Ingeniería inversa de un coche de Fórmula 1 e impresión 3D en miniatura
El objetivo: Utilizar dos escáneres 3D diferentes para escanear el automóvil de Fórmula 1 en su totalidad, capturando todo el automóvil de arriba a abajo con los más altos niveles de detalle y velocidad.
Herramientas utilizadas: Artec Eva, Artec Studio
Los escáneres 3D de Artec son herramientas indispensables, utilizadas en todas las etapas del ciclo de vida de un producto. Desde la creación de prototipos hasta la ingeniería inversa, pasando por la creación de un modelo 3D para el análisis de control de calidad y análisis de datos, la digitalización en 3D es vital para lograr un flujo de trabajo más rápido.
La ingeniería inversa consiste en capturar los detalles tecnológicos y la composición de un objeto para aumentarlo, mejorarlo o recrearlo. Utilizado en una gran variedad de industrias, como la ingeniería industrial, automoción, aviación, fabricación, electrónica y muchas otras, permite replicar el objeto inicial mediante la captura, análisis y desmontaje de su réplica digital 3D.
El uso de la digitalización 3D para la ingeniería inversa es cada vez más popular, debido a los resultados precisos que se pueden obtener y a la facilidad de uso. Las soluciones 3D de Artec proporcionan una precisión impresionante, así como la capacidad de capturar en 3D objetos rápidamente, mientras que el software inteligente de post-procesamiento, Artec Studio 11, es capaz de procesar grandes cantidades de datos automáticamente para crear el modelo 3D. Además, debido a la gran movilidad de los dispositivos, son capaces de llegar a los lugares de difícil acceso del objeto, y cuando se combinan con el pack de baterías, no requieren una fuente de alimentación fija.
Un buen ejemplo del uso de la tecnología 3D para la ingeniería inversa es este proyecto iniciado por un fabricante de herramientas con sede en Birmingham que encargó a los socios británicos de Artec, Central Scanning y a un proveedor líder de soluciones CAD & CAM, Delcam, la realización de una réplica en 3D a escala de su coche de F1 para que pudiera ser impreso en 3D a un tamaño de aproximadamente 300 mm.
El coche fue escaneado en 3D, y luego los datos recogidos fueron procesados en el conjunto de software de ingeniería inversa PowerSHAPE de Delcam.
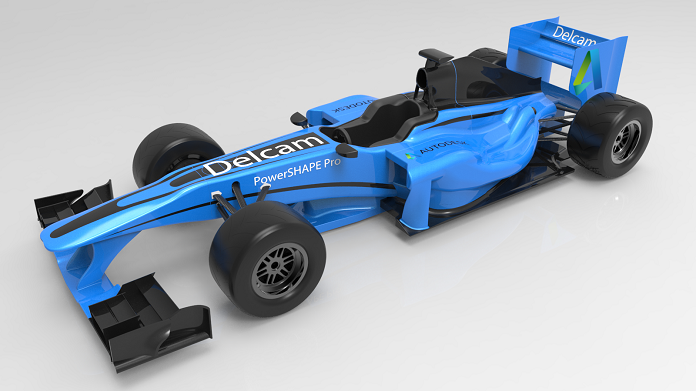
El modelo acabado del coche de F1 en PowerSHAPE.
"Hicimos este escaneo como prueba para ver lo que se podía lograr usando dos tipos de sistemas de escaneo", dice Paul Smith de Central Scanning.
La carrocería principal del coche fue capturada usando un Steinbichler Comet L3D. La cabina del conductor, el volante, la suspensión de la horquilla, el alerón trasero, los espejos retrovisores y las áreas a las que no se podía acceder fácilmente con Steinbichler Comet fueron escaneadas en 3D con Artec Eva.
"Elegimos Eva por su versatilidad y velocidad, además no necesitamos añadir marcadores, ya que sigue fácilmente los dibujos", dice Paul.
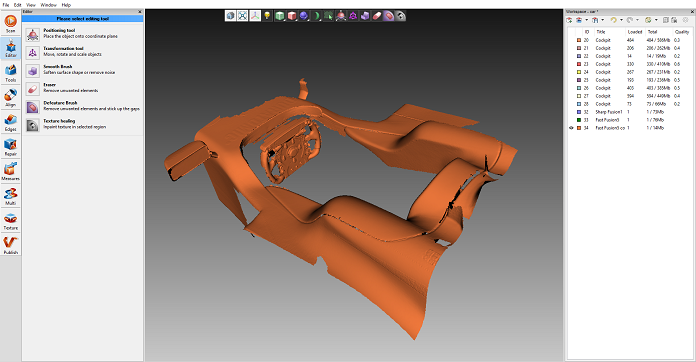
Parte de la cabina en Artec Studio 10.
El coche fue escaneado en 3D en el área de recepción del propietario y en el taller; ambas áreas tenían buena iluminación estable pero sin luz solar directa ya que esto podía afectar a la captura de datos.
Paul ha compartido con nosotros algunos consejos sobre cómo escanear las piezas del coche más fácilmente.
"Agregar algo detrás de las suspensiones de doble horquilla, como papel pintado, permite que el escáner rastree la textura y capture la delgada geometría ".
