Artec Space Spider e Control X permettono una produzione più rapida e accurata
Riepilogo: La fabbricazione in più passaggi può far sorgere durante il processo delle imprecisioni che finiscono per causare malformazioni nelle parti prodotte. Le indagini correttive sono difficili, a meno che non si utilizzi un approccio sistematico con gli strumenti adeguati.
Obiettivo : Utilizzare lo scanner 3D Artec Space Spider e il software di metrologia e gestione della qualità Geomagic Control X di 3D Systems per ridurre i costi e i tempi totali del progetto, aumentare la precisione e superare le aspettative della fonderia con il minimo numero di iterazioni.
Strumenti utilizzati: Artec Space Spider, Artec Studio, Geomagic Control X
La scansione e l'ispezione di parti prodotte con la stampa 3D si è tradotta in costi ridotti, iterazioni ridotte al minimo e precisione e qualità migliorate.
Man mano che le tecnologie di produzione evolvono produrre le migliori componenti meccaniche possibili pone sempre più nuove sfide tecniche. Spesso, la prima volta che un produttore a contratto inizia la produzione, sono necessarie diverse messe a punto del nuovo processo per comprendere elementi come il restringimento, le rifiniture di superficie e la ripetibilità. La produzione additiva non fa eccezione, ma gli strumenti per rintracciare gli elementi di errore in questo campo non erano al passo con i tempi. Almeno fino a oggi.
La maggior parte dei ben prodotti seguono un serie di tappe comuni. Progettazione, produzione, ispezione sono un modo generalizzato per prendere in considerazione il processo, le fasi e le responsabilità. Ognuna di esse è una chiave per la produzione di parti di alta qualità. A seconda della complessità e della natura del pezzo da produrre, il flusso di lavoro può essere ottimizzato a più riprese.
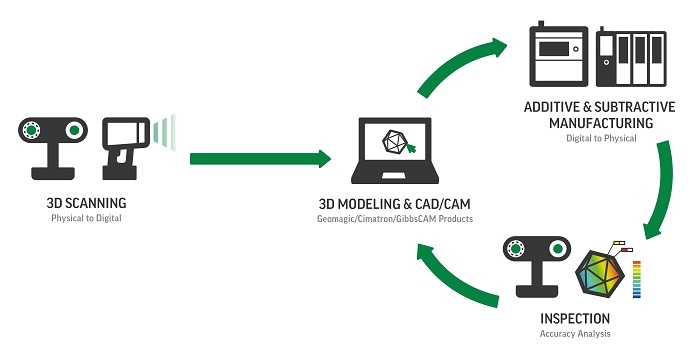
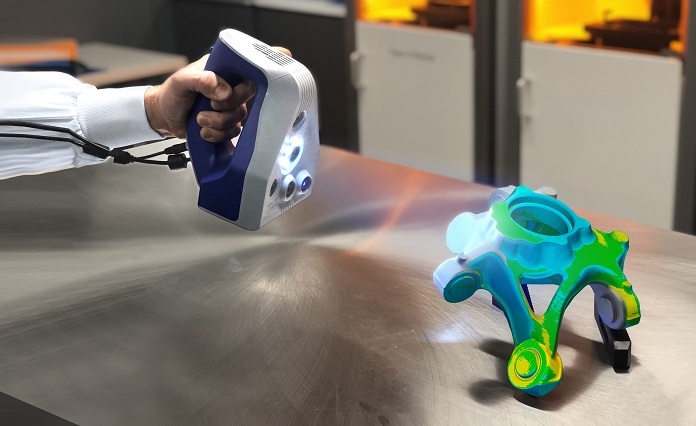
Nel flusso di lavoro descritto di seguito, dimostreremo come Artec Space Spider e il software Geomagic hanno eseguito una perfetta cattura e analisi della forma di stampi di fusione in cera stampati in 3D e pezzi pressofusi, in tutte le fasi di progettazione, test e processo di produzione.
LA SFIDA
La fabbricazione in più passaggi può far sorgere durante il processo dei contrattempi che finiscono per causare imprecisioni nelle parti prodotte. Le indagini correttive sono difficili, a meno che non si utilizzi un approccio sistematico con gli strumenti adeguati.
