How Curtis Cabs turbocharges their reverse engineering with Artec Leo
Challenge: An industry-leading custom cab enclosure maker needed to speed up their reverse engineering workflow to meet deadlines and keep up with rising levels of market demand.
Solution: Artec Leo, Artec Studio, Geomagic for SOLIDWORKS
Result: The company’s design and engineering team reduced their scanning speed for one vehicle from 4-8 hours down to under an hour, and scan processing that used to take 2-3 days to complete per vehicle is now finished in less than one hour.
Why Artec: Being able to scan without any cables or laptop to get in the way means quickly taking Leo wherever they want to go, then capturing millions of data points per second with every sweep of the scanner, while watching the scan appear in real time on Leo’s rear touchscreen display.
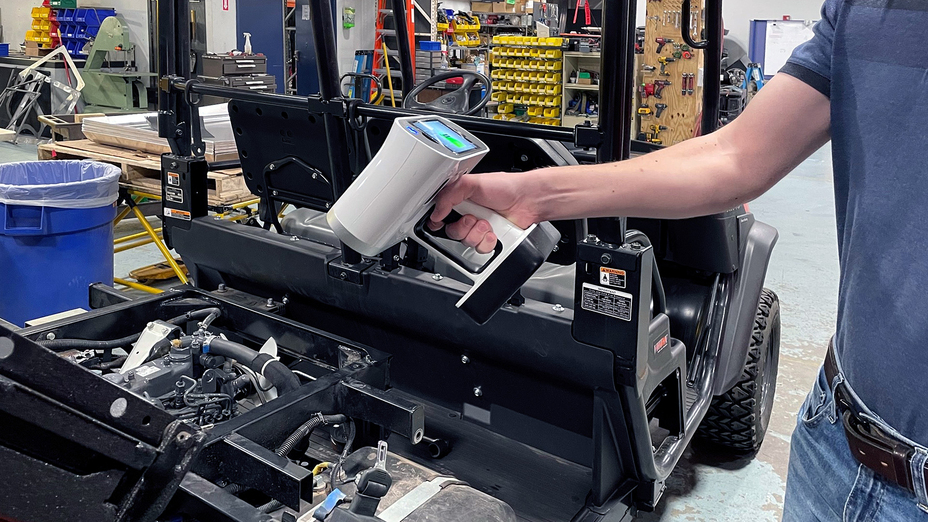
Image courtesy of Curtis Cabs
In the beginning, they were astonished. With their new Artec Leo 3D scanner in hand, the Curtis Industries design engineering team never expected it would slash a full 38 hours off their scan-to-CAD workflow for just one project. But it did.
And they soon discovered that Leo’s benefits went way beyond a few dozen hours of time saved with each and every scanning job.
Since 1968, this Massachusetts-based company has been an innovator and leader in the design and manufacture of custom aftermarket cab enclosures for tractors, UTVs & golf cars, snow & ice removal equipment, and more.
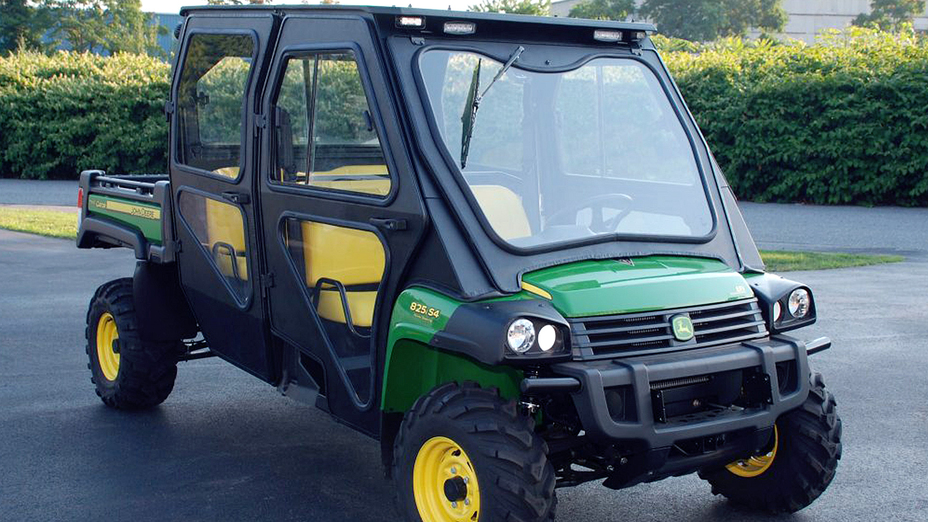
A Curtis Cabs John Deere Gator XUV cab enclosure. Image courtesy of Curtis Cabs
Maintaining the highest standards of quality
When it comes to Curtis Industries product lines, achieving a perfect fit is everything. In the words of Steve Smith, the company’s Design Engineering Manager, “Our custom cabs are made to interface with vehicles as if they’re a natural extension built together from the very beginning.”