Había algunas zonas oscuras de fibra de carbono alrededor de los trapecios, que se rociaron con spray muy ligeramente. Los reflejos de luz alrededor de las áreas del alerón también se pintaron un poco para facilitar y acelerar la captura.
"Nos gustó usar Artec Eva porque no necesitaba calibración y era rápido de instalar y capturar en estas áreas difíciles", dice Paul.
La mayoría de los datos se procesaron utilizando configuraciones estándar y sin textura durante el proceso de reconocimiento global para acelerar el proceso. Los grandes conjuntos de datos de Artec y Steinbichler se fusionaron en PolyWorks.
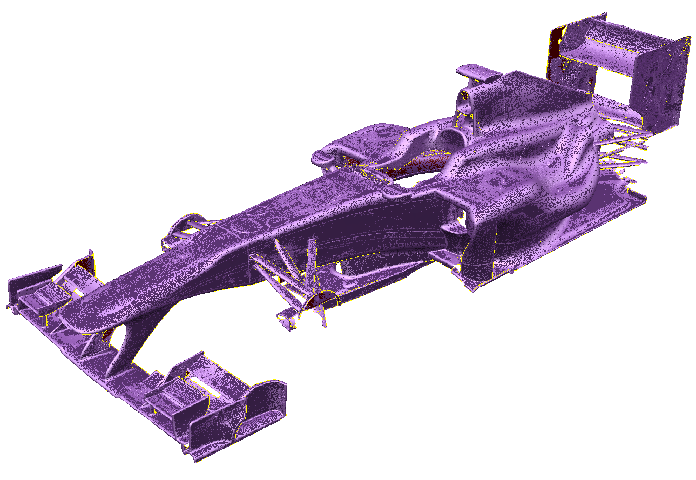
La malla creada a partir de los datos 3D.
El modelo completo de 250Mb STL 3D,con aproximadamente 8.5 millones de triángulos, fue entonces completamente rediseñado en Delcam usando PowerSHAPE Pro. Las regiones complejas de doble curvatura eran las más adecuadas para el modelado de superficies, mientras que las partes más prismáticas podían formarse de forma más eficiente utilizando sólidos.
Como explica James Slater de Delcam, "Las aletas delantera y trasera del coche fueron modeladas como sólidos, creados tomando secciones a través de la malla, extruyéndolas y luego fusionando las piezas separadas usando operaciones booleanas simples". Este trabajo fue realizado por un estudiante en prácticas de verano, que sólo había tenido una semana de formación antes de embarcarse en el proyecto. Mientras tanto, uno de nuestros ingenieros más experimentados se ocupaba de la construcción de la superficie más exigente necesaria para la carrocería. El resultado final fue un modelo 3D completamente detallado, híbrido, de superficie y sólido que sería virtualmente imposible de realizar utilizando cualquier otro software. Por supuesto, una de las cosas más importantes en cualquier proyecto de energía renovable es arrancar con una malla precisa y de alta calidad ".
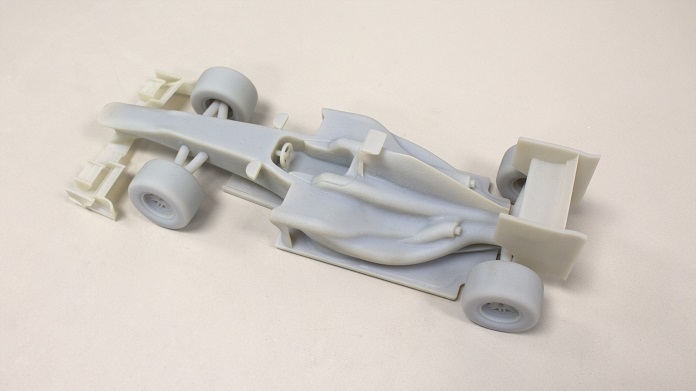
La réplica impresa en 3D del coche de F1.
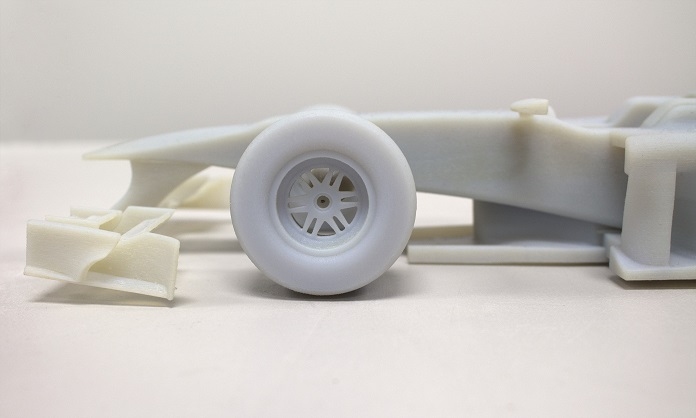
Primer plano de la maqueta del coche de F1.
El coche fue revestido a tamaño completo. Una vez que se redujo la escala, algunas de las áreas más delgadas, en particular los trapecios y los alerones, se engrosaron en PowerSHAPE. La copia digital del coche se imprimió en 3D en Objet Eden 500V con una capa de impresión de 0,016 mm.
Escáneres detrás de la historia
Prueba los escáneres 3D líderes en el mundo.