Dutch-Chinese history comes to life as Artec Eva and Space Spider help recreate 17th-century ceramics
Summary: In the city of Delft, The Netherlands, a designer works with Delft University to recreate 17th-century Chinese porcelain and produce new work based on centuries-old designs.
Goal: To convert original 17th-century vases into perfect 3D models and prints, and to conceptualize new designs based on ancient excavated artifacts.
Tools Used: Artec Eva, Artec Space Spider
In a country so vast in both its size and history, Chinese culture has today made its way into the international mainstream with everything from its cuisine to its technology becoming appreciated and explored. China’s delicate ornaments are no exception, most famously those made from porcelain.
Exported to the rest of the world from as early as the Han dynasty (206 BC–220 AD), the signature blue and white swirls and patterns have become synonymous with Chinese culture, or at least they have become one of its most easily recognized designs. The source of much of these centuries of porcelain: Jingdezhen. With most Chinese porcelain being produced in or around this southern Chinese city – rivers flowing both north and south eased the transport of fragile items – export was key for both domestic and international markets.
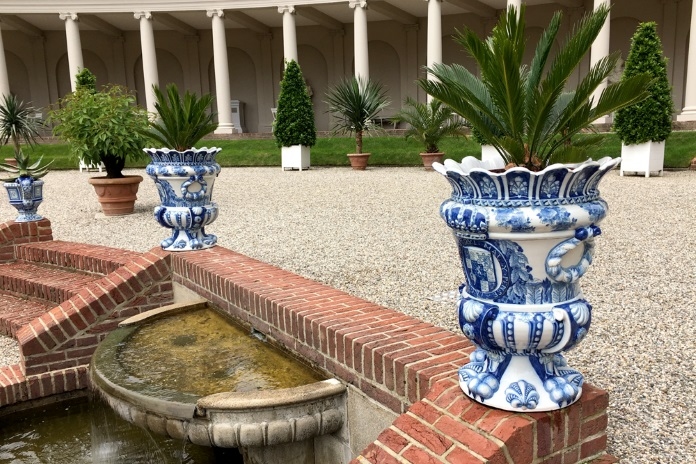
New technology was used to bring the old and valuable back to life.
From as early as the 15th century, there are records of Chinese porcelain being purchased by European travelers. By the 17th and 18th centuries, the East Asian market began to attract even more European companies with tea, silk, spices and, of course, porcelain. Between 1602 and 1682, the Dutch East India Company is said to have exported between 30 and 35 million pieces – more so than their English, Portuguese, and Swedish counterparts.
To bring history back to life, designer Maaike Roozenburg in collaboration with leading Dutch university Delft University of Technology – in this case specifically the Industrial Design faculty – used scanners provided by Artec Ambassador 4C Creative CAD CAM Consultants.
“The whole history of porcelain is fascinating,” says Roozenburg. “It’s this magical white material and something they invented in China. There was an obsession with it. Everyone wanted it, and in China, they started to really produce porcelain especially for western markets. All the royals in Europe loved it.”
In The Netherlands, Chinese porcelain was so loved and desired that Dutch ceramic artists set out to try and create an imitation. This resulted in what is known as Delftware, which became a notable industry of its own.
“In the 17th century, ceramic Delftware vases decorated the gardens of royal Het Loo Palace in Apeldoorn,” Roozenburg says. “But they are all gone. Archeologists found some bits and pieces, and scientific proof that they were there, together with drawings and paintings.”
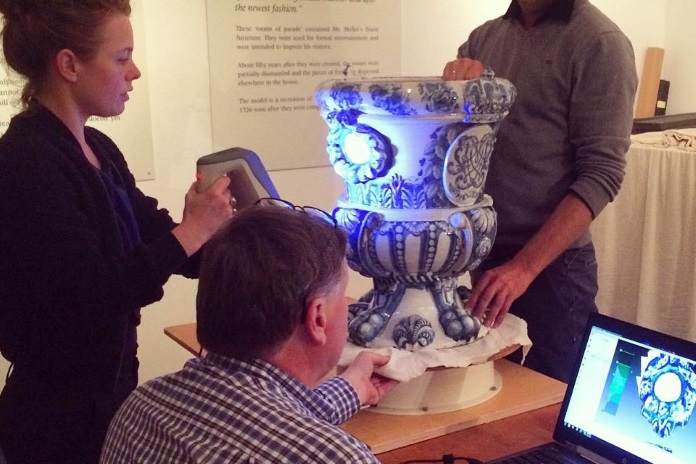
The only two remaining 17th-century vases weren't allowed out, so Artec scanners were brought in.