LA SOLUZIONE
Lo Scanner 3D Space Spider e il software di metrologia e gestione della qualità Geomagic® Control X ™ di 3D Systems
I RISULTATI
• Il raffinamento del processo produzione additiva senza attrezzi, con scansione 3D e reti di ispezione, ha migliorato i risultati sul numero minimo di iterazioni (una)
• riduzione del 27% dei costi con un aumento del 10% della precisione totale
• Stretto rapporto di lavoro con una fonderia e analisi del processo di fusione di parti finite che ha superato le aspettative della fonderia con iterazioni minime (una)
• Incremento del 14% della precisione delle parti finali
• Riduzione del costo di rifinitura con operazioni di lavorazione secondaria ridotte

Artec Space Spider è uno scanner 3D portatile ad altissima risoluzione che eccelle nel catturare con precisione piccoli oggetti e dettagli complessi per l'ispezione dimensionale.
Con il suo funzionamento plug and play, Space Spider esegue la scansione degli oggetti facilmente, senza complicate preparazioni e una formazione dell'utente necessarie, consentendo ai clienti di digitalizzare le parti ovunque si trovino. Gli algoritmi proprietari "target free" di Artec 3D consentono allo scanner di tracciare l'oggetto basandosi solo sulla forma e sul colore. Non è necessario aggiungere marcatori sull'oggetto
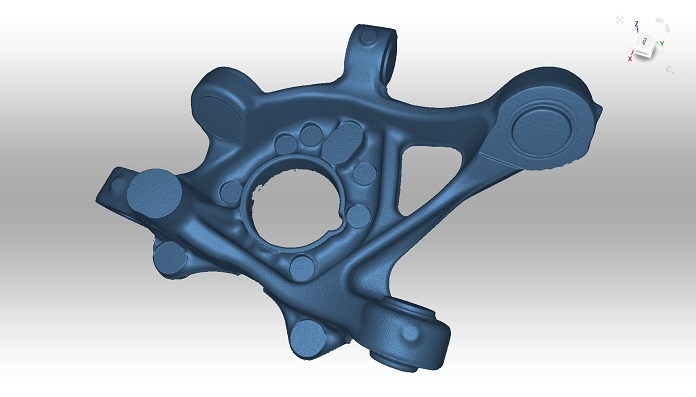
Software di scansione Artec Studio
Geomagic Control X di 3D Systems è un software di metrologia industriale che consente l'analisi delle cause e la correzione della produzione. Il software nativo di scansione 3D Control X è una soluzione ideale per la metrologia con dispositivi di misurazione portatili. Con Control X, sempre più persone nella vostra organizzazione potranno prendere misure più velocemente, con maggiore frequenza, in modo più completo e ovunque.
Questa soluzione completa fornisce informazioni preziose sulla produzione nei processi di manifattura più complessi. Il risultato? Una qualità finale dei pezzi notevolmente migliorata, precisione e ripetibilità.
Design
In questo esempio di flusso di lavoro, abbiamo replicato un vero e proprio progetto del cliente. In questo caso il nostro cliente stava sviluppando un veicolo leggero autoguidato.Al fine di accelerarne l'immissione sul mercato, sono stati selezionati e combinati una serie di componenti e sistemi di veicoli sul mercato per assemblare un prototipo funzionante . Durante questo processo è stato trovato uno snodo di sterzo che si è dimostrato prezioso per il progetto, e il cliente aveva bisogno di digitalizzarne e catturarne il design per modificarlo e poi produrlo con un materiale leggero.
Per iniziare il lavoro, il pezzo originale è stato digitalizzato e scansionato in 3D. Per la digitalizzazione rapida è stato utilizzato Artec Space Spider , e il pezzo è stato modellato in modo rapido e preciso in Geomagic Design X utilizzando un approccio di modellazione ibrida unico nel suo genere.In genere i nostri clienti seguono un metodo di modellazione di tipo costruito (molto preciso) o con intento progettuale (guidato dalla dimensione). Un approccio di modellazione ibrido consiste nel combinare entrambi questi concetti per fornire un modello solido CAD che ha sia caratteristiche dimensionate che superfici NURBs altamente dettagliate.Utilizzando questa strategia , il modello è stato completato in meno di 1,5 ore e trasferito in tempo reale su SOLIDWORKS come file CAD basato su feature.