“Every single weather seal, bracket, mounting hole, window, and door needs to be in exactly the right place with the right dimensions, without exception.”
“Because of this,” he continued, “our cabs provide operators with maximum comfort and protection from the elements for years of service. To make this happen, every single weather seal, bracket, mounting hole, window, and door needs to be in exactly the right place with the right dimensions, without exception.”
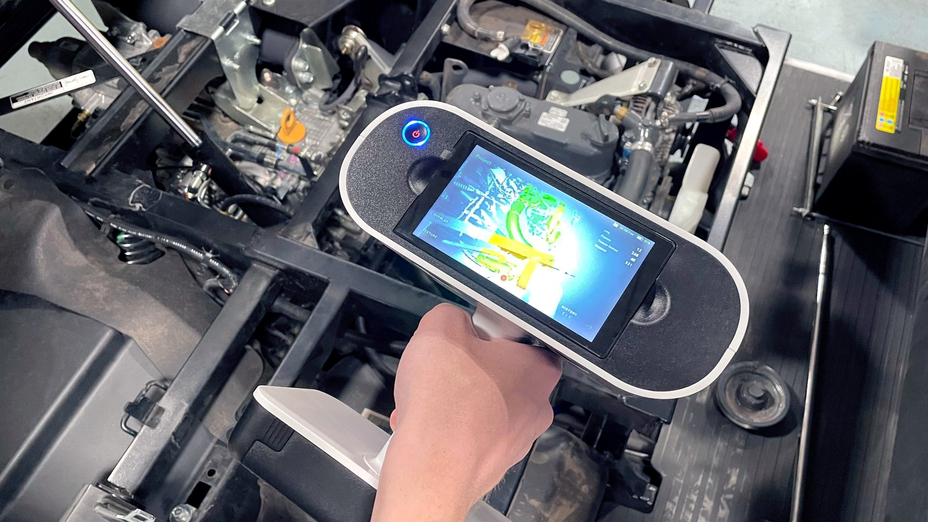
3D scanning the engine compartment of a Kubota utility vehicle with Artec Leo. Image courtesy of Curtis Cabs
With an impeccable reputation from coast to coast, in order to meet the ever-rising market demand as well as their own stringent deadlines, Curtis Industries and their design engineering team relentlessly pursue any possible ways to improve their products and workflows, including one of the most crucial for them: their reverse engineering process.
The reverse engineering workflow
The first stage in their enclosure design workflow requires reverse engineering the specific model of vehicle that the new cab enclosure will be made for.
In order to guarantee a snug and resilient fit with every surface their cabs come into contact with, Curtis’s design engineers need precise measurements of the target vehicle, which will then be used in the next phase of the process, where a prototype CAD model of the enclosure is created from these measurements.
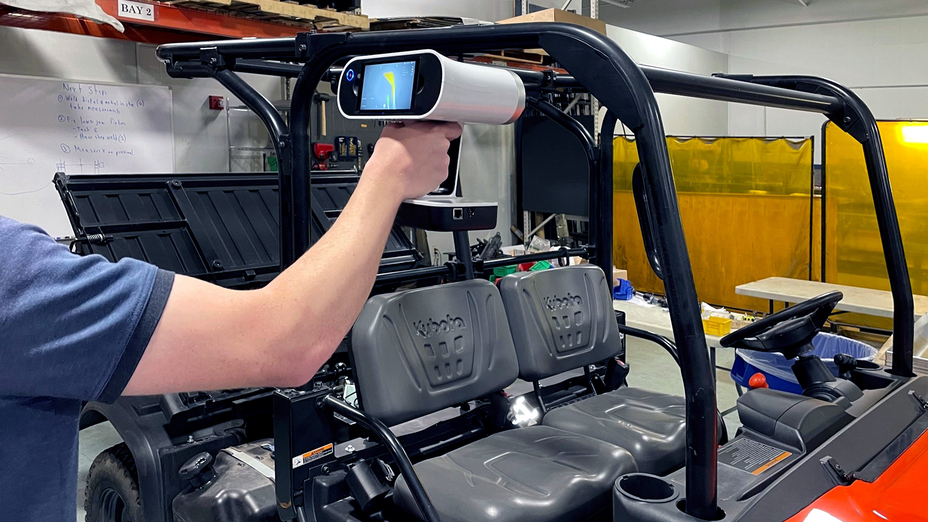
3D scanning the roll bar of a Kubota utility vehicle with Artec Leo. Image courtesy of Curtis Cabs
To accomplish this in the past, they used a collection of tools including tape measures, calipers, plumb bobs, and a coordinate measuring machine (CMM) arm.
