How does a 3D printer work?
With the variety of 3D printers available today, your manufacturing options are virtually unlimited: from plastic toys and chocolate of the most specific and unusual shapes to ceramic dental implants and body casts or prostheses, to metal industrial parts of all possible sizes, and more. Need a coffee cup? You can print that. Want a house? You can print that, too. While the kind of 3D printing technology you employ depends entirely on what your project demands, and the properties of the material used, the idea behind any 3D printer’s work basically comes down to this: using a 3D model to build a solid physical object from the bottom up (or the other way around), by combining tiny bits of plastics, composites, or bio-materials together.
Introduction
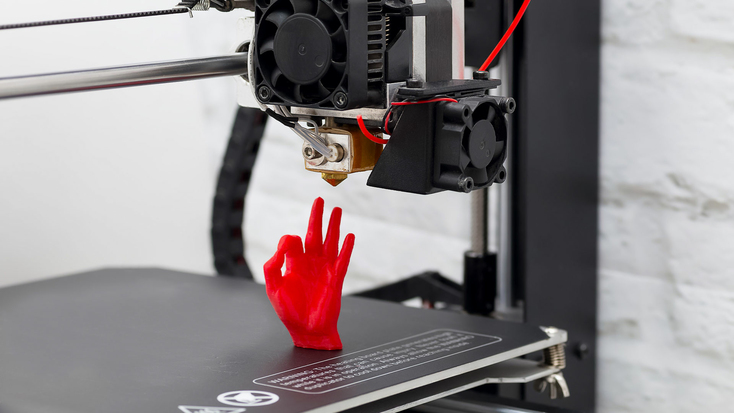
3D printing has taken the world by storm, and has proved incredibly influential in boosting bespoke manufacturing. It is easily one of the most revolutionary innovations in our time, so let’s first understand why. What’s the big deal, and why does 3D printing seem to be everywhere?
With many uses and seemingly countless possibilities – and these possibilities continue to increase as technology patents expire – 3D printing has exploded over the last few years. One of the reasons for its popularity today (apart from being insanely cool) is the fact that modern 3D printers are far more user friendly, so, at-home concept modelers or school teachers can take as much advantage of the technology as large-scale manufacturers do.
Not only is 3D printing becoming faster at producing more and more customized products, but scientists keep coming up with ingenious ways to print, sometimes by combining multiple materials. Innovations in 3D printing are bound to have commercial potential, as they mean manufacturing with minimum waste, cheaper prostheses, a better fit for tailored items, and faster production of spare parts.
In this article, we will explore what 3D printers are as well as how they work, while also discussing 3D printing technologies and applications, giving you a bit of a backstory while going over the key steps of the 3D printing process.
While the innovative part of the concept – equipment, tooling, materials, and the very idea of conjuring virtually anything out of plastic filament or powder – still seems overwhelmingly futuristic to many, 3D printing is not only exciting to explore, but easy to grasp.
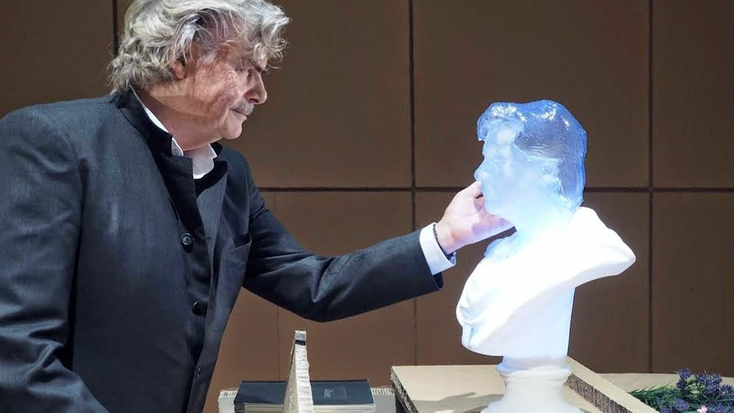
Austrian actor Peter Simonischek inspects his 3D-printed bust made from Artec Eva scans
In a nutshell, the technology uses a 3D model to physically produce a complete 3D object via a series of techniques, sometimes referred to as additive manufacturing. A common metaphor used to explain 3D printing is baking a sliced loaf of bread backwards: Imagine you’re baking each slice of bread individually and then gluing them together into a whole loaf, instead of baking a whole loaf first and then slicing it, as one typically would.
Now that you understand the basic idea, let’s dive into the details!
What is 3D printing?
When the 3D printing process appeared on the scene back in the 1980s, it was associated with the concept of rapid prototyping. This was because the process helped to develop prototypes far more accurately and swiftly than any other method had before. Chuck Hall, one of the creators of the very first 3D printer, made history in 1986 when he invented and patented stereolithography – or as it is more commonly known now, SLA. Hall went on to found 3D Systems, which till today remains a pillar of the industry. This kick-started the evolution of a technology that would soon be seen as something out of a sci-fi film.