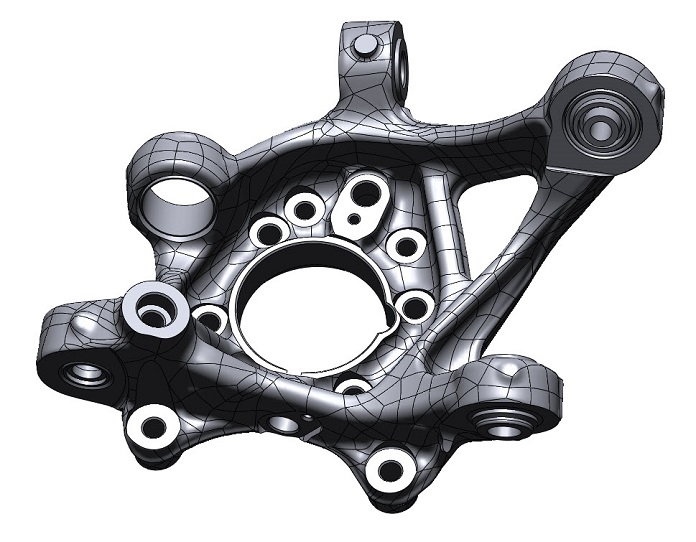
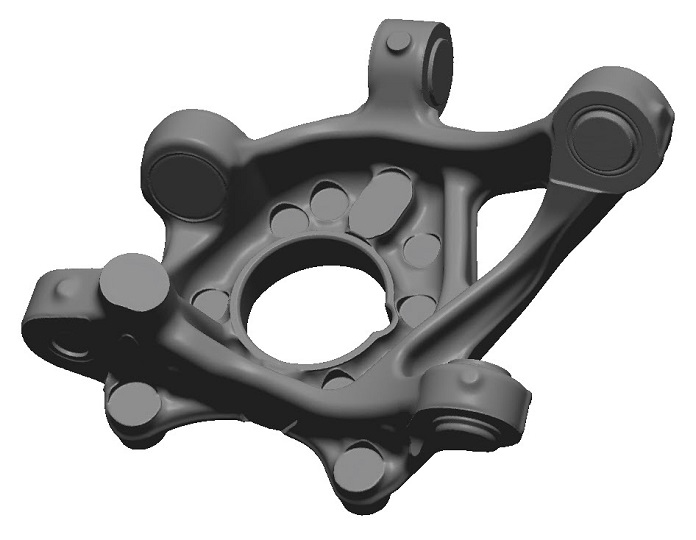
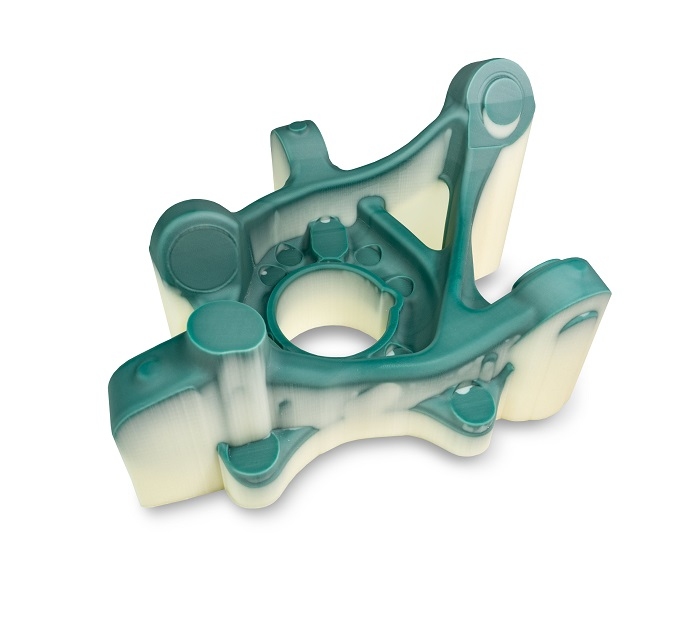
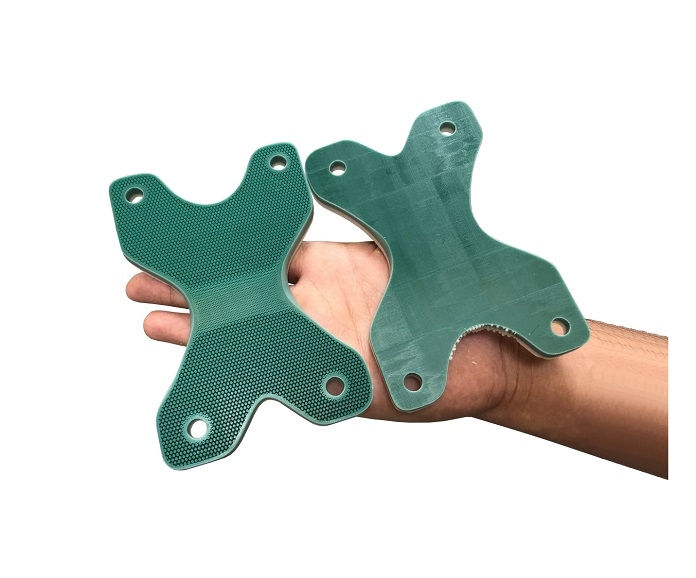
Scansione del pezzo originale
Modello CAD ibrido
Modello defeatured per la stampa
Stampa 2500 IC incompleta
Esempio di sezione trasversale di Sparse Infill Mode su Projet 2500 IC
Creazione di stampi
La produzione additiva è stata utilizzata per applicazioni aerospaziali e automobilistiche per produrre stampi di fusione per decenni.Con i recenti progressi nella stampa 3D, gli stampi industriali possono essere creati in cera o polimero a costi significativamente inferiori, che si integrano perfettamente nei processi di microfusione. 3D Systems sta assistendo ad un uso sempre più diffuso della creazione additiva di stampi tool-less, che continuerà a crescere man mano che la tecnologia diventerà più accessibile, rapida e precisa.
In qualsiasi processo additivo in cui si manifesta un aumento di calore nella deposizione del materiale, o nella post elaborazione, è a volte possibile che il pezzo si deformi. Le parti che hanno una massa significativa o una considerevole area di sezione trasversale, tratterranno il calore più a lungo rispetto alle parti più piccole o più sottili.