From CMM to Artec Leo
Although the CMM arm delivered adequate measurements via its scans, the arm’s slow operation speed, heavy mounting plates, and limited reach made every job a prolonged and tedious chore, not to mention the device needed to be repositioned at least 4 times throughout every session.
With a typical CMM session demanding 4-8 hours to complete, that was just the beginning. Those same CMM scans would entail another 2-3 days or more of processing before they were ready for use by Curtis’s design engineers.
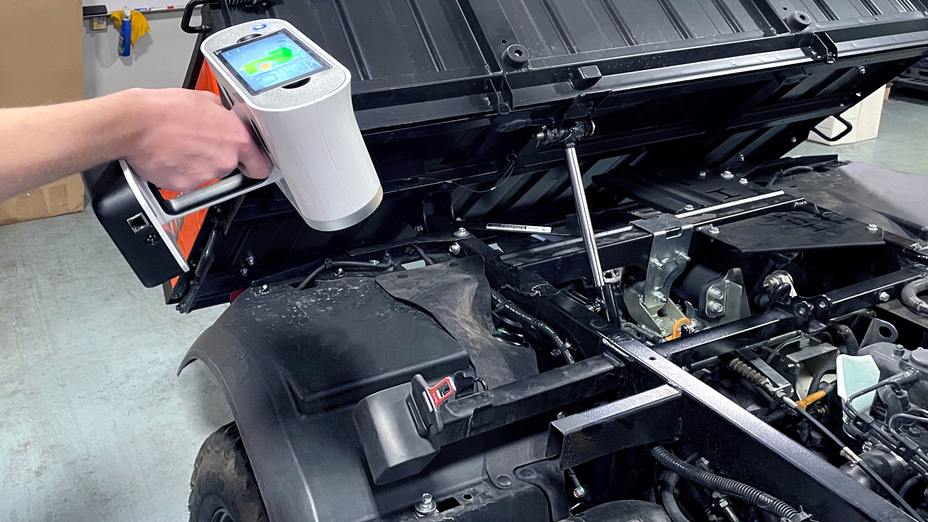
3D scanning the engine area of a Kubota utility vehicle with Artec Leo. Image courtesy of Curtis Cabs
Understanding that this segment of their workflow was a bottleneck for his team, Smith began searching for a better solution. His research brought him to 3D scanning, and just hours later he connected with Bo Helmrich of Artec Ambassador Digitize Designs, who told him about the Artec Leo, a professional 3D scanner that could bridge the gap for them.
Just one scan is all it took
Since seeing is believing, Helmrich drove long-distance through a blizzard to meet with Smith and his engineers at their facility in Massachusetts. There, as a demonstration of Leo’s abilities, he scanned a large tractor.
Smith and his team were delighted to see how easily and fast Helmrich was capturing the vehicle, with millions of data points acquired with every sweep of the scanner, all without any cables or extra laptop to get in the way.