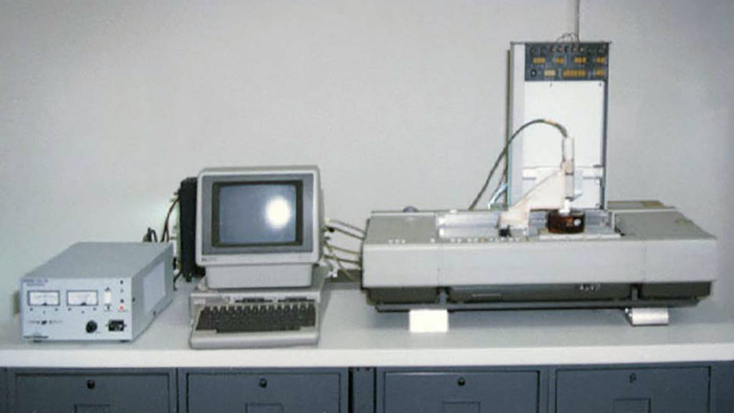
The first 3D printer invented by Chuck Hall. Image source: www.my3dconcepts.com/explore/history-of-3d-printing
In short, both then and now, 3D printers are astonishing next-gen machines that use 3D models to create physical objects from a variety of materials. Instead of ink in your average inkjet printers, 3D printers use other materials such as molten plastic, rubber, metallic powders, and carbon fiber.
What 3D printing is, in essence: Piling up layer upon layer and fusing them together with adhesive material or ultraviolet light to create an object in 3D.
How does a 3D printer work?
It takes a combination of high-quality software, proper materials, and industry-grade tools to create a 3D object out of thin air. To understand how exactly this combination works, let’s take a closer look at three basic steps of the 3D printing process: First, you need a 3D file, which you can obtain by downloading, 3D scanning, or designing yourself. Then, you decide on the 3D printing technology you’ll need. And finally, you send your design to a 3D printer to be turned into the desired object.
Let’s take a closer look at each of these steps.
3D modeling and 3D scanning
How can you make a 3D model? There are at least two ways: by using 3D modeling software, or by digitizing real-world objects via 3D scanning. While both methods present advantages and disadvantages, your choice will largely depend on the needs of your project. In case you’d like to delve deeper into the topic, check out our guide on how to make 3D models.

3D scanning the crankshaft of an internal combustion engine with Artec Eva, a structured-light 3D scanner
One major benefit of top-of-the-line 3D modeling software is its vast range of capabilities. As a professional, it helps you create any model you could possibly imagine, from a miniature part of a timepiece to the entire clock tower surrounding it. This is just what you need for designing objects that do not yet exist, getting creative with your model, or obtaining a model of an object that is not available for scanning.
The evident pros of designing your own model in 3D modeling software would then be realistic visualization, artistic expression, and a possibility to use the 3D file libraries that many platforms offer. What’s not so great about this approach? Creating 3D models this way is very time consuming, and often enough, the final results can be inaccurate.
KEY POINT
3D scanning allows you to precisely digitize a real-world object, a human being, or even an entire building, scene, or environment.
But not to worry – there’s another avenue that has been gaining popularity recently, especially for professional projects. This alternative method is 3D scanning, which allows you to precisely digitize a real-world object, a human being, or even an entire building, scene, or environment. You can easily complement 3D scanning with any modeling steps: such a hybrid workflow may involve editing your 3D scan data in CAD or sculpting software. As a standalone method, 3D scanning is widely used for reverse engineering, quality inspection, healthcare, heritage preservation, and more.
Regardless of the application, 3D scanning will save you a great deal of time and effort when replicating existing objects, not to mention the much elevated level of precision you can achieve if using a professional 3D scanner instead of traditional 3D modeling tools.
3D printing software
As soon as your 3D model is ready, you can get started with printing it. This is when 3D printing software makes its big entrance. This type of software helps you execute a 3D print by slicing your model and sending it to your printer.
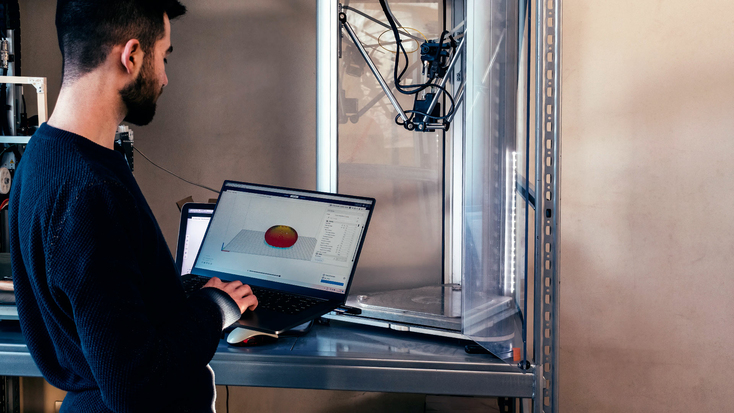
The slicing software is what you need as a mediator between your 3D model and your 3D printer. Simply put, “slicers” translate your file into the format or control language your 3D printer will understand (for many printers this will be G-code, while some others operate in their own format). A great number of free slicers are available to meet the needs of home users.
These programs are called slicers because that’s literally what they do: take your model and slice it into numerous flat layers that a 3D printer needs to properly do its work. Such software also works out the best printer settings such as layer height, temperature, print speed, and, mostly for FDM printers, the optimal path for the printer to follow.
Different brands of 3D printing software offer diverse functionalities that include slicing, providing remote access to a 3D printer, and much more, to monitor, control, and manage your 3D printer and streamline the communication between the devices. Whichever you prefer, all types of 3D printing software are part of an entire ecosystem.
