What is LiDAR?
LiDAR is a mapping technology that uses laser light to measure the distance to a target surface. In a nutshell, it's generating a 3D map of anything from a room to large areas of terrain with stunning accuracy. In this article, we’ll look at what LiDAR solutions are capable of, what different types of LiDAR there are, and how this technology is used.
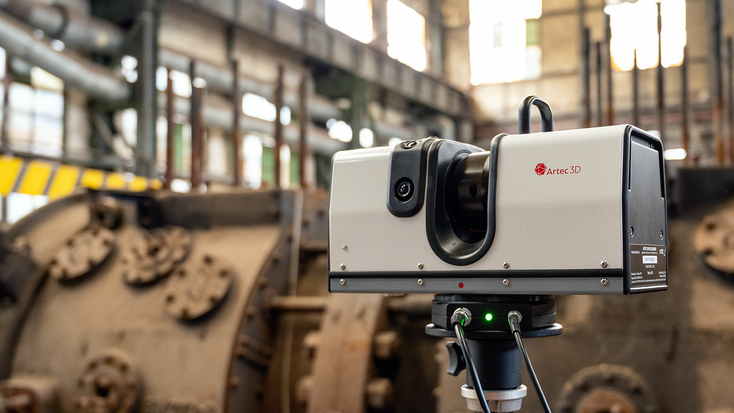
Before we plunge into the mechanics of LiDAR scanning, do you know where the name LiDAR comes from? In the same way radar gets its name from “radio detection and ranging” and sonar from “sound detection and ranging,” LiDAR is an acronym, too.
“Light detection and ranging” or “laser imaging, detection, and ranging” – whichever you prefer, you get LiDAR either way.
What it’s capable of capturing varies: From elevations and pits to vegetation to entire cities, you’ll be able to see it all on your computer screen as a 3D map, zoom in on smaller parts of the scene, or pan across it – all thanks to LiDAR.
To visualize what LiDAR technology is capable of, here’s an example: a 3D map of New York City created from spatial LiDAR data, full-color photos, and satellite shots. This map along with those of many other cities and towns you see all the time can be easily accessed on Google Maps, where you can explore skyscrapers, squares, monuments, and other landmarks in stunning detail and from any side (except for the bottom). You can always go back to a plain 2D view, of course, but why would you after getting this bird’s eye view of a megacity that no 2D map or photo could ever render as vividly?
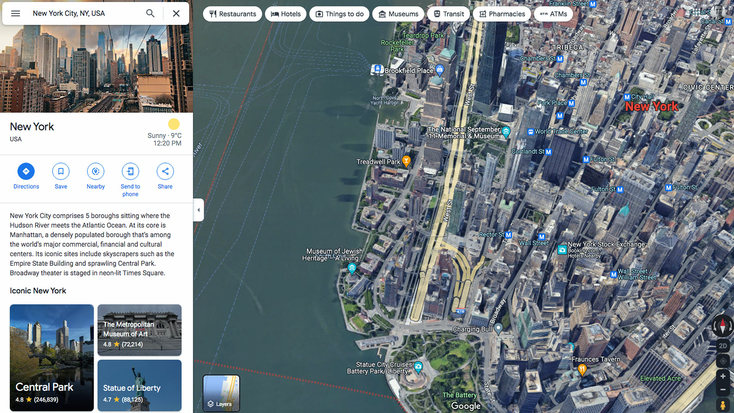
Apart from creating captivating images, why does LiDAR actually matter?
LiDAR technology has opened up tremendous possibilities in engineering, construction, urban planning, and a host of other fields where decision-making depends on accurate information about the shape and dimensions of large and extra-large surface areas. If you’re building a road, say, in a mountainous region, you’ll want to know exactly how much construction material needs to be allocated, and how long construction will take. The length of the road will not be just the shortest distance between points A and B it will connect; to find that out, you’ll need to take into account all rises and falls along the way. Going to take to the forest with a tape measure and a compass? Probably not. The swift and accurate solution to your task would be an airborne LiDAR system.
KEY POINT
LiDAR technology opens up possibilities in engineering, construction, urban planning, and other fields where decision-making depends on accurate information about the shape and dimensions of large and extra-large surface areas.
How does LiDAR work?
A LiDAR sensor scans its surroundings by beaming out laser light. When the light hits the nearest surface, it bounces off and travels back to the LiDAR device, which in turn picks up the inbound signal. Depending on the technology used, LiDAR calculates the distance to the nearest surface by logging the time it took the beam to return or analyzing the phase shift of the inbound signal.