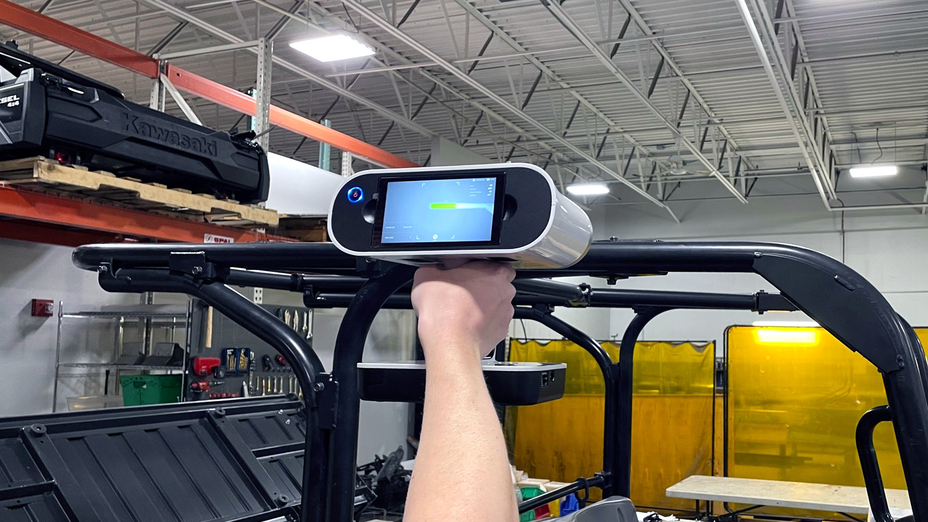
3D scanning the upper roll bar of a Kubota utility vehicle with Artec Leo. Image courtesy of Curtis Cabs
With Leo’s built-in touch screen, Smith and his team watched the scan of the vehicle appear in real time, delivering immediate confirmation that all the needed geometry and features were being captured.
Minutes later, exporting the scans to CAD
Minutes later, Helmrich showed them how it was a snap to export the scan data from Artec Studio software right into SOLIDWORKS via the Geomagic for SOLIDWORKS plugin. Once there, the vehicle’s surface scans were smoothly turned into a CAD model by adding planes, cylinders, and other reference features.
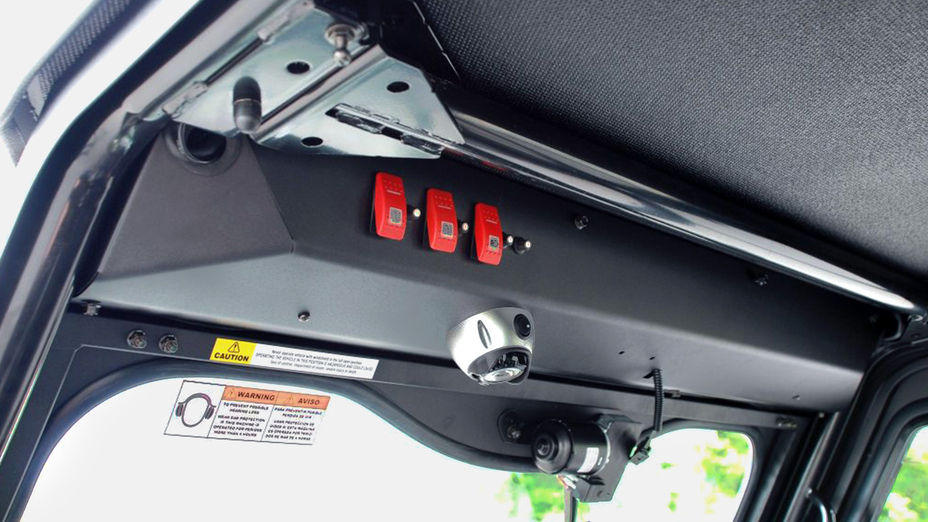
Interior panel and roll bars of a Curtis Cabs John Deere Gator XUV cab enclosure. Image courtesy of Curtis Cabs
“This is a massive leap forward in our design-to-build workflow.”
“We were amazed at how fast and painlessly Leo scanned everything, compared to what we were used to in the past with our CMM. Because we design our products around scanned vehicle data, for us this is a massive leap forward in our design-to-build workflow,” said Smith.
Curtis Industries made the decision to buy their Leo that same day, without hesitation.
Putting Leo to the test against the CMM
Wanting to quantify the significant changes that Leo had already brought to their scan-to-CAD process, after they made the purchase, Smith and his team went back to their traditional CMM-centered approach and timed every step of the process of scanning a vehicle for designing a new cab enclosure.
