What is a Digital Twin?
With advanced technologies like AI, VR, and 3D scanning increasingly being integrated into manufacturing, the line between the physical and virtual has never been blurrier, leading some to say that we are living through a Fourth Industrial Revolution. At the core of this ‘Industry 4.0’ overhaul is the ‘Digital Twin,’ a virtual copy of a part, asset, system, or process that can be used to track or improve performance. In this article, we explain how these twins are made, where they are being applied, and the opportunities they could unlock.
Introduction
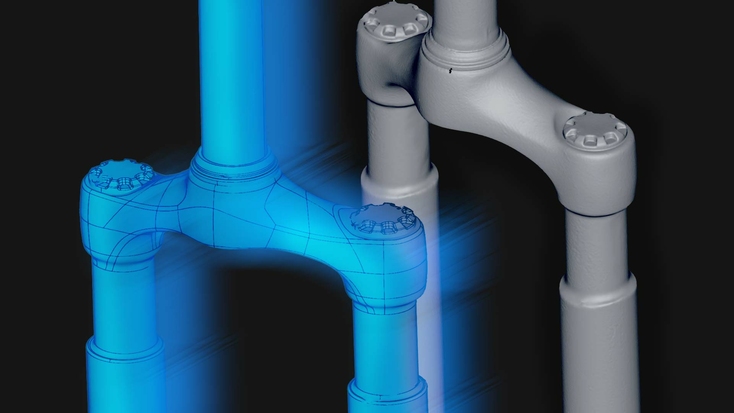
Digital Twins aren’t just 3D models – they’re linked to real parts, assets, systems, or processes by a real-time data feed
Digital Twinning is one of several emerging technologies that have the potential to change the way products are manufactured. But, before we get too carried away with the opportunities they present, it’s worth asking: what exactly are Digital Twins?
Essentially, the Digital Twin concept revolves around the idea that products, machines, and even wider installations, can be turned into virtual models. Whether developed via data aggregation or captured using technologies like 3D scanning, it’s important to note that these twins aren’t just digital copies. In fact, they exchange data with their real-life counterparts via a series of attached sensors. This data stream, which can include information ranging from an object’s condition during production to machinery energy output, is quickly becoming hugely advantageous to manufacturers.
Key point
Digital Twins provide manufacturers with a valuable means of testing specific workflow improvements before rolling them out on the factory floor.
With Digital Twins of systems or processes, they’re able to monitor every aspect of their performance and identify opportunities for optimization. This data can then be utilized in areas like machine upkeep and preventative maintenance to preempt failures and reduce downtime. Digital Twins also provide manufacturers with a valuable means of testing workflow improvements via smaller-scale simulations, before rolling them out on the factory floor.

An Auxiliary Power Unit (APU) Digital Twin. Image source: the University of Twente
Let’s say you also want to assess how an asset composed of multiple moving parts would perform once assembled. With Digital Twin simulations, you could carefully examine how this product’s components interact and identify potential design improvements, in a way that circumvents much of the trial and error seen in product R&D.
At the larger end of the scale, it’s even possible to take the same approach to urban planning. Architects can now use construction data as a solid basis for analyzing if experimental cityscapes, designed to improve construction sustainability and citizens’ quality of life, would perform as expected, if they were to be built in reality.
Key point
Digital twins are not just 3D models of real assets, systems, or processes – they’re connected by a real-time datastream.
While the concept as we know it today was first unveiled by Michael Grieves at the University of Michigan in 2002, Digital Twins weren’t named as such until NASA’s John Vickers coined the term eight years later. Since then, the technology has gone from being a manufacturing niche, to one of the top industrial technology trends globally. In particular, its potential as part of a fully integrated series of technologies, or ‘Internet of Things,’ alongside others like AI, AR, and 3D printing, continues to capture manufacturers’ imagination.
So, how does all this work in the real world? Over the rest of this article, we’ll break down how Digital Twins are made, before identifying how 3D scanning can help optimize this process, and where resulting digital models can be applied across industries.
Types of Digital Twin
Part and Asset Digital Twins
Product twins can broadly be broken down into two different types: parts and assets. By parts, we mean the smallest, most basic functioning components of larger builds, such as the joints and beams of an assembly (also known as mechanical subassemblies). Assets, on the other hand, are products with two or more components, whose interactions can be analyzed in virtual form as Digital Twins.
