Artec-validated construction material offers glimpse of a sustainable future
Challenge: Discovering if a novel sugar-based biomaterial can breathe new life into a 300-year-old building block design and turn it into a viable modern construction tool.
Solution: Artec Leo, Artec Studio, SOLIDWORKS
Result: An innovative inspection workflow, in which Artec 3D scanning is used to check cast slabs for deformities. Digitizing and analyzing over one hundred samples has yielded the insights needed to perfect the ‘Sugarcrete®’ formula. It can now be used to build blocks with consistent properties, ready for deployment in sustainable architecture projects worldwide.
Why Artec 3D?: Leo’s speed, built-in display, and wireless configuration make digitization quick and easy, even for 3D scanning newcomers. It’s this user-friendliness, alongside an incredible level of accuracy and precision, that allows users to tackle complex inspection tasks.
Cheap and easy to make, cement is incredibly popular. In fact, besides water, cement is the most utilized resource on Earth. But it’s also a significant factor in global warming.
To make construction concrete, you first need to create cement by firing limestone, clay, and other materials in a kiln, as part of an energy and CO2-intensive process. When you factor in the damage caused by ingredient mining, transport emissions, and the impact concrete-covered cities have on our health, cement is now one of our planet’s biggest eco-villains.
While major industry players try to counteract their colossal carbon footprints, either with carbon capture or green energy, others are seeking to replace cement in construction altogether.
Straw, bamboo, and even eggshells have been considered as alternatives. Often, it’s proposed that experimental materials be 3D-printed as well, to cut waste. However, trial success stories aside, nothing has dislodged cement from its role at the heart of modern construction.
Sugar: Our sweet eco-savior?
One of the latest, most innovative approaches to tackling this thorny issue, is being honed at the University of East London (UEL).
Alongside sugar refining experts at Tate & Lyle Sugars, the UEL team are working on a substitute based on a sugarcane byproduct. You may well ask: ‘Why sugarcane?’ As it happens, sugarcane is the world’s most-picked crop.
Almost two billion tons are harvested worldwide each year, leaving behind 600 million tons of plant stalks crushed into a pulp-like mess called ‘bagasse.’ Until recently, this was largely disposed of, but it is increasingly being repurposed. Generally, the material is reused as a biofuel, but the UEL team believe it may also have construction potential.
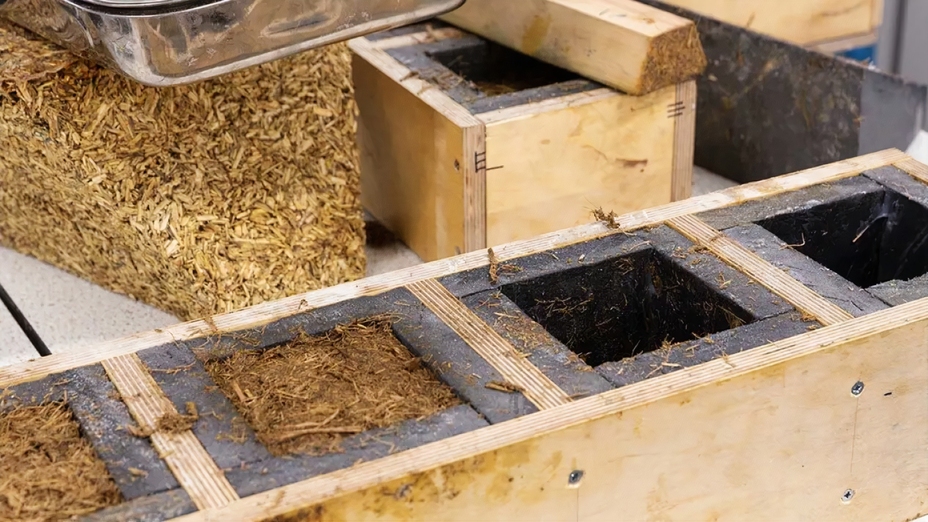
A close-up of the Sugarcrete® block-pressing process. Photo by Chromaphotography, provided courtesy of UEL
In their efforts to realize this potential, the team have developed a material 4-5 times lighter than brick, with a 15-20% smaller carbon footprint. But rather than making bricks from their formulation – which they’ve named Sugarcrete® – they’ve worked with architects at Grimshaw to revive a design from 1699.