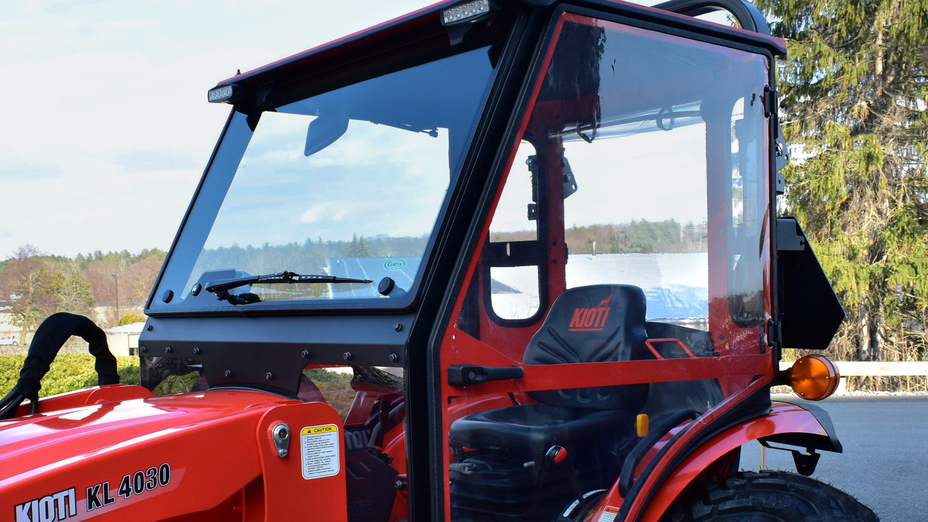
A Curtis Cabs Bobcat CT20 custom cab enclosure. Image courtesy of Curtis Cabs
Then, with their Leo, they injected it into the very same workflow with the same vehicle, timing this process as well. The contrast, to put it lightly, was stunning:
Scanning speed: what used to take them 4-8 hours to measure with a CMM now requires under an hour with Leo.
Volume of surface data: unlike the CMM arm that measures a handful of features, Leo captures all the surfaces being scanned, recessed features, and irregular shapes of a vehicle, making it easy to use this wealth of geometries in CAD as accurate reference models for creating their new product designs.
Scan processing: plummeted from 2-3 days or more with CMM scans to now under an hour with Leo, on a per-vehicle basis.
The golden synergy: portability and ease of use
Smith and his team have welcomed Leo’s ease of use and short learning curve, making it simple to teach to new members of the design team. Not to mention Leo’s portability.
“With Leo, anytime we want, it’s a cinch to carry it over or drive it out to a vehicle, whenever the need arises.”
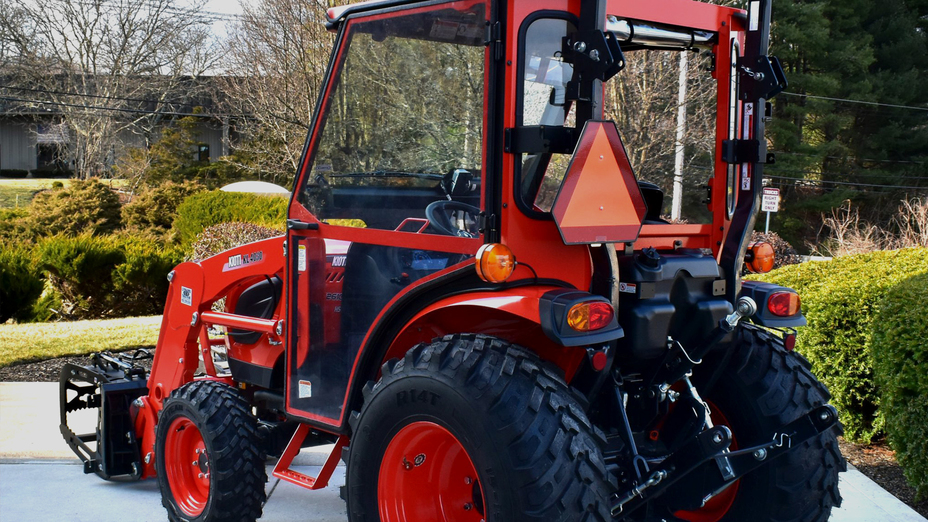
Rear view of a Curtis Cabs Bobcat CT20 cab enclosure. Image courtesy of Curtis Cabs.
In comparison with the heavy and cumbersome CMM, which demanded bringing the vehicles to it for scanning, Smith said, “With Leo, anytime we want, it’s a cinch to carry it over or drive it out to a vehicle, whenever the need arises.”
As devoted Leo users, in the months and years ahead, Smith and his team are looking forward to focusing their Leo on more and more applications throughout the company, including reverse engineering vehicle parts and tractor attachments, and more.
Scanners behind the story
Try out the world's leading handheld 3D scanners.