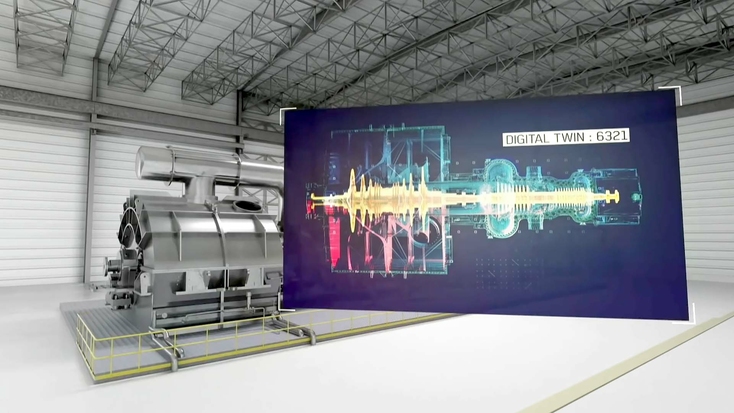
A Digital Twin designed to lengthen the lifecycle of a steam turbine. Image source: GE
System Digital Twins
Zooming out a step further, we have Digital Twins of systems. These models can either be made up of parts or assets that have been assembled into fully functional units, or the machines used to produce them in the first place. Critically, this category of Digital Twin allows users to analyze how two different types of asset interact, and identify opportunities for performance enhancements.
Process Digital Twins
When applied at a wider scale, Digital Twinning can even be used to monitor the performance of entire factories. These Digital Twins allow manufacturers to synchronize all of a facility’s systems, whether these be related to production or facilitators like ventilation systems, and ensure they constantly operate at peak efficiency. They can also be useful planning tools. If, for example, one system were to break down, what would the impact be on others?
Ultimately, taking a macro-level view of process chains enables users to detect things like material shortages and the need for machine maintenance ahead of time, so they can plan in advance, and maximize system uptime.
Where does 3D scanning come in?
So, that’s Digital Twinning in a nutshell. But where exactly does 3D scanning fit in? Well, the technology now represents one of the best ways to create the models behind such twins, as part of a digitization process that’s often described as ‘reality capture.’
While it’s possible to develop computational models that gather the data needed to carry out Digital Twin simulations, without engaging in any reality capture at all, this is a months-long workflow. 3D scanning offers a much faster means of accessing these insights. This can be achieved by digitizing anything from a part right up to a process chain, as it is, either for instant analysis, or utilization as a basis for creating a fully integrated Digital Twin.
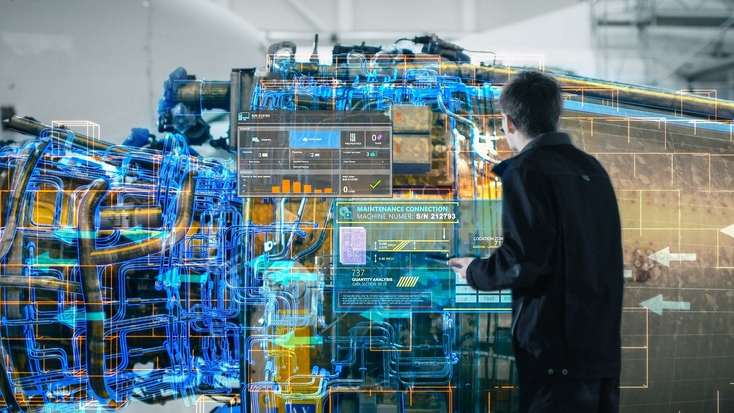
A Digital Twin being used to manage operational and sensory data in real time
Of course, there are also other reality capture technologies out there. Using photogrammetry, for instance, it’s possible to create Digital Twins by overlaying photos of an object taken from multiple angles, by devices as accessible as everyday smartphones. However, the technology is not very accurate, using it can be extremely time-consuming, and it doesn’t tend to provide real-time feedback – making the missing of scan data more likely.
Additionally, while 3D scanning provides linear measurements, photogrammetry is more vulnerable to distortion. This is because the technology relies heavily on image quality, which can be impacted by anything from camera resolution to motion blur. As we’ll explore later on, accuracy is a vital prerequisite for creating usable Digital Twins, and this inconsistency really detracts from photogrammetry’s credentials as a twinning tool.
Key point
3D scanning offers manufacturers a faster, more versatile means of accurately digitizing their products and facilities.