In base a questo principio, abbiamo testato due metodi di stampa con l'obiettivo di avere il minor costo possibile e il più alto livello di stabilità dimensionale.Abbiamo testato un metodo di stampa a cera completamente solida e un metodo di riempimento a guscio sottile/cera sparsa, preparato dal software 3D Sprint build e stampato sul sistema Projet MJP 2500 IC, che produce modelli di colata in cera. Da esperienza precedente, abbiamo scoperto che un guscio da 2 mm con un rapporto di riempimento del 50% produce parti stabili di alta qualità nella stampa di parti relativamente grandi.
Dopo la post-elaborazione e il raffreddamento, i nostri due modelli sono stati scansionati con Artec Space Spider con relativa facilità. La forma unica delle parti, il colore verde della cera e il leggero effetto opacizzante e sbiancante del post processing hanno permesso al nostro tecnico di scansione di catturare senza problemi i modelli utilizzando il tracciamento Geometry + Texture.
Usando Geomagic Control X, abbiamo importato direttamente il nostro file 3D Sprint Build e ispezionato ogni parte nel suo esatto orientamento di stampa per la routine di ispezione. Sapendo che avremmo scansionato il pezzo sotto esame in più iterazioni per migliorare il nostro processo, siamo stati in grado di impostare un progetto di ispezione dettagliato e duplicarlo più volte mantenendo l'intera cronologia di sviluppo del processo in un unico file Geomagic Control X. Una volta completate le scansioni, abbiamo semplicemente importato ogni nuovo file stl nel progetto Control X e il processo di valutazione si è svolto automaticamente, creando report ripetibili di alta qualità.