That year, French architect Joseph Abeille introduced dry assembly flat vaults made up of interlocking slabs, which slotted together to transfer loads across their collective surface. The team’s revamped design now features post-tensioned perimeter ties, which reduce its reliance on steel by up to 90%, making it an ideal basis for eco-friendly infrastructure.
However, as they started to press Sugarcrete® blocks, the UEL researchers encountered a significant amount of shrinkage. With the construction industry being so highly regulated, the team needed a way of measuring, quantifying, and tackling this. The answer? A unique R&D process accelerated and validated by high-speed, precision Artec 3D scanning.
Digitization at UEL’s ‘Fab Lab’
Fortunately for the Sugarcrete® team, UEL is now home to a Digital Fabrication Lab packed with digitization tools, including Artec Eva Lite, Artec Eva, Artec Space Spider, and Artec Leo.
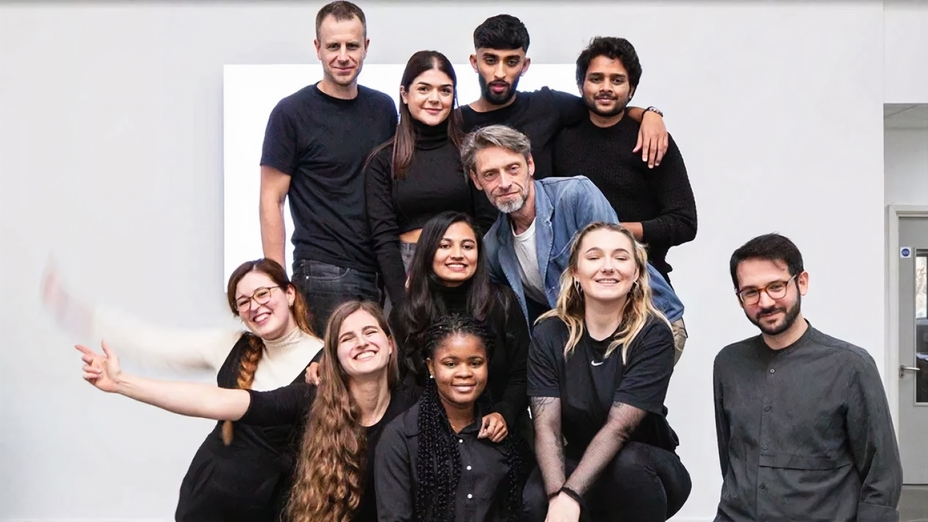
The Sugarcrete® development team. Photo by Chromaphotography, provided courtesy of UEL
Since 2006, Artec Gold-certified partner Patrick Thorn & Co. has helped UEL expand from a handful of milling machines to an industry-ready facility, providing training along the way. With this Fab Lab’s devices, students have already found it possible to digitize everything from art to outdoor environments for monitoring purposes, while achieving exceptional results.
In this case, its developers deployed the industry-first wireless Artec Leo to evaluate Sugarcrete® prototypes. Its lack of cables and built-in display made it incredibly maneuverable and easy for newcomers to get to grips with. The device’s sky-high accuracy and precision also allowed them to identify each block’s exact shrinkage and uncover a solution: an improved recipe.
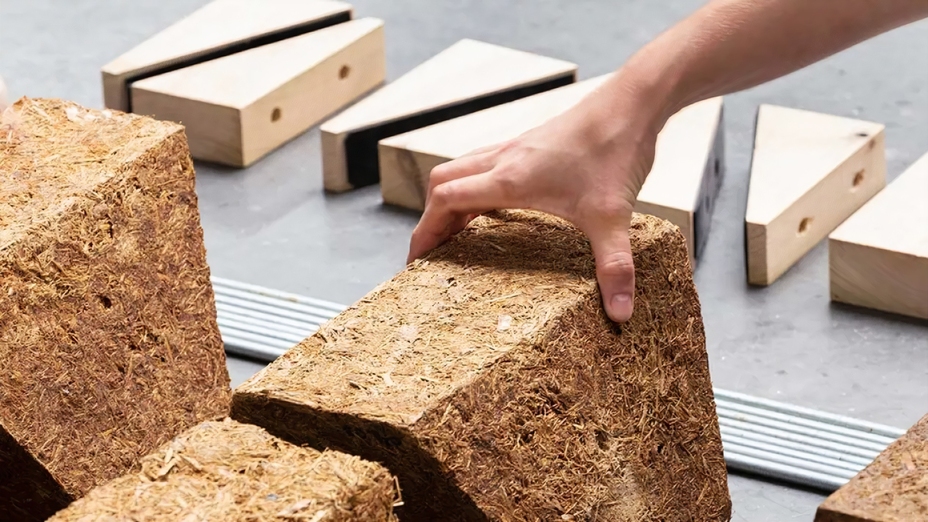
A Sugarcrete® building block being slotted together. Photo by Chromaphotography, provided courtesy of UEL
“We had used lime, a standard building material with less carbon than cement. But it features water content, which tends to shrink,” Alan Chandler, Co-Director of UEL’s Sustainability Research Institute explains. “Now, we use a waterless silicone binder that ‘glassifies’ the mixture, giving you less deformation and more compressive strength.”
