Artec Leo brings 3D scanning to new heights: 185 feet over San Francisco Bay
Challenge: After decades of exposure, general wear and tear, and constant proximity to some of the world’s most damaging elements, heat and the sea, the rusty panels of San Francisco’s Richmond–San Rafael Bridge needed to be replaced. With no reliable drawings or measurements of the panels available – the bridge was constructed in the 1950s – accurate information from these panels needed to be obtained. With just one catch: These panels are part of a 5-lane bridge that serves an estimated 80,000 cars daily, and towers 185 feet (56 m) above the San Francisco Bay.
Solution: Artec Leo, Artec Studio, Geomagic Design X, Autodesk
Result: Wireless and equipped with an inbuilt touchscreen, Artec Leo rose to the challenge and, untethered by cables or a computer, easily scanned the eight panels. With all the necessary measurements and information obtained, replacement panels were manufactured. For quality control and future reference, the newly installed panels were then scanned, too.
Why Artec? With Artec Leo fully operational without cables, wires, or the need for computers or other equipment during scanning, all data required was easily and fully captured with minimal disruption to traffic.
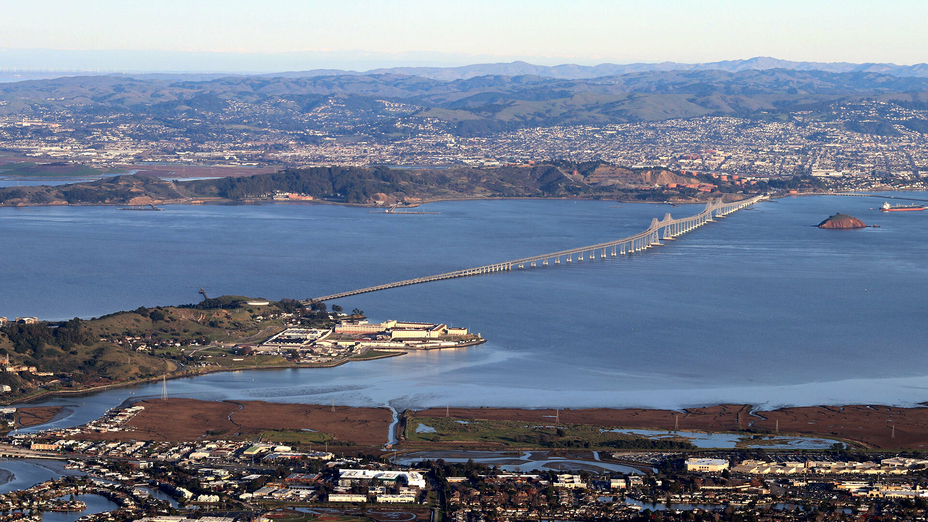
Against the backdrop of 1950s California – a post-war boom of changing times and industrialization even as Beat poets scratched pen against paper in now-iconic bookstores – the Richmond-San Rafael Bridge was being brought into existence. Plans for such a bridge had begun much earlier than that, though – as early as the 1920s, the need for a connection between San Francisco’s eastern and western bays was identified, an idea that was proposed, approved, delayed, amended, and put off numerous times, and for decades to follow.
It was then, with much anticipation and a need increasing as quickly as the state’s growing population, that plans were agreed upon, and construction of what is officially named the John F. McCarthy Memorial Bridge began.
Designed to replace a ferry service linking Richmond on the east side to San Rafael on the west side, construction began in March 1953, and by September 1956, the bridge was open, fully functional, and ready to receive guests – in this case, tens of thousands of drivers who at last had a way to easily cross the bay.
The bridge has remained operational ever since, transporting, at last count, more than 70,000 drivers from one side of the bay to the other every day. And while the bridge is of course both functional and picturesque, its location makes it vulnerable to an impressive collection of incredibly corrosive elements: saltwater, heat, wind, and vehicle exhaust.
“While working on bridges, an engineer shared an expression with me: Rust never sleeps,” said Marcio Adamy of Indicate Technologies Inc., an Artec 3D Gold-certified Partner.
To keep the bridge at its safest and most functional, some repair was in order. One specific section of a particular segment had become especially corroded and rusty over time, and it was this part of the bridge that needed to be replaced.
“The client wanted to measure the panels, and the location of their rivets, and there were over 250 rivets on each panel!”
With no known measurements available (and even if there had been measurements, their reliability would’ve been questionable) a new task presented itself: to calculate the exact measurements of these panels, a daunting task requested by Danny’s Construction, a company that specializes in steel and the manufacturing and maintenance of huge structures such as stadiums, buildings, and in this case, bridges.