There are plenty of options to pick and choose from for both experienced users and newbies, open-source or paid. In the last few years, 3D printing software has been offering innovative features and new capabilities in abundance, so you can easily find the right tool for a seamless workflow.
3D printing technologies
When it comes to actual printing, there is a dizzying number of technologies to choose from. Here’s a quick overview to make sense of them:
- Vat Photopolymerization
- SLA
- DLP
- CLIP
- Material Jetting
- Binder Jetting
- Material Extrusion
- FFF
- FDM
- Powder Bed Fusion
- SLS
- DMLS and SLM
- MJF
- EBM
- Sheet Lamination
- Directed Energy Deposition
Vat Photopolymerization
This 3D-printing technology features a variety of workflows that have one core concept in common: A liquid photopolymer is placed in a vat and selectively cured by a light source until a solid 3D object is built, layer by layer.
Variations of Vat Photopolymerization based on Stereolithography are Digital Light Processing, and Continuous Liquid Interface Production.
Stereolithography (SLA): The very first 3D printing technology is still the most widely known today. SLA is also known as photo-solidification, or resin printing. What happens is liquid resin is put in a vat, then an ultraviolet laser is focused on the resin through the transparent bottom of the vat. This beam cures and solidifies the resin layer by layer, and the solid object gradually emerges in the desired shape dragged up by a lifting platform.
Digital Light Processing (DLP) is one version of a vat polymerization modification. It is similar to the abovementioned SLA in the sense that it also cures liquid resin into a 3D structure; the light source used is the core difference here. DLP uses a digital light projector screen to flash the image of the layer across the platform, thus curing all points simultaneously, in the form of the layer. As the light projector is a digital screen, the image of every layer consists of pixels, so a 3D layer is composed of rectangular cubes known as voxels.
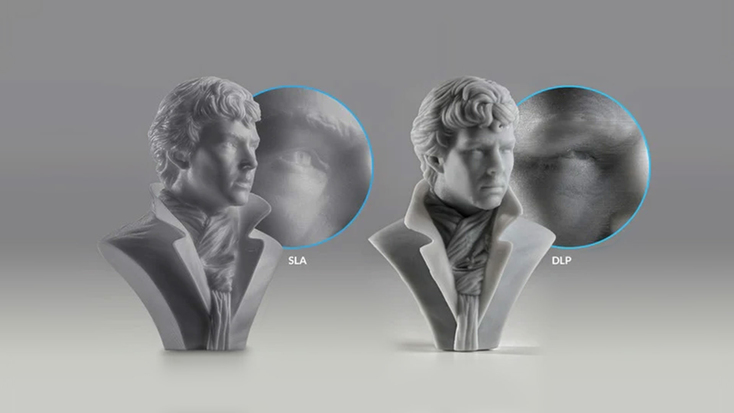
Image source: Formlabs
Continuous Liquid Interface Production (CLIP) is a proprietary 3D printing method originally owned by EiPi Systems and currently developed by Carbon3D. Since CLIP developed from SLA, you will again notice the similarities: a pool of liquid photopolymer with a bottom transparent to ultraviolet light, which solidifies resin, and a three-dimensional object slowly rising up from the vat. What’s different here is that the printing process is continuous. This is made possible with a special oxygen-permeable membrane in the base of the pool that creates a thin polymerization-free area, the so-called “dead zone.” This oxygenated zone helps the uncured resin stay liquid between the growing part and the projection window, also allowing it to flow into areas where it can be cured.
Material Jetting (MJ)
A comparatively new 3D printing technology, material jetting uses photopolymer droplets cured with UV light to create solid objects. This method can most easily be compared to what happens in a 2D inkjet process: before resin is solidified, it is sprayed in the form of very small droplets. MJ 3D printers sprinkle hundreds of resin droplets at a time, layer upon layer, until the part is complete.
Binder Jetting (BJ)
Binder Jetting is a 3D printing process in which a liquid bonding agent is selectively placed upon a layer of metal, sand, ceramic, or composite powder granules. To form a solid part, Binder Jetting moves a print head over the powder bed depositing droplets of a binder (simply put, glue) that keep the powder granules together. Each droplet of a binding agent is around 80 microns in diameter, which allows for great resolution. When the layer is complete, the powder bed moves downwards, and a new layer of powder recoats the surface of the previously printed layer. The droplets of a binder are deposited again, and the process repeats until the entire part is formed.
Material Extrusion
This method uses filament of a thermoplastic material, which is fed through a moving heated printer extruder. The material melts in the process of being pushed through the extruder’s nozzle. The extruder follows a predetermined path and deposits the filament onto a build platform, which can also be heated for better adhesion. When the first layer is ready, the next one is put on top of it to keep growing the workpiece. The object is formed when the filament cools down and solidifies.
Fused Filament Fabrication (FFF) and Fused Deposition Modeling (FDM): Material extrusion is widely known as Fused Filament Fabrication (FFF), which has been a massive hit among 3D printing enthusiasts. In turn, Fused Deposition Modeling is a proprietary term for the same process, coined by S. Scott Crum in the 1980s and commercialized a decade later by Stratasys. With the technology’s patent expired, FDM has become the cheapest – and therefore most available and accessible – 3D technology out there. The appearance of RepRap, an open source development community, made FDM a favorite technology of DIYers of the world. Material extrusion is also used industrially to build parts with complex geometries.