KEY POINT
LiDAR calculates the distance to the nearest surface by logging the time it took the beam to return, or analyzing the phase shift of the inbound signal.
The sensor consists of two key components: a transmitter and a receiver. A transmitter emits up to hundreds of thousands of pulses of laser light in the direction of the surface that is being scanned. Once a pulse reaches the surface, it bounces back, or is backscattered, and the signal is picked up by the receiver. Timing electronics calculate how long the pulse takes to travel from the sensor to the target surface and return, or to be more precise, it calculates the delay in the return.
The longer it is, the further away the surface from the sensor – this technology is called time-of-flight laser scanning. Note that a mobile or airborne LiDAR system also features an IMU (Inertia Measurement Unit that consists of an accelerometer, gyroscope, and other sensors) and GPS tracker to obtain the XYZ coordinates of the transceiver at each point in time a laser pulse is sent out. All this data is analyzed by a computer, the output being a 3D map of the surface in a point cloud data format.
In addition to time-of-flight, there is phase-shift technology. Phase-based scanning utilizes a constant beam of laser energy that is emitted from the scanner. The scanner then measures the phase shift of the returning laser energy to calculate distances.
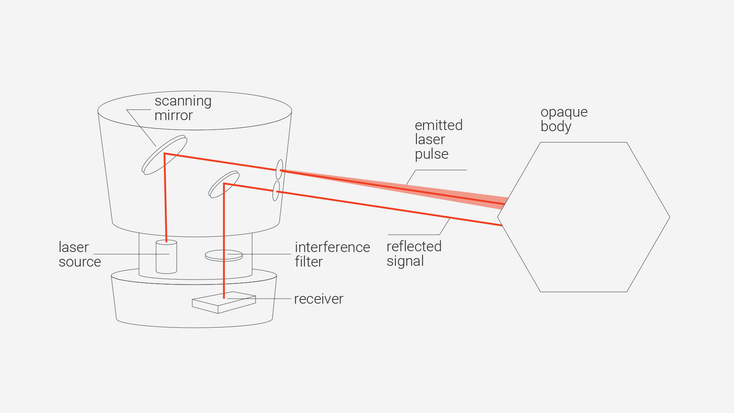
Key terms
Time-of-flight: Using the time it takes a pulse to travel between two points to calculate the distance between the points.
Phase-shift: Calculating the delay that exists between two waveforms emitted at the same frequency or time.
One main tradeoff between time-of-flight scanners and phase-based scanners is between speed of acquisition and dynamic range. Time-of flight devices typically capture data at a rate between hundreds and thousands of points per second. By contrast, phase-based devices capture hundreds of thousands of points per second. Phase-based devices are faster, and in many applications this makes them the tool of choice.
On the other hand, time-of-flight devices have a much longer dynamic range and can provide useful data from as close in as a meter up to a kilometer. Time-of-flight devices are the clear favorite when the ranges to be measured are long.
How accurate are LiDAR scanners?
Depending on the scanner type and ambient conditions, the accuracy of a LiDAR system can range from submillimeter values to dozens and hundreds of millimeters. A number of factors can influence the accuracy of 3D data collected by a LiDAR scanner.
Just like any scanner, a LiDAR is a factory-calibrated device. Before being handed over to a customer, the scanner is ‘trained’ to measure the distance to hundreds of targets with known reflectivity and at a known distance from the device. As a result, an error function is created and stored in the scanner’s software. However, during factory calibration it’s impossible to cover all types of surfaces the scanner may have to scan in specific project environments, and the distance to the surface is sometimes calculated based on the values for similar surfaces with known reflectivity.
Another factor to bear in mind is range noise, which is defined as the difference between each individual measurement and the mean distance to an object. Range noise is impacted primarily by the distance to the object being scanned, as well as the surface’s reflectivity properties.
Mechanical components of a LiDAR scanner are also subject to error, especially with the passage of time, which is why manufacturers recommend recalibrating the scanner once in several years.
Finally, environmental conditions such as wind velocity, solar radiation, air temperature, and moisture can distort the backscattering of laser pulses and affect the quality of the data collected.
Clearly, manufacturers are well aware of factors that impact the accuracy of LiDAR scanners and ensure the best of these devices deliver unmatched levels of accuracy. Read on to get to know Artec Ray, a LiDAR scanner that boasts best-in-class angular accuracy.
Types of LiDAR
We’ve already mentioned two types of LiDAR: mobile and airborne. Add stationary to these two and you get the three main ones.