To recreate these Chinese-inspired Delftware vases, it was a matter of tracking down some of the originals. Throughout the world, only two were found: One in Erddig Hall in the UK, another in the museum of Schloss Favorite in Germany.
“Thank God, at the time, royals gave these vases as presents to other royals!” says Roozenburg.
With both locations unwilling to let their vases be taken out, the team traveled there to get the job done. “Once the castles found out they were the only ones who had them, they said ‘no, they will stay here,’” recalls Roozenburg. “So we went there with Artec scanners in our backpacks to these still-existing castles in Britain and Germany – and scanned them on the spot.”
“I think what’s amazing about scanning is that, by rendering physical objects that are really fragile, valuable, and have to stay within a museum into digital data, you can experiment with them,” says Roozenburg. “It gives new opportunities to work with historical objects that you otherwise would not be able to touch.”
During the scanning process, more challenges presented themselves – this time, it was a common scanning problem with the reflective nature of porcelain. “We expected it wouldn't work, but in the end Artec Eva worked much better than expected,” Roozenburg says.
Before deciding on Artec Eva, attempts were made with a CT scanner. This didn’t work due to the nature of the process: Radiation going through this scanner makes slices of the objects, one slice at a time, which are then put together with software. “It was not a smooth scan, and you’d have to do a lot of work after the scan,” she adds.
Artec Eva, an easy-to-use and highly precise scanner, is an excellent solution for capturing almost any medium-sized object, including those with shiny surfaces – an important benefit in the case of these vases. Its structured light scanning technology also makes it safe to use, and leads to precise, high-resolution measurements.
To make sure there wouldn’t be unexpected issues or setbacks, styrofoam models of the vases to be practiced on were made. “You don’t want any surprises when you’re in a castle in Britain and realize you have to improvise!” Roozenburg laughs.
To minimize the handling of the vase while making it more stable, a round platform attached to a small motor was assembled. The vase to be scanned was then placed on the platform and slowly rotated for a full and even scan with Artec Eva mounted on a tripod.
For the decorative ornamental additions such as lion heads and shells, Artec Space Spider was put to work. This scanner is ideal for smaller objects and intricate details, and with its extreme degree of accuracy and ultra-high resolution, Space Spider was the best choice for capturing such fine details and rich colors. After they were scanned, the ornaments were processed in MATLAB, where they were refined before being 3D printed.
“You cannot use the overall vase, you have to remove all the details and use different molds of different parts, refine them and scale them back,” Roozenburg explains.
To create the new vases, several stages of molding, printing, assembling and painting were required.
All the data was then brought back to the studio in Amsterdam for more work. For the body of the vase, post-scan processing was done in Artec Studio and MATLAB, Sketchup, and Geomagic Studio 2013 to create a detailed model from which the ceramic slip cast mold was formed using CNC Milling.
In terms of how the scans were post-processed in Artec Studio software, Bertus Naagen, lab manager of TU Delft’s Industrial Design department explains. "We followed all the standard steps, including Rough, Fine, Global, Outlier Removal, Sharp Fusion (by radius) for each separate scan, and then Small Object filter. After this, we aligned all the scans and applied Sharp Fusion (watertight). The final step was exporting as either STL or OBJ."
Another factor that was kept in mind: ceramic shrinks during the drying process, so the model had to be scaled up to compensate for the shrinkage. Once the vases were molded and the ornaments attached, the adorned vases were glazed and painted, one by one.
And so the goal was accomplished: new technology was used to bring the old and valuable back to life.
“The best thing is, in the end you can’t see that there was any new tech used. The finished work of 45 vases look like the originals, like they are brand new coming from the oven in the 17th century,” says Roozenburg.
Technical University scanning expert Naagen has worked with Roozenburg on a number of projects, and in this case, “recounting centuries of exchange between The Netherlands and China.”
With a keen interest in combining modern technology and heritage, Naagen says that his team is always enthusiastic in supporting projects that maintain the relevance of history.
“It’s culture,” he says. “We should make it accessible to people all over the world.”
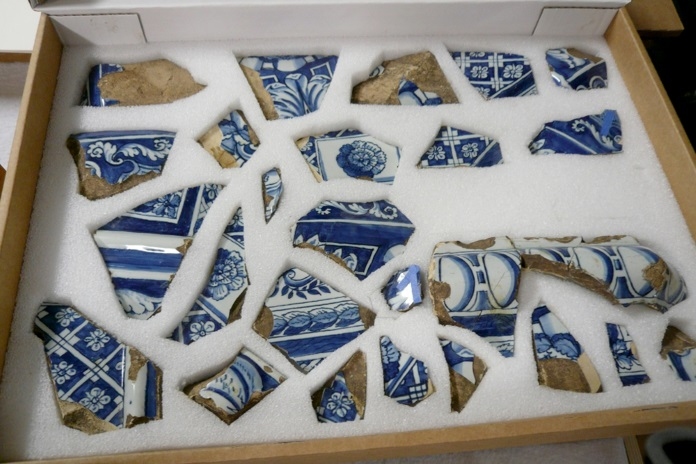
Every bit counts when getting the details of ancient artifacts right.