Abbiamo scoperto che generalmente tutte le aree con offset di lavorazione a macchina erano entro i limiti di errore, ma le aree più libere presentavano tendenze al di fuori della fascia di tolleranza più stretta. Riteniamo che questo sia correlato ai nostri presupposti secondo cui ampie aree di sezione trattengono il calore e cambiano potenzialmente forma durante il raffreddamento.
La nostra analisi completa di questa fase ha aiutato a trarre alcune conclusioni: la stampa 3D con lo stampo in cera non era solo più economica, ma anche di dimensioni più fedeli dopo la post-elaborazione.
Stampaggio
La fusione con stampi è un'affidabile metodologia produttiva risalente a 5.000 anni fa e che si è consolidata nella produzione industriale globale negli ultimi cento anni, sin dagli albori della rivoluzione industriale.
Oggi, il processo di fusione offre risultati garantiti, è molto diffuso e supportato da software di simulazione che aiutano a ridurre la possibilità di difetti delle parti interne. Appoggiandosi ai servizi di una fonderia esperta e con uno sforzo minimo da parte del cliente, è possibile fornire stampi fabbricati in modo additivo e produrre parti prive di difetti interni e che superano le aspettative di tolleranza del processo comunemente utilizzate per la microfusione.
I clienti che partecipano attivamente ai test del risultato e all'iterazione del processo possono aspettarsi di ottenere risultati di qualità significativamente più elevata durante l'ottimizzazione della geometria del pezzo prodotto, grazie alla stabilità del processo di microfusione stesso.
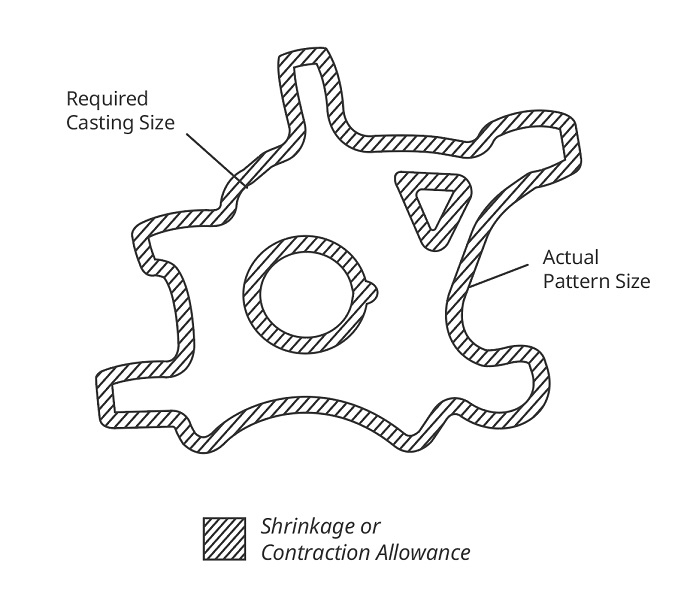
Dimensioni di fusione richiesta
Dimensioni effettive del modello
• ~ 35% in meno di materiale usato nel processo.
• ~ 27% di riduzione dei costi dei materiali.
• ~ aumento del 10% complessivo rispetto tolleranze (utilizzando confronto 3D).
• La parte solida non ha superato la nostra soglia di tolleranza.
• La parte di riempimento ha superato la nostra soglia di tolleranza.
• Inoltre, ulteriori indagini hanno dimostrato che a lungo termine la stabilità dimensionale a temperatura ambiente è stata migliorata nel corso della parte solida.