Stationary LiDAR scanners
Let’s first take a look at stationary LiDAR scanners since that’s the core of the technology; all other types of LiDAR stem from this one. Stationary LiDAR scanners normally cover smaller areas compared to mobile and airborne systems. However, they boast the highest accuracy.
Stationary LiDAR scanners are used extensively for reverse engineering and quality inspection. With a LiDAR, you can scan rooms, buildings, and vehicles of any kind: those that traverse land, air, water, or outer space.
Imagine you need to retrofit a pipework system spanning dozens of square meters, or you’re planning repairs of a building, or considering reverse engineering the body of an airplane. In all these cases, you’ll need exact dimensions of pertinent surface areas, and that’s where a stationary LiDAR scanner will come in handy. It’s especially relevant when, for example, part or all of the surface is located too high above the ground and you can’t possibly reach it with a handheld scanner unless you erect some customized scaffolding.
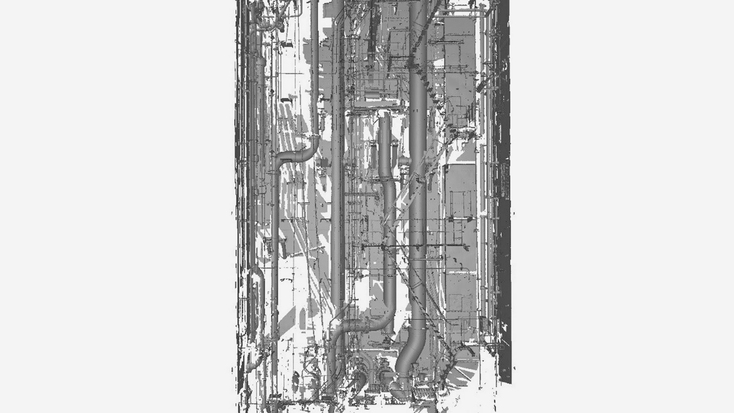
3D scan of pipework made with Artec Ray, a stationary LiDAR 3D scanner.
Now, let’s take a step back and see how you get the results shown in the screenshot above. In other words, how do you scan with a LiDAR scanner? In fact, not much is needed from you. A scanner is mounted on a tripod and placed in front of the object or scene that you’re going to scan. With one click, Artec Ray starts to create a preview of the area to be scanned. If, from this preview, you decide that this is precisely the area that you need captured and that the scanner does not need repositioning, Ray will proceed to fully capture all data from your object or scene.
In cases where you’d want to take care of ensuring faster alignment at the processing stage or increasing the accuracy of your 3D scan data, you may want to put targets across the area. The scanner can easily detect those targets in just about any environment and then, once scanning is over and all data has been collected, the scanner’s software aligns all scans the fastest and most efficient way thanks to the use of targets.
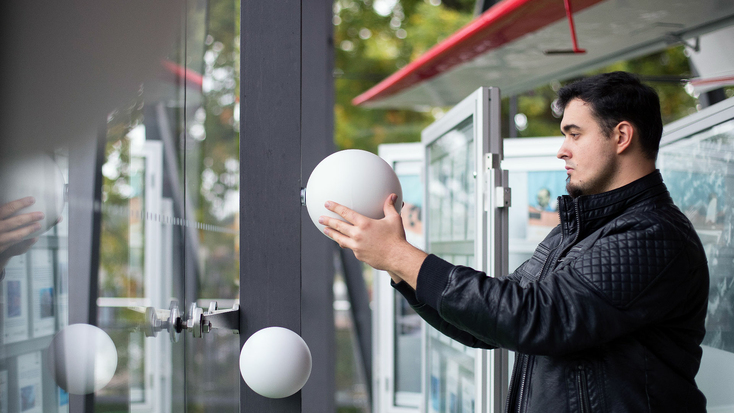
An example of targets placed on an object and around it.
Some LiDAR-type scanners, for example, Artec Ray, do not always require targets to register and align scans, while offering very high accuracy levels. Ray is one of the most advanced metrology-grade devices on the market today. Working at up to 110 m away from the target surface, Ray can scan objects ranging from the body of a car up to large aircraft or buildings. With massive projects like the latter, you definitely wouldn’t want to end up with massive amounts of noise, deal with scan misalignment, or have to take the scanner to the same location on another day and rescan areas that weren’t properly captured from the first go.
With Artec Ray, no worries: this scanner boasts submillimeter distance precision when scanning at up to 10-15 meters away from the object and best-in-class angular accuracy, which ensures you get the most precise results over large surface areas. And by showing you a preview of what it’s going to scan, you can check if the scanner’s current position is best for capturing a given surface area, or if you should consider repositioning the device.