Powder Bed Fusion (PBF)
The 3D printing process in which a heat source selectively fuses powder particles inside a built area forming a solid part is called Powder Bed Fusion (PBF). Let’s get to know the different varieties of PBF.
Selective Laser Sintering (SLS): The main material used in Selective Laser Sintering is polymer powder, which is heated and deposited onto a build platform. After this step, a CO2 laser beam scans the surface, selectively sintering the powder. The laser solidifies the entire cross section, after which the build platform shifts one layer down to make space for a fresh layer of powder. The next cross-section of the object is then sintered again and again on top of the recently solidified layers – the process repeats until the object is manufactured. As a finishing touch, the object is cleaned with pressurized air and brushed.
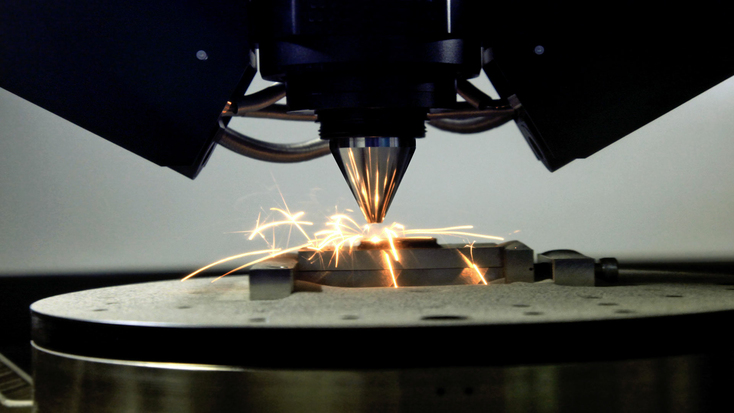
Direct Metal Laser Sintering (DMLS) and Selective Laser Melting (SLM): Based on pretty much the same principle, Direct Metal Laser Sintering (DMLS) and Selective Laser Melting (SLM) are used to produce metal parts exclusively. SLM is employed to fully melt the powder of metals such as aluminum, stainless steel, or cobalt chrome to form solid objects, while DMLS doesn’t melt powders – instead, it heats them up and fuses them on a molecular level. DMLS sinters alloys, including titanium-based ones.
Multi Jet Fusion (MJF): The Multi Jet Fusion (MJF) technique is slightly different from the above mentioned methods: instead of placing a new layer onto a solid one, it adds a new portion of agent while the previous one is still molten. Technically, it uses an inkjet array to apply fusing and detailing agents, then fuses them into a solid layer by heating the elements. No laser is needed, because detailing agents are jetted along particular contours. When the object is complete, the powder bed is moved to a processing station, where most of the loose powder is removed by an integrated vacuum. Compared to objects built with the help of SLS, this technique offers higher density and lower porosity, thus creating a smoother surface for the final part.
Electron Beam Melting (EBM): This technique is another Powder Bed Fusion method. Electron Beam Melting uses electrons, namely a high-energy beam, to fuse the particles of metal powder. While SLM uses a laser beam as energy source, EBM uses an electron beam instead, with the rest of the process being quite similar. Because of its higher energy density, EBM is much faster, but its use is limited to conductive materials such as zirconium or titanium.
Sheet Lamination (SL)
The next category of 3D printing technologies is Sheet Lamination (SL), sometimes referred to as Laminated Object Manufacturing (LOM). It is a rapid prototyping system created by Helisys Inc. that involves fusing layers of material (adhesive-coated paper, metal, or plastic laminates) with heat and pressure. The technique was popularized by Israeli-based Solido 3D, which printed parts made of polyvinyl chloride (PVC) and a special adhesive. The fused layers are then cut into a desirable shape with a laser or knife. The Sheet Lamination technique based on paper is not yet widely spread, but its creators keep experimenting to hone the method to perfection.
Directed Energy Deposition (DED)
A more complex 3D printing process, Directed Energy Deposition (DED), is often used to repair existing industrial parts such as propellers or turbine blades, or to add a different material, rather than build new parts from scratch. This is largely due to the fact that DED 3D printers are massive industrial devices requiring more space, skill, and control.
This method involves melting material (mostly metal powders or wire source materials) directly with a laser or electronic beam, while depositing it onto the growing part through a nozzle, which can move in multiple directions. The part is often 3D scanned in-process between the deposition of consecutive layers.
Some popular terms for this method include Direct Metal Deposition (DMD), Laser Engineered Net Shaping (LENS), Laser Deposition Welding (LDW), Electron Beam Additive Manufacturing (EBAM), and 3D Laser Cladding.
3D printing materials
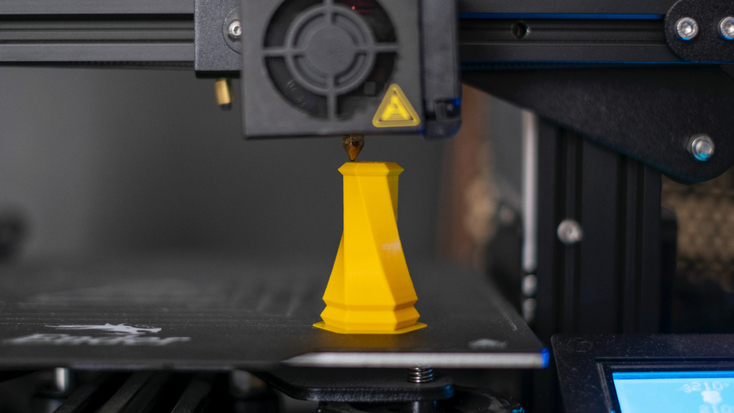
Now that you know a good amount about the methods which 3D printers employ to create solid objects, you might be wondering what the most common 3D printing materials are. To put it simply, what can be used as “ink” in 3D printers. These materials come in a wide variety, so when you choose the right ones for your project, you need to factor in the application and design of your object.