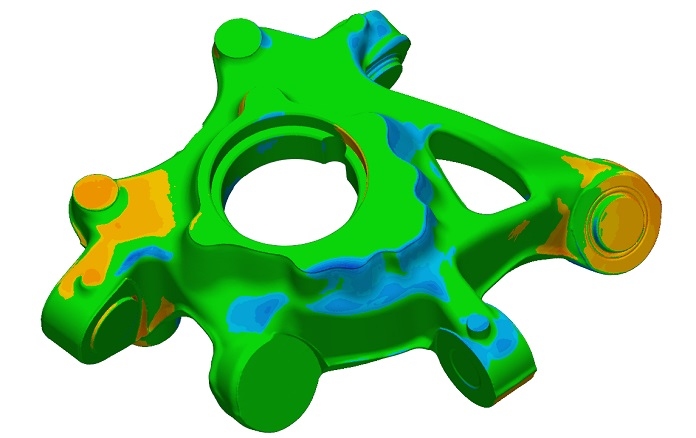
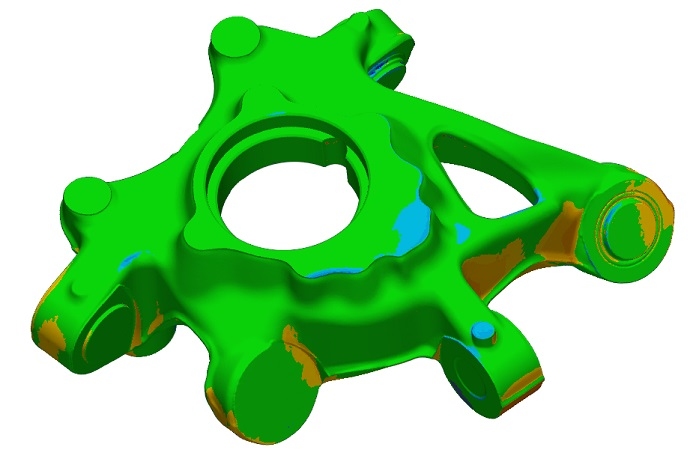
Analisi: Modello solido di cera
Analisi: stampo in cera con Infill
Il restringimento è un risultato comune nel processo di fusione e in genere una fonderia fornisce una guida ai clienti al fine di compensare il restringimento noto di un materiale specifico, per le dimensioni di un pezzo definite da un riquadro di delimitazione. A causa della complessità della geometria e del processo fisico di fusione, è comune vedere un restringimento non uniforme nella maggior parte delle parti prodotte. Di conseguenza, una microfusione può essere generalmente considerata un processo dalla tolleranza fluttuante.
Durante i processi di microfusione del nostro sterzo, abbiamo riscontrato una percentuale di restringimento adatta al nostro modello e materiale. Dopo esserci consultati con l'impianto di colata, ci è stata consigliata una scala uniforme del 2% per la produzione di una parte precisa. Per studiare l'effetto che la scansione 3D e un fattore di scala di precisione possono avere sull'accuratezza della parte finale , abbiamo prodotto un modello di cera con un fattore di scala del 2% come consigliato, e lo abbiamo affidato alla fonderia.
Un'ulteriore ispezione sui pezzi risultanti è stata effettuata per verificare se il fattore di scala uniforme conforme a tolleranze previste. Seguendo le specifiche generalizzate della fonderia, si è ottenuta una parte che era decisamente dentro i parametri di precisione ottenibile dichiarati del nostro partner. Tuttavia, un'attenta ispezione con lo strumento di confronto delle sezioni trasversali in Control X ha indicato alcune aree in cui una migliore applicazione del fattore di scala di precisione potrebbe migliorare significativamente l'accuratezza complessiva del pezzo finito.
Questo confronto di Silhouette di sezione trasversale con una fascia di tolleranza stretta mostra chiaramente i bordi esterni con colorazione blu e i bordi interni mostrano colorazione arancione e rossa. Il profilo esterno conferma una condizione di "sottodimensionamento" in cui il limite effettivo della parte si trova all'interno del limite di riferimento. Il profilo interno mostra che la caratteristica del cilindro centrale è dimensionalmente più piccola del previsto , ma appare al di fuori della caratteristica di riferimento. Ciò indica che l'ombra della sagoma totale della parte presenta una differenza di scala che può essere corretta aumentando nuovamente il fattore di scala, la stampa e la fusione.