Routine workflow of Artec Ray: gathering 3D data in a maintenance room. The data can be streamed not only to a laptop connected to the scanner but also wirelessly, to an iPad and even an iPhone.
The level of precision of Ray scan data gives you the freedom to reverse engineer industrial objects based on their 3D models; compare 3D models of large mechanical parts with their CAD counterparts for quality control; 3D digitize statues for heritage preservation, and create online galleries for museums around the world – the scope of applications is really wide.
Mapping with airborne LiDAR scanners
The scope of applications grows even further if you go airborne with a LiDAR sensor. That’s what engineers do before they build a new road, lay a pipe through a mountain ridge, or design a new golf course. Mounted on a plane or helicopter, a LiDAR scanner is capable of collecting 3D data across hundreds of square kilometers. Granted, while covering extra-large areas of terrain, airborne LiDAR systems cannot provide submillimeter accuracy. In this case, tolerances can reach a few centimeters, but that’s normally sufficient for most large-scale projects.
Mobile LiDAR applications
The golden mean between accuracy and the size of the scanned area is embodied in the mobile LiDAR sensor, which opens up even more exciting prospects, and not only for engineers. Installed in autonomous, or self-driving cars, LiDAR systems continuously scan the surrounding area calculating in real time the distance to the nearest vehicles, pedestrians, and any sort of obstacles for the purpose of avoiding a collision.
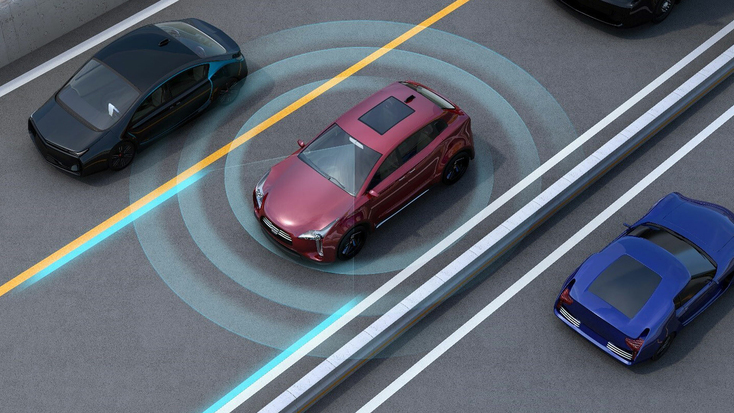
Using remote sensing to ensure a safe drive.
LiDAR scanner in iPad Pro and iPhone Pro
Consumer-level applications of the LiDAR sensor are not limited to autonomous cars. Users of Apple’s iPad Pro and iPhone Pro (starting from version 12) enjoy the benefits of LiDAR technology. Scanning objects up to 5 meters away, these gadgets integrate with apps such as IKEA Place and Hot Lava to furnish users’ rooms in AR and to transform the space around them into game challenges.
While Apple’s LIDAR falls short of the accuracy and resolution needed for manufacturing industries, AR shopping and gaming are largely seen as the most promising applications of this solution. The introduction of LiDAR on the iPad and iPhone has spurred the development of targeted applications, dramatically expanding the number of users of 3D scanning technologies. What used to be the domain of metrology engineers and surveyors is now embraced by regular users of Apple’s gadgets.
Conclusion
So there you have it. When it comes to LiDAR, there’s so much you can do and so many applications you can explore. This technology helps build the cities around us, the detailed images we view, the roads we drive. It’s something to think about the next time you’re wandering through a city – whether digitally, or in real life.
Get to know LiDAR technology and embrace its benefits with Artec Ray.
Lisez ceci ensuite
Plus d'articles du
Centre d'apprentissage
Le scan laser 3D est une technologie innovante qui crée des modèles 3D ultra-détaillés d’objets et d’environnements. Dans cet article, nous expliquons comment il fonctionne, les types de scanners disponibles actuellement sur le marché, les applications pour lesquelles ils peuvent être utilisés et les avantages qu’ils offrent.
Le scan 3D est plus populaire que jamais, et des entreprises du monde entier adoptent cette technologie polyvalente pour maximiser leur productivité, éliminer les dépenses inutiles et créer de nouveaux produits et services attrayants.
En matière d’impression 3D, votre scanner 3D joue un rôle primordial, au même titre que le logiciel utilisé. Voici un guide consacré aux meilleurs scanners 3D, qui vous aidera à trouver la solution idéale et à en tirer le meilleur parti pour produire très rapidement des modèles numériques prêts pour l’impression 3D.