By contrast, LiDAR laser scanning continues to prove a popular and highly accurate means of modeling larger structures in the surveying field. Handheld 3D scanners are also very versatile, and some feature built-in displays that allow you to check what data you’ve captured as you go. So effective are these devices that resulting scans can be used as a basis for CAD or BIM models, and ultimately the creation of Digital Twins.
Overall, advances in 3D scanning continue to make it a more appealing means of gaining manufacturing insights and accelerating the process of creating Digital Twins. But, if you’re new to the technology, what are the key differentiators you need to consider when buying your first device? Let’s take a closer look at some of these factors.
Artec Ray II
If you’re planning on Digital Twinning a large area, whether it be the inside of a factory or real estate to allow for remote viewings, you’ll need to take range into account. Utilizing the tripod-mountable Artec Ray II, you can rapidly capture surfaces from up to 130 meters away, with a 3D point accuracy of 1.9 mm at a distance of 10 meters. This, alongside its built-in display, makes the device ideal for ensuring minimal deviation between scans and the true sizes of factory spaces, and making sure that resulting Digital Twins are fit for purpose.
In order to really recreate facilities in fine detail, it may also be necessary to scan intricate parts with handheld devices, and combine this data with that captured by Artec Ray II – as it’s possible to do within Artec Studio. The platform streamlines the process of aligning point cloud data, whether it has been freshly captured or pre-processed, and running joint global registration, to create 3D models at an incredibly high level of resolution and accuracy.
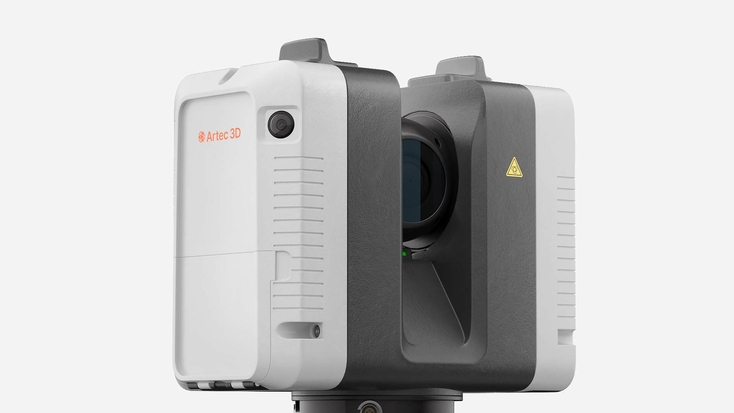
Artec 3D’s lightning-fast long-range Ray II 3D scanner
This industry-agnostic process could mean digitizing anything from a workshop to a warehouse full of machinery, but the benefits are the same. Tracking production performance in real-time allows potential bottlenecks to be identified and tackled as early as possible, whether these are caused by a design defect, or late on by manufacturing faults.
Dynamic duo: Ray II + Leo
Elsewhere, if you intend on twinning assets rather than processes, speed, and maneuverability are likely to be more important differentiators. The wireless, AI-powered Artec Leo ticks both these boxes, enabling users to capture data at speeds of up to 35 million points per second in HD Mode, while monitoring progress on the move, via its 5.5-inch display.
Leo doesn’t sacrifice resolution for speed either, and its HD Mode makes it easier to capture clean, high-resolution scans of small-to-medium-sized objects than ever before. All of these features make the device perfect for creating Digital Twins that replicate product intricacies.
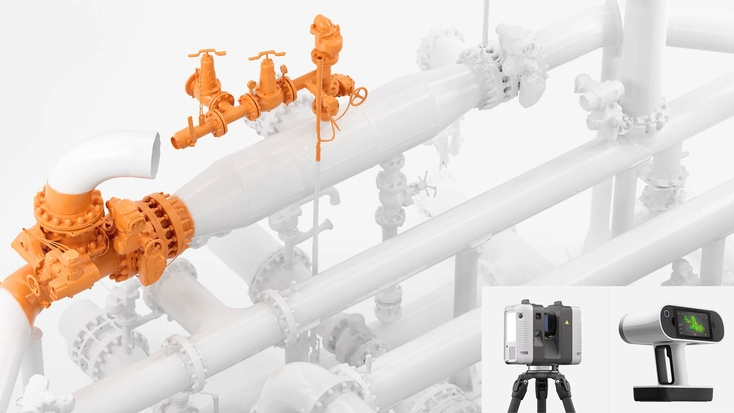
Artec Leo and Ray II being combined to create a detailed Digital Twin of a pipe network
If assets are particularly small, it’s also worth