“They wanted to measure the panels, as well as the location of their rivets, and there were over 250 rivets on each panel,” Adamy said. “Each panel has north and south sides, as well as exterior and interior parts. So to produce new panels, they needed to make sure the measurements came with all the right holes in exactly the right locations.”
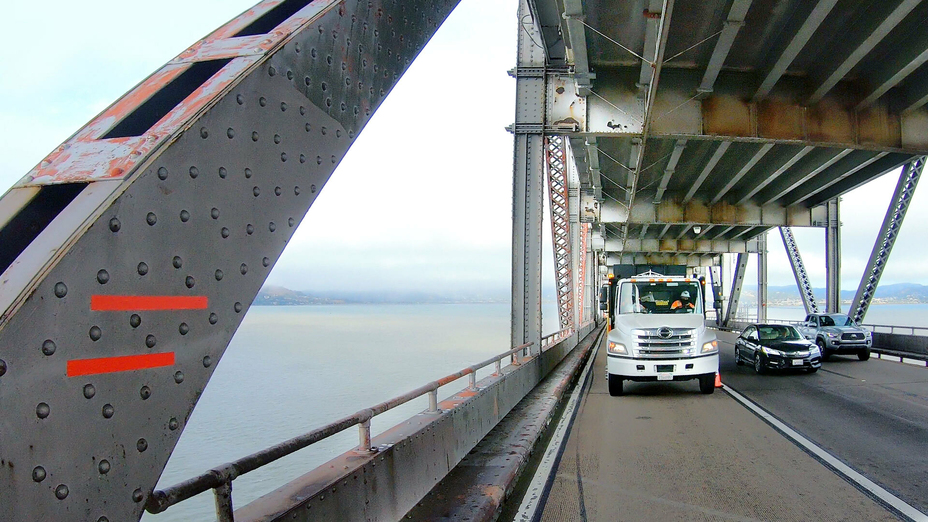
Each panel had 250 rivets, each of which needed to be accurately captured.
With this came two challenges: the height of the bridge, and the fact that, well, it transports 70,000 cars every day. The solution needed to be fast, fuss-free, and self-contained, all while making sure the final results were accurate and reliable.
The only solution
When it comes to accessing these particular panels of the Richmond–San Rafael Bridge, there are several things that need to be considered. Firstly, the parts that need to be measured are 185 feet (56 m) above the water. Next, there is constant traffic throughout the day. Let’s not forget the fierce winds that are wont to rage across the bay, as well as the need to be as minimally intrusive as possible – whale mating season, for example, restricts any near-water activity lest the lustful whales get distracted.
In a nutshell, someone needed to be able to quickly and safely slip out onto the outer-facing section of the bridge while remaining protected from oncoming cars, causing as little disruption to traffic as possible and – given the height they’d be operating at – remembering not to look down. And then, to capture every single surface detail of each panel.
There was but one solution that was up for the task: the Artec Leo.
Completely wireless and designed to easily capture the trickiest corners, Artec Leo’s inbuilt screen makes it a cinch to capture every surface of an object, and all the details within. In the case of the Richmond–San Rafael Bridge, there wasn’t any other device that could do the job: working with Leo means that’s all you have with you – an essential consideration given the nature of this job. It simply wasn’t an option to be that high up, and in such a small space, with that brief amount of time to get the job done, all while fussing over computers, cables, and perhaps another person on standby, ready to assist.
“There was no other solution. Artec Leo was designed for this.”
While in other situations using a different scanner or a combination of scanners might have been an easy solution, in this particular case, the answer was clear. Adamy said, “I was in this basket, maybe three feet by one foot, with another person. Where would I put the computer, or any table? So in this specific case, there was no other solution. Leo was designed for this.”
All the work was done in record time – and in HD Mode, too. “I made a decision to scan everything with HD Mode, though it wasn’t really necessary to have such rich geometry in this case,” Adamy said. “But I always like to have the best and then reduce – instead of not having enough information but not being able to add anything else later.”
After the team had some practice on the best and most efficient way to scan each panel, they got it down to less than ten minutes per side.
