Microsoft Flight Simulator, one of the most beautiful games in the world, uses Artec Leo to recreate ultra-realistic aircraft
Challenge: A video game developer needed to create an ambitious, ultra-realistic flight simulator.
Solution: Artec Leo, Artec Studio
Results: The game’s aircraft models are more lifelike than ever before, and the game has already become a worldwide sensation, acclaimed by professionals for its realism. The precision of the fuselage, cockpit, and landing gear has been confirmed by the aircraft constructors themselves.
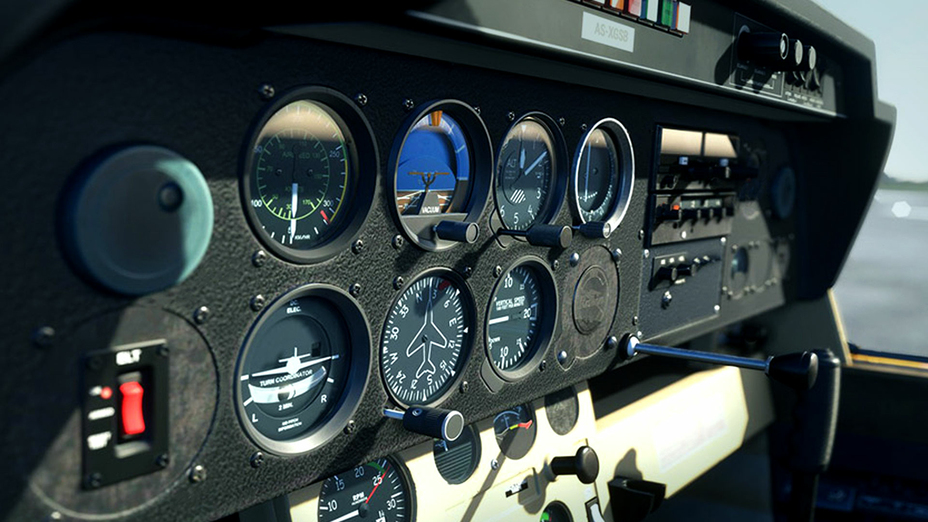
Cockpit view in the game Flight Simulator
Fourteen years following the last release of the world-famous flight simulation game, on Aug, 18, 2020, Microsoft and Asobo Studio unveiled the newest edition of Flight Simulator.
Already number one on the best-selling PC games chart since its release, Microsoft Flight Simulator is a worldwide hit, boasting more than 1 million unique players, with 26 million flights already having been flown in this super realistic simulation.
To recreate the game environment, the graphics, and the plane cockpits to the peak of perfection, Asobo Studio needed to faithfully include every last detail. This is even more important since the majority of players are pilots, passionate airplane enthusiasts, and other expert gamers with extensive knowledge of flight simulators.
3D technologies to help with performance imperatives
Engineers from Asobo Studio, France’s leading independent game developer for PC and consoles based in Bordeaux, used 3D scanning technologies to recreate with true-to-life precision the planes’ cockpits in the game, making even the tiniest details more realistic in this new release of Microsoft Flight Simulator.
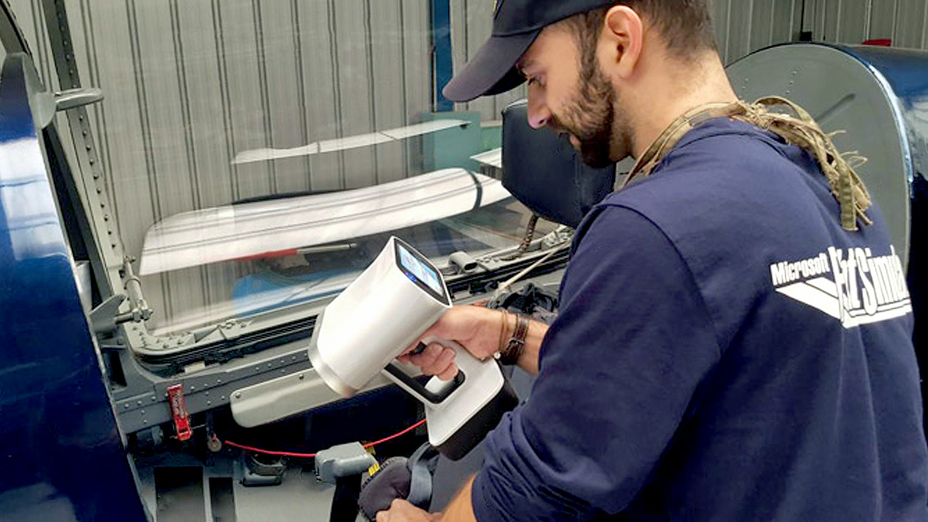
Asobo vehicle designer scanning the inside of an aircraft with Artec Leo
This is why teams from Asobo Studio had to visit various runways to digitize multiple planes, ranging from aerobatic two-seaters all the way up to jumbo jets, with every aircraft scanned meticulously.