Here’s a quick overview of the 3D printing materials most commonly employed in different 3D printing technologies. It is also worth noting that many of these materials are not necessarily associated with just one 3D printing technology.
SLA: Resins
Rigid yet delicate, resin in its different forms is employed by technologies such as SLA, DLP, Multijet or CLIP. Resins, or photopolymers, are essentially 3D printable liquids that boast a very high chemical resistance and low shrinkage. Compared to other 3D-applicable materials, resins can sometimes be limited in strength and flexibility, but they still come in various formulations with a diverse range of optical, mechanical, and thermal properties. Due to their high photo-reactivity, resins often require a more complicated storage, which can be a limitation, too.
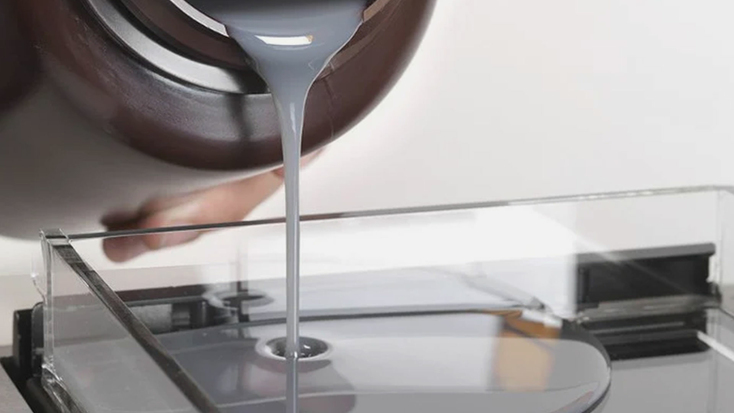
Liquid resin is used for both SLA and DLP. Image source: www.3dnatives.com/en/sla-vs-dlp-3d-printing-080420215
Standard resins are known as the most economic SLA material, producing high-resolution prints with fine features and a smooth surface finish. Widely used in prototyping applications, this translucent material offers a good level of detail, but is limited in terms of design because it requires a supporting structure for the model during printing.
Engineering resins for SLA were created to provide engineering specialists with a wider selection of material properties for different applications. This category includes such types of resin as tough, rapid, durable, and heat-resistant. While the names of these types mostly speak for themselves, all these resins require post-curing under ultraviolet light to bring out their maximum mechanical properties.
FDM: ABS, HIPS, HDPE, PLA, composite materials, and more
Acrylonitrile butadiene styrene (ABS): A common thermoplastic polymer, Acrylonitrile butadiene styrene is famously used to make LEGO bricks. The term “thermoplastic” explains that this sort of material becomes liquid and pliable (with a “glass transition”) in response to heat. What this means: ABS can be heated to its melting point, easily shaped, and quickly solidified. Used in countless applications, it is rather tough and rigid (ever stepped on a LEGO?), and retains color perfectly. This is a non-toxic material, which is also water and chemical resistant. One thing it doesn’t take well, however, is UV radiation – which is why it’s no good for extended outdoor use.
High Impact Polystyrene (HIPS): An easily dissolvable support material often used with ABS, High Impact Polystyrene also shares a number of properties with its 3D printing partner. Still, it is slightly lighter, more impact resistant, and low cost. When used for support structures, HIPS momentarily dissolves in d-Limonene, allowing for accurate support removal. Extremely easy to print, this material is really helpful in evaluating quick pre-production prototypes.
HDPE: A thermoplastic polymer made of the monomer ethylene goes by the name of High-density polyethylene (HDPE) and is used to produce piping, geomembranes, recyclable plastic bottles and packages (with the recycling code 2), and even plastic lumber. With a melting point of about 230 degrees Celsius (446 degrees Fahrenheit) and a considerable strength-to-density ratio, HDPE sometimes replaces ABS to build lighter and stronger, more flexible parts. However, this requires higher and thoroughly controlled temperatures, a heated print-bed and an extruder tolerant to high temperatures.
PLA is a polymer plastic produced from crops like sugarcane or corn, which makes it one of the most eco-friendly filaments on the market. It’s one of the most popular, too: compared to ABS, this material is inexpensive, biodegradable, can be printed more easily and at a lower temperature. On the downside, PLA is not as heat resistant and can often be brittle. Mostly known as a go-to material for desktop 3D printing, PLA is still used for manufacturing parts for many professional applications.