It was also here, specifically in the Dutch city of Delft, that porcelain cups, bowls, and dishes were discovered and excavated: the remaining bits of history from China, more remnants of a Chinese-Dutch trade route from the 17th century.
“17th-century glassware is really fragile and mostly broken. They’re in museums behind glass, and you’re definitely not allowed to touch them,” Roozenburg says. “I wanted to bring them back to kitchen tables.”
In contrast to the perfection of the vases, where the intention was to make perfect copies as close as possible to the originals, and to have these back in the gardens like they had never left, the aim here was quite a contrast: to show traces of history.
“I didn’t make perfect copies, I made replicas where you see cracks and imperfections. I didn’t fill gaps that were missing – in that sense it is more artistic and experimental,” Roozenburg says.
In collaboration with craftsmen of Jingdezhen, she has today created new designs based on these historical objects – presented as they are with cracks and blemishes, missing bits and imperfections.
Roozenburg set out with the intention of using new technology – Artec Space Spider – to remake and reintroduce these forgotten porcelain objects. “The whole scanning process is a tool, but it’s a tool you have to learn to work with,” she says. “You have to do it a few times to really learn and understand how this machine works and how it captures the world around you, which is an interesting process.”
With Artec 3D scans and printouts of the 17th-century porcelain, Roozenburg headed to China and asked craftsmen there if they could still make the tableware.
“What’s quite amazing is that having this new technology, you can render an object into digital data and bring it to the other side of the world,” Roozenburg says. As a guide for their own work, the craftsmen in China used Artec scans for design and texture while referring to photographs of original artifacts for greater detail.
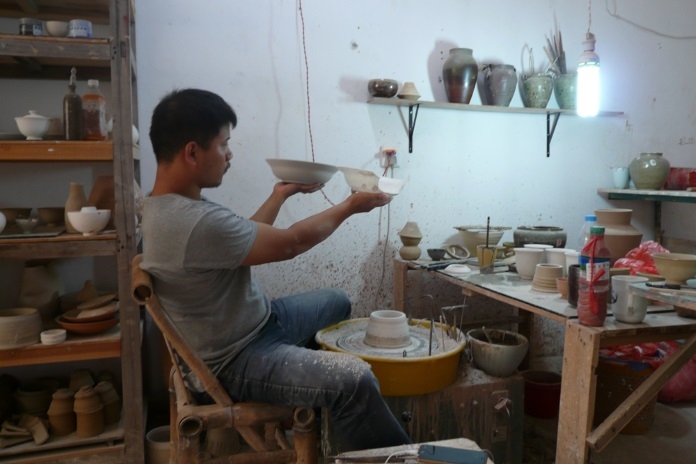
Craftsmen in China modeled the new bowls based on scans and photographs.
After the new items were made by hand, they were then scanned, modeled on screen, and printed out.
Roozenburg has since gone on to create a range of new designs based on the historical objects she has worked with, commemorating centuries of trade and exchange between The Netherlands and China.
While Roozenburg had previously used CT scanners which “needed far more post-processing and data processing,” this project was a first for her with Artec portable scanners.
“It was fascinating, learning to understand the scanner and its way of capturing reality. The way you can piece more parts of a scan together into one object worked really well and is accessible. The scanning itself was like ballet: experimenting with smooth movements and angles to capture the object."
Els Rappard-Oostland of Artec Ambassador 4C, sees Artec scanners being used everywhere from university hospitals to quality control for heavy machinery. In this case, she says, success comes in the fact that cups, bowls, and dishes were excavated in the city of Delft, yet produced in Jingdezhen, China, in the 17th century.
“This is great,” she says. “History has been brought to light with modern technologies.”
True replicas: to Delft and back is a project in collaboration with Archeology Delft, Delft Technical University, Museum Prinsenhof Delft, and International Studio Jingdezhen.
With special thanks to: Ir.Bertus Naagen, Dr. Steven Jongma en Adriaan Rees
Garden Vases Palace Het Loo: a project for the Dutch Palace Het Loo, in collaboration with Delft Technical University, Schloss Favorite, Erddig Hall, Royal Tichelaar Makkum.
With special thanks to: Ir.Bertus Naagen, Suzanne Lambooy and Jan Kok
Scanners behind the story
Try out the world's leading handheld 3D scanners.