine being used to apply the finishing touches to a mold.
It’s also worth noting that mold manufacturing tolerances get tighter as the workflow progresses. Initial designs that haven’t yet been polished with machining tend to feature surfaces that aren’t perfectly flat or aligned. As a result, these only need to be accurate to within a few millimeters, making Leo more than accurate enough for users’ needs – both in the inspection of foam patterns and received castings, to ensure they’re produced to specification.
In-depth analysis for compliant casting
Rapid, intuitive data capture is one thing. But the manufacturer still needs to turn point-cloud data into a mesh for analysis. That’s where Artec Studio comes in. Artec’s latest software features all the reverse engineering and inspection essentials, so users can capture, process data, and then use the resulting model to measure, analyze, and find deviations.
For this use case, the company’s team opted to export their data to ZEISS Inspect Optical 3D, an even more advanced inspection software with tools for in-depth analysis. Sharing data from Artec Studio is seamless and provides access to features like Python scripting and GD&T tools, as well as a software built on parametric principles that remembers each step of your workflow.
Using these functionalities, they measure shrinkage (a common problem in the world of foam casting), deviations, and other manufacturing issues. Previously, they’d manually check molds with a micrometer. Switching to 3D scanning has streamlined, accelerated, and boosted the accuracy of these checks, while providing access to a next-level digital inspection toolkit.
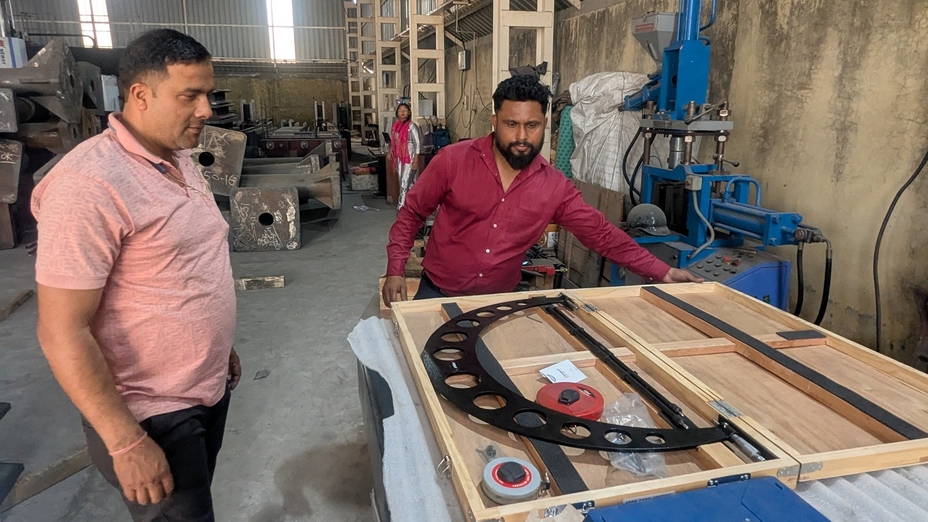
Engineers using an analogue industrial micrometer.
When it comes to receiving the final mold, this level of quality control is extremely useful to the manufacturer. Once they have evidence of how foam patterns left the factory, they can prove it when service providers make an error in production, and request that costs be reimbursed.
Where next for digital casting inspection?
Already the proud owner of two Artec Evas & Leos, the company is now considering upgrading more of its hardware to unlock further optimization and help meet growing demand. This could see it invest in more Leos, or adopt Artec Point, Artec’s first laser scanner, ISO-certified for exactly the kind of industrial metrology-grade applications it’s constantly engaged with.
A lot of the time, this manufacturer adds final details to parts with machining – whether these be automotive molds or any other kind of large metal object. As its CNC systems operate at an accuracy of up to 20 microns, the metrology-grade Point would be perfect for final inspection.
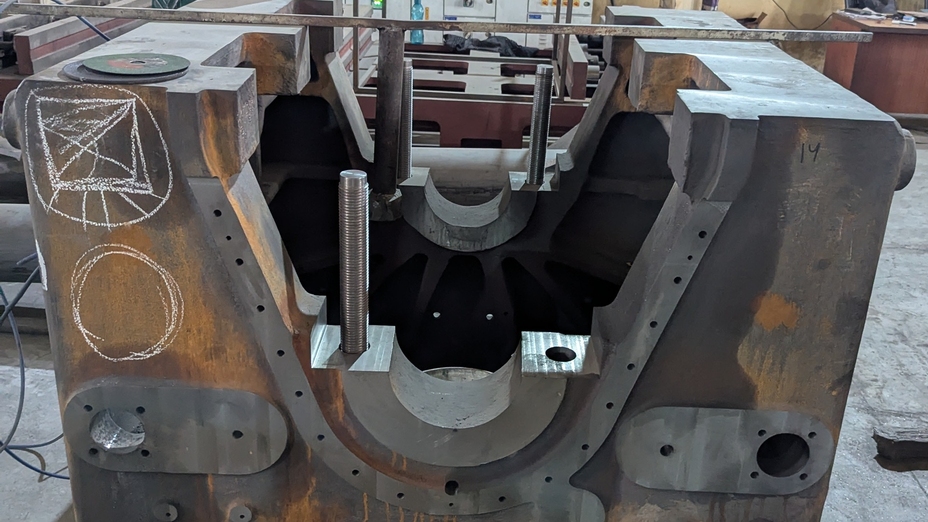
A huge finished industrial automotive mold.
If we zoom out a little, the manufacturer’s workflow is also impressive but not unique. Artec 3D scanning is regularly used for casting inspection across many industries and markets. In the US, full-service jobbing foundry Willman Industries deploys Artec Eva for scan-CAD analysis.
Ausco Products does something similar with Artec Leo, Space Spider & Geomagic Design X. Externally sourced brake castings are analyzed and checked against accuracy, tolerance, and performance standards. Altogether, these use cases show how Artec 3D solutions are allowing engineers to adapt to customer needs, even in seemingly diverse industrial applications.
Scanners behind the story
Try out the world's leading handheld 3D scanners.