“It was particularly useful to be able to capture the finished material. With Artec Leo, we have proved how Sugarcrete® slabs can have enhanced properties.”
Building from theory into reality
Artec Studio has also been central to the Sugarcrete® project’s success. Using features like Autopilot, which automates many manual data processing steps, students in the team were quickly and easily able to go from scan to highly detailed 3D mesh. Artec Studio’s close SOLIDWORKS integration also made the scan-to-CAD process a simple one.
With direct mesh export functionality, files can be sent to SOLIDWORKS in a single click. This integration proved a real timesaver, as the team ultimately had to turn over one hundred block meshes into CAD models. According to Chandler, this was crucial to “unpacking the differences” between samples, avoiding generalizations, and ruling out defects caused by pure chance.
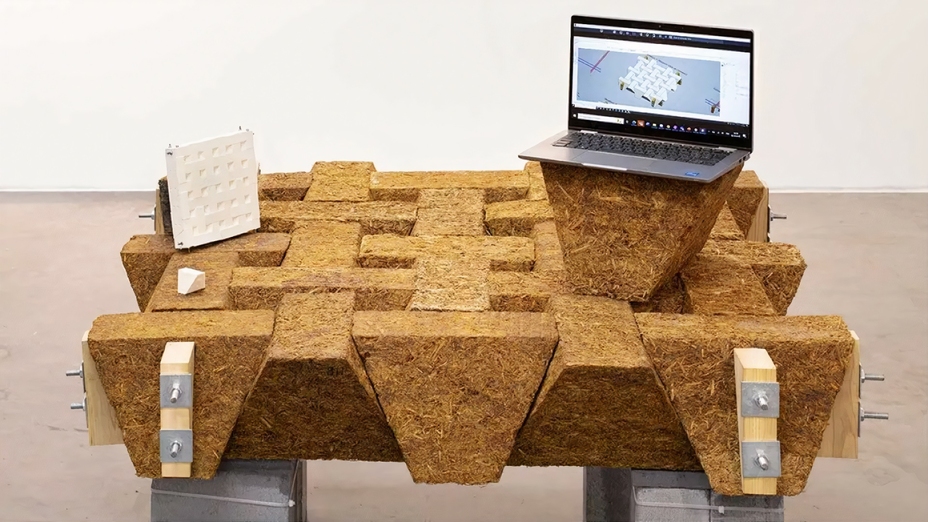
A complete Sugarcrete® slab with a 3D model of the end design. Photo by Chromaphotography, provided courtesy of UEL
As the team works with Tate & Lyle Sugars to identify application opportunities in the sugar-producing world, he adds that Artec 3D scanning can now aid the aims of UEL’s Sustainability Research Institute – in design optimization, performance modeling, and lifecycle analyses (LCAs).
“Measuring block shrinkage is no longer a theoretical exercise, it has become a practical one,” concluded Chandler. “You can predict load paths on a computer, but it’s far easier to digitize and look at the variables. With 3D scanning, we want to be able to link LCAs to building performance and design. It’s not just about data looking good, it’s about doing good.”
“We’ve had to go beyond the theoretical. Being able to assess our approach using very accurate Artec 3D scanning has allowed us to see how blocks behave in reality.”
Want to find out more? You can read the full Sugarcrete project breakdown here.
Scanners behind the story
Try out the world's leading handheld 3D scanners.