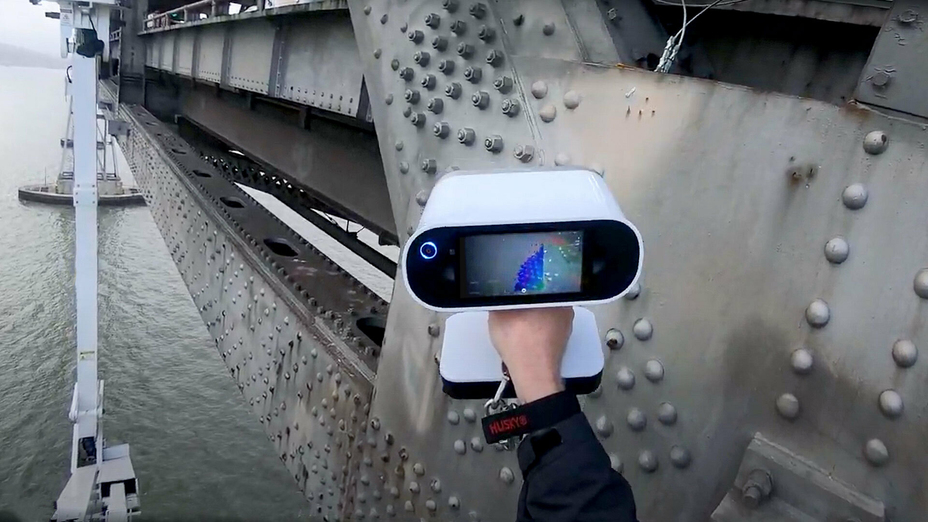
56 meters above the water, the job had to be done quickly, safely, and with no extra baggage such as computers or cables to get in the way. The answer: Artec Leo.
“I had a small gap of time when I was allowed to work on the bridge,” Adamy said. “I would arrive around 5:30 or 6 am, and we’d plan what we would do. Then I put on my harness, helmet, and safety equipment. And then I’d stay there scanning until about 9:30 to 10:30 am, and then drive back to the office and start to upload the files,” Adamy said.
Given the tight time slots available for each scanning session, the amount of scanning that needed to be done, environmental restrictions in place, and temperamental weather conditions, the entire project took several months to complete.
After eight trips, and less than 30 minutes of scanning each of the 6-foot panels from all directions, the first part of the job was complete: All panels were scanned, and the captured data was on its way to the next stage.
All in a day’s work
Even with all the planning that had had to be done, the safety personnel and policemen on standby, a crash truck to avoid collisions from oncoming traffic, and one man strapped into a safety harness while hanging over the San Francisco Bay, the job itself wasn’t one that was in itself difficult. Despite all the challenges and difficulties, scanning with Artec Leo was easy.
And so was processing the data.
“I uploaded the files, and ran all the steps,” Adamy described. “Then I ran global registration, deleted extra information that I didn't need, then I converted everything into a mesh using sharp fusion. And then I exported this mesh as an STL file.”
Following these fairly straightforward steps, the STL file would be uploaded to Geomagic Design X for further processing, then exported in .pts format, which was then used on Autodesk for SBU drawings and to collect information. In some cases, everything from the scanning to the processing, post-processing, and final result was done within the day.
“The only hard thing was being there: managing your fears in this environment with the wind, cold, and sun!”

The hardest part of scanning here? The height!
“Like I said, this part is a very straightforward job: Upload files, run global registration, edit and create a mesh file, sharp fusion… it’s a no brainer,” Adamy said. “The only hard thing was being there: being beyond the crash truck, managing your fears in this environment with the wind, cold, sun, all that stuff. That’s the hardest part.”
Saving time and cost
And eight months later, all eight panels had been fabricated and proudly installed, with at least 75 to 90 percent of time saved – and that’s a conservative estimate. Using 3D technology and specifically Artec Leo as the chosen scanner came with more benefits than possibility and convenience – it cut down a whole lot of cost, too.
The amount of time saved, for one: say, for example, if each panel had to be manually measured with a tape measure or a ruler, with the laborious process of measurements documented by hand drawing, and then translated to manufacturers of new panels.
Because of how accurate the results are, time was also saved when producing the new panels, not to mention a reduced number of employees who needed to be present, which in turn cut down on labor costs, too.
One final step? To scan the new panels, of course. While we today may struggle with finding reliable information on structures and buildings erected many decades ago, professionals in the future will have no such problem.
In the case of the Richmond–San Rafael Bridge, full 3D scans, measurements, designs, and files on these panels are finally available – down to 0.1 mm accuracy, and for countless generations of engineers, builders, architects, and inspectors to come.
Scanners behind the story
Try out the world's leading handheld 3D scanners.