Those scanning operations took only a few weeks, and were accomplished with the help of the handheld 3D scanner Artec Leo, a device capable of scanning 80 frames per second, and operated via a simple touchscreen. The scanner was provided by 3D Numérisation, an Artec 3D partner.
This way, Artec Leo was used to rapidly capture the colors, shapes, and precise dimensions of a Robin DR 400 aircraft, as well as many other planes.
Once the planes are scanned, the data is then processed in Artec Studio software, where the scan mesh densities are reduced and optimized to match the game engine requirements before the scans are exported for further development. Artec Studio allows the user to create, edit, and process all the 3D data at hand, whatever the size, or resolution of the object being captured. Each scanned aircraft needs around one working day of software processing in order to be ready for export.
Ease of use, ultra-realism, and time saving
Artec Leo, which is capable of scanning any type of object, was also used to digitize other parts of the aircraft, such as the landing gear and fuselage.
It is obviously much faster to scan an existing object than to recreate it from scratch using 3D modeling software. 3D scanning technologies allow users to digitally bring to life an object identical to its real-world counterpart. To show how fast the process is, scanning a plane took from half a day to one day, depending on its size. Entire cockpits and landing gear could be captured in merely an hour.
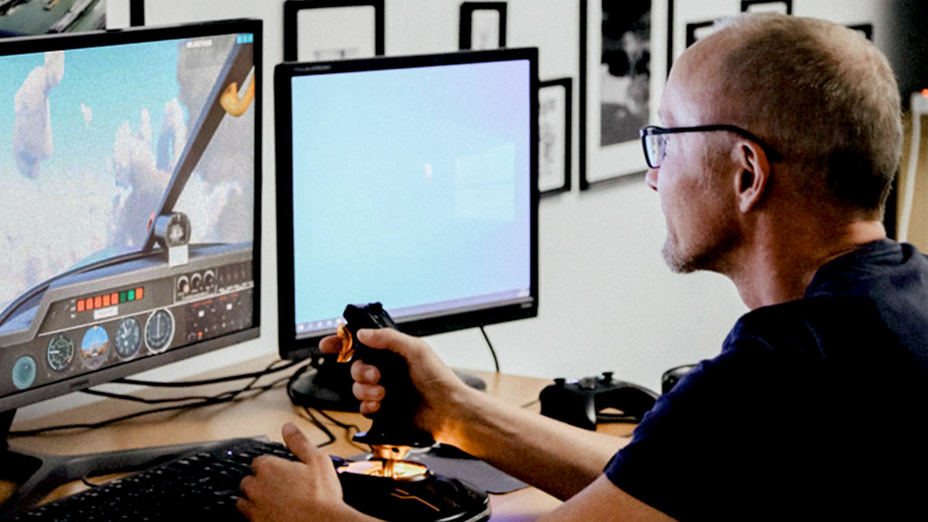
Ultra-realistic aircraft models are tested inside the simulator
“We could capture a huge amount of data in such a short time, while changing the angle of scanning very quickly,” said Nicolas Favre, Vehicle Artist at Asobo Studio. “During the digitization process, the only difficulty was to find enough distance to scan the instrument panel inside the cockpit, which is a narrow cabin. Without 3D scanning, it would have been way longer and more difficult to reproduce such a high level of precision, especially for the many knobs and buttons inside the cockpit.”
“3D scanning was crucial in regards to time savings, and let us skip some quality control checks from different aircraft manufacturers who had to give us their authorization to validate our work. With 3D scan technologies, we could go directly to the modelization phase while earning trust and credibility from the manufacturers, who could verify the accuracy of our aircraft and cockpit models in our game,” explained Gabriel Turot, Vehicle Artist at Asobo Studio.
Asobo Studio, always up-to-date with the latest technologies, considers this 3D scanning project as a “Laboratory for ideas” to eventually use on other future projects, with the objective to create even more realistic video games.
Andrey Vakulenko, Chief Business Development Officer of Artec 3D, concluded “With this approach to simulation game development, anyone can virtually step inside an aircraft cockpit that’s vividly identical to the original. It is simply stunning to experience the results delivered by Asobo Studio for creating the planes in Flight Simulator. The Artec Leo scanner is normally used for the design of actual aircraft, and ensuring quality control of their parts. It is exciting to know that now everyone can enjoy 3D models of these planes with a level of quality chiefly used by aeronautical engineers. This opens the gates for countless developers across the video game industry, but also in virtual reality and augmented reality as well.”
Scanners behind the story
Try out the world's leading handheld 3D scanners.