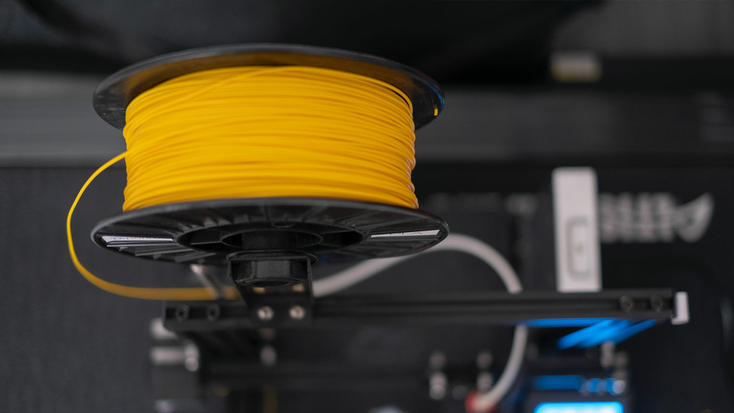
Composite materials typically combine a PLA, nylon, or PET base with different particles or fibers. Simply put, these materials are combined to benefit from their original properties. For example, after adding a little finishing, the eventual 3D models can boast the aesthetics of real wood or metal while the filaments only contain around 30% of wooden or metal particles. Adding color and experimenting with temperature could also change the final look of a 3D-printed part.
A different type of composite materials is composites with reinforcing fibers. Three of the most common representatives of this type are carbon fiber, fiberglass, and Kevlar. Being brittle and thin, the fibers are sometimes compared to uncooked spaghetti – they are not the easiest material to use on their own. However, when mixed with the plastic called the matrix, they are indispensable in creating strong, lightweight 3D parts.
Ceramics: Despite the fact that 3D printing is commonly associated with plastics, resins, and composites, ceramics have taken a special place among 3D printing materials. Especially appealing due to their durability, chemical resistance, aesthetics and tactility, let alone the incredible cost effectiveness, ceramic materials are used to 3D print anything from industrial parts to dental implants to tableware to art projects. Ceramics are usually classified as classic (made of clay – stoneware, earthenware, and porcelain) and technical, or engineered, ceramics (popular examples include Aluminum Nitride, Zirconia, Silicon Nitride, Silicon Carbide, and Alumina). Often the objects 3D printed with ceramics are kilned and glazed as in a classic pottery process.
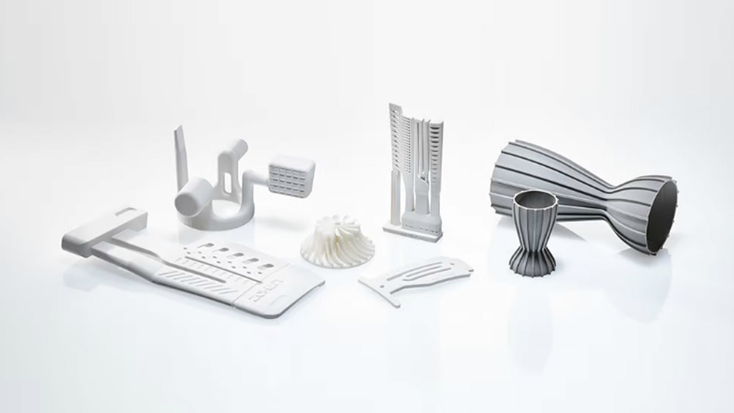
3D-printed industrial ceramic parts. Image source: Lithoz
SLS: Nylon and TPU
Nylon: Ideal for prototyping and end-use production, nylon is a common material to use for SLS. Being sturdy and durable, this engineering thermoplastic is suitable for complicated assembled parts. It also boasts high resistance when subjected to ultraviolet, high temperatures, water, and chemical solvents. Nylon is a part of the polyamides family, and its composites with such materials as aluminide, carbon, or glass are very versatile and often used in more than one 3D printing technology.
Thermoplastic Polyurethane (TPU): A combination of plastic and rubber known as Thermoplastic elastomers (TPE) is what flexible filaments are made of. Natural elasticity allows this material to flex and bend easily. Thermoplastic Polyurethane (TPU) is the most widely used type of TPE, so the term is often used to refer to the entire category. Its rubbery properties make TPE ideal for many projects, from household appliances and medical devices to wearable prints, toys, and phone covers. Flexible Filaments can be molded into practically any shape before they cool down and set, but they have their limitations, too. For example, such materials can be hard to print because of possible stringing or blobs.
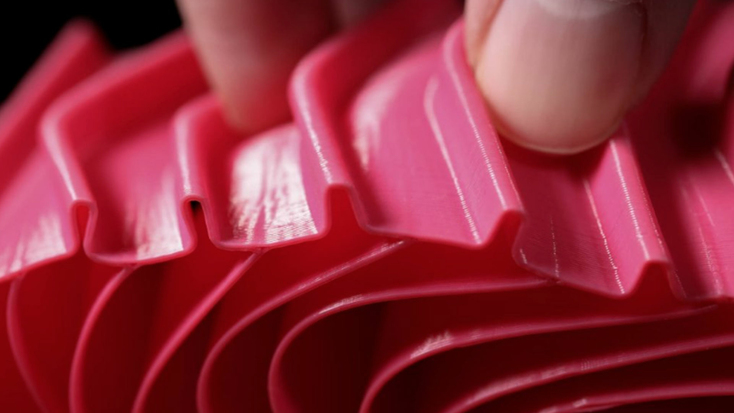
The flexibility of TPUs make them ideal for a range of 3D printing projects. Image source: www.kinvert.com/flexible-tpu-filament-3d-printing
SLM and DMLS: metal powders
Very fine metal powders, such as brass, bronze, steel, or copper are infused in metal filaments. The proportions of metal powder, PLA, and binding polymer could vary, but these filaments are still much heavier than plastics though not as heavy as pure metals. The final objects printed with this material will have the realistic look and feel of metal, especially if polished. Metal filaments are great for printing figurines and sculptures which are eventually much lighter than the actual bronze piece, for example. However, this sort of material tends to be rough, which means you’ll need to use a wear-resistant nozzle when printing and deal with clogging that might take place over time.