Precedenti indagini di miglioramento del processo di microfusione ci hanno fornito alcune informazioni sulle regolazioni relative dai valori standard raccomandati che possiamo applicare e un secondo modello di cera è stato stampato con un fattore di scala non uniforme del 2,2%, 2,3% e 2,7% in X, Y e Z, rispettivamente, e passati alla fonderia.
Con un'ispezione finale sul modello compensato di precisione, siamo stati in grado di trarre alcune conclusioni sul processo da stampo a parte:
• Lo stampo in scala di precisione ha fornito risultati che hanno superato le aspettative della fonderia.
• La conformità dimensionale complessiva della parte corretta della scala è aumentata del 14% circa.
• Almeno una delle principali operazioni di lavorazione potrebbe essere evitata con l'aumento della precisione.
• Il costo totale di produzione della parte è stato ridotto.
• Sono necessarie analisi future per vedere se è possibile applicare ulteriore precisione per ridurre generalmente le operazioni della macchina.
Conclusione
L'efficienza è la chiave per mantenere il profitto e ridurre gli sprechi nei cicli umani e di produzione . Con Artec Space Spider e Geomagic Control X, siamo stati in grado di migliorare la qualità complessiva delle nostre parti prodotte analizzando ogni fase del processo, con il numero minimo di cicli di messa a punto e di iterazione. Ridurre iterazioni e congetture, risparmiare tempo e denaro e accelerare i tempi di immissione sul mercato sono i principali vantaggi dell'utilizzo di una soluzione completa comprendente un software di ispezione industriale, scansione 3D e scansione nativa di alta qualità .
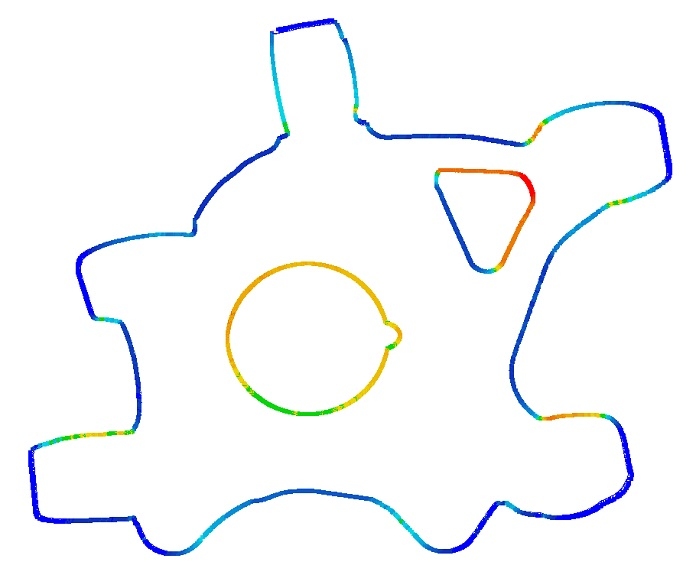

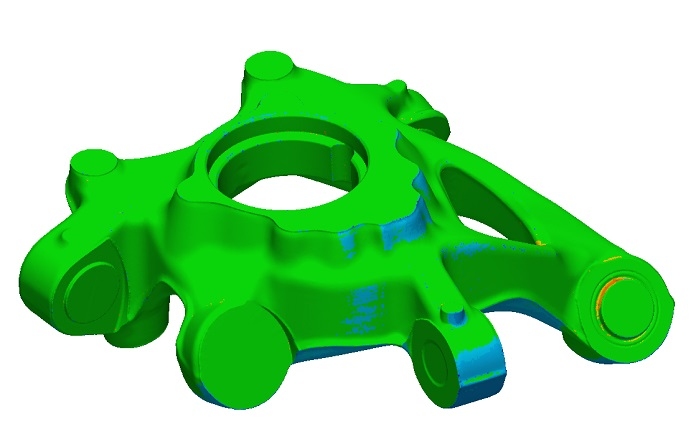
Analisi della sezione trasversale dell'errore di scala
Parte finale stampata
Analisi del casting finale
Gli scanner dietro alla storia
Prova i migliori scanner 3D a livello mondiale.