What are 3D printers used for?
In the less than 40 years that 3D printing has been around, it has secured its place in modern history as the 4th industrial revolution. Let’s take a look at some examples of how this innovative technology has reshaped entire industries.
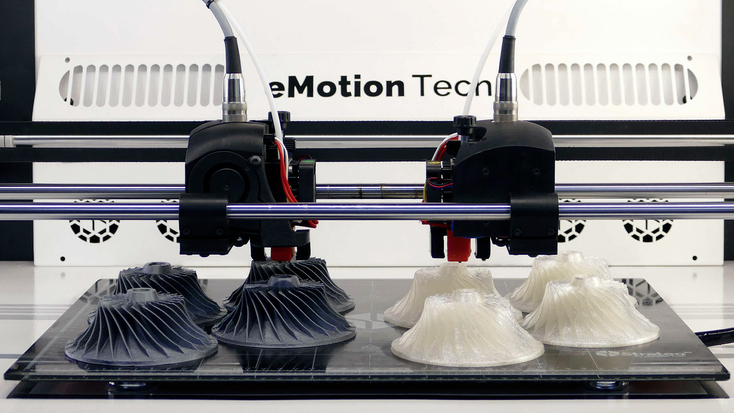
Rapid prototyping & rapid manufacturing
Rapid prototyping is a part of 3D printing history, if not the very reason for its existence. Thirty years ago when manufacturers were looking to overcome the frustration of not being able to create parts easily and quickly, 3D printing technology helped them save time and effort. Prototypes could finally be fabricated in hours rather than weeks, and soon enough, the development of 3D printing techniques and materials allowed for manufacturing final working parts, not just prototypes. This came to be known as rapid manufacturing.
Automotive
Rapid prototyping and manufacturing has given astounding freedom to automotive manufacturing. Car producers can now shorten production development and dramatically improve their final products at a much reduced cost. With the lead time at assembly lines substantially decreased, machine design can be improved and customized considerably. Another benefit is the ability to manufacture truly innovative mechanical parts for new models, as well as spare parts which can be printed on demand.
Aerospace
One of the earliest and most eager adopters of 3D printing, the aerospace industry first used the technology back in the late 80s. Industry giants such as Airbus and Boeing consider functional prototypes, tooling, and lightweight components to be some of the main applications of 3D printing. Its use across different sectors of the industry is not limited to rapid prototyping, either – fully functioning structural parts like turbines and propellers, wall panels, and air ducts have been successfully 3D printed and used for years now. The technology has also played a vital part in helping reduce the weight of different aircraft, which can lead to a reduction in CO2 emissions and fuel consumption.
Consumer products
Creating personalized, perfectly tailored goods that meet the needs of a customer is something that is very difficult to do via traditional manufacturing; mass customization at a lower cost is arguably the greatest benefit 3D printing offers. Practically any consumer-targeted industry can enhance its product development and boost competitiveness: consumer electronics, sportswear, toys – you name it, with 3D printing it is entirely possible to make it all. Additionally, the recent 3D printing boom plays an important part in market research.
Healthcare
Medical applications of 3D printing range from bioprinting to prosthetics, orthotics to dentistry, producing pills to implants. One additive manufacturing method used in this field is 3D bioprinting, a type of additive manufacturing in which ‘bio-inks’ (cells or any biocompatible material) are used to fabricate tissues or organs, layer by layer, to imitate the natural behavior of the original living structure.
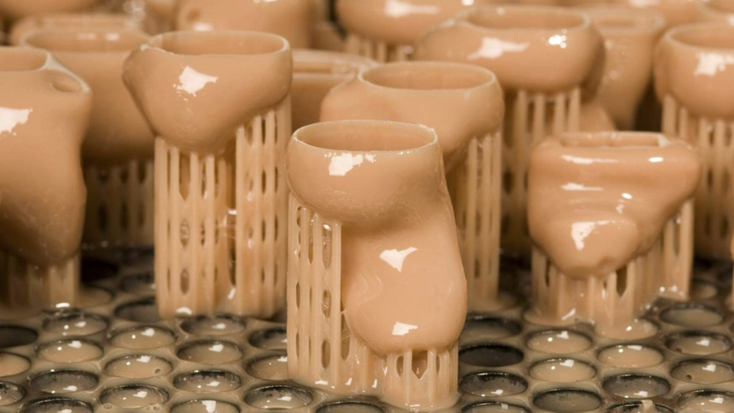
Custom hearing aids being 3D-printed. Image source: https://www.whiteclouds.com/3d-technology/3d-printing
Prosthetics have been reimagined with 3D printing, enabling doctors and engineers to create prostheses fully customized to the wearer, whether for a patient who has suffered limb loss, a form of cancer, or congenital disease. Until recently, many people didn’t have the option of a high-quality prosthetic – the whole process would mean painful amounts of time and money invested, with no guarantee of a truly satisfying result. With 3D-printed prosthetics, perfectly fitting assistive devices have become much more available. Another good example is dentistry, which has adopted 3D printing to create cost-effective implants and dental appliances.
Building
The advantages of 3D printing in construction include allowing never-before-seen accuracy and complexity when building residential, industrial, or public structures. Typically, the process involves creating a 3D model of any aspect of a building that can be 3D printed, then choosing the most suitable material for the job, the actual printing, and, finally, assembly in a factory or even right at the construction site. It is entirely possible to 3D print construction components by extruding cement, concrete, and foam, or bonding different types of polymer powders.
“Printing” the entire building is a reality now, too: notable examples of this include apartment complexes and office buildings in China, the United Arab Emirates, the Netherlands, and the United States. In 2016, the very first 3D-printed pedestrian bridge in Madrid, Spain, marked a milestone for the construction sector and civil engineering. Not only does 3D printing in construction boost functionality, and reduce human error and waste, it also promises to create more housing, which could enhance solutions for complex societal problems such as overpopulation or homelessness.
Food
While we wish we could tell you 3D printing was the solution to tackling world hunger, we’re not quite there yet. What is well underway already, however, is how 3D printing helps the food industry in development stages. It comes in handy when creating food processing and food production machinery, as well as limiting food waste when testing this equipment.
Although the types of food available to print are limited due to printing techniques, factors such as selective 3D printing restaurants and the availability of different food printers on the market indicate considerable adoption from both consumers and makers. Material extrusion would be the most common method used with viscous “inks” such as dough, fruit or veggie puree, chocolate, cheese – anything that could be of a semi-liquid consistency.
While these dining opportunities are exciting to hear about (or to be served on a plate), one significant drawback of 3D food printing is that it is far from scalable, and is currently used mainly for personalized fine dining. Still, examples of socially valued projects supporting plant-based proteins or treating malnutrition are present, and are only continuing to grow.
The future of 3D printing
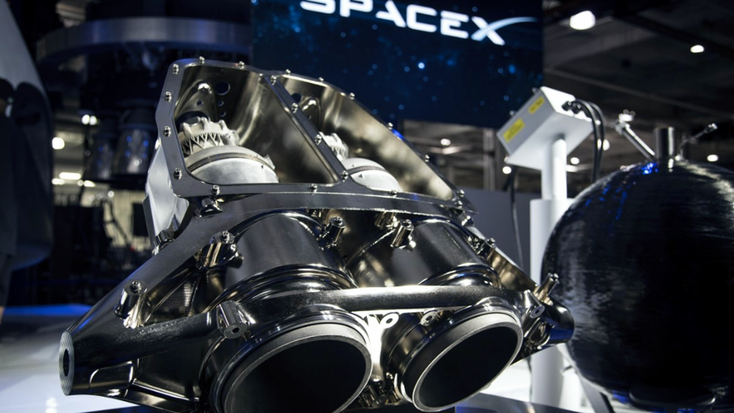
3D-printed SpaceX Crew Dragon Super Draco Engine. Image source: www.whiteclouds.com/3d-technology/3d-printing
In recent years, much research and practice has been put into turning the next-big-thing excitement surrounding 3D printing into a more practical everyday reality. In the process of advancing from an emerging technology to one of the engines of today’s manufacturing processes, the industry has matured. Its practical applications in the modern world seem boundless – from gadgets and artwork to aircraft components and transplantable organs.
Apart from being a great way for businesses to streamline their prototyping technology, additive manufacturing is now much more relevant for non-tech users as 3D printers become more available, and 3D software more user-friendly. Embraced by designers and DIYers, teachers and students, 3D printing enables the creation of customized products with no need for pricey or complicated industry-level infrastructure.
You might wonder, then, why 3D printing has not become as common as shopping online by now. Despite its popularity, there are still some obstacles that the industry faces including the cost of pre- and post-processing, and a limited choice of materials. That said, many other challenges such as equipment and materials costs or lack of in-house expertise have shifted in the last several years, demonstrating opportunity for further growth.
The amount of innovation 3D printing has already brought to manufacturing, supply chains, and design possibilities is indisputable: in a very short time, the technology has made massive leaps forward across multiple industries, with businesses gravitating towards smarter, faster, more efficient and environmentally friendly manufacturing.
Affordability, boosted productivity, products perfectly made for you – these are only a few benefits 3D printing will continue to bring. With its relevance ever-increasing, 3D printing may go as far as being a driving force in the global economy.
And when it does, we’ll say we told you so.
Read this next
More from
the Learning center
3D printing is no longer just a concept; today, businesses are using it to gain a competitive advantage. As industry players flood the market with proprietary devices, software, and materials, navigating that space can be quite a challenge. So we’ve put together a few things to consider before investing in an industrial printer. We cover some of the most prevalent technologies in industrial 3D printing, with at least one 3D printer in each category to give you a benchmark as you begin your search.
Different types of 3D printing software can be used on their own or in combination to take you through the entire 3D printing process: from a 3D model to a brand new 3D-printed object. In this article, we review the best 3D printing software you can use to design your 3D model, edit, repair, and slice your file, and then print an outstanding final piece.
When it comes to 3D printing, your 3D scanner plays a crucial role alongside the right software. Here’s a guide to the best 3D scanners, put together to help you find your perfect solution and make the most of it so you can get 3D-printer-ready digital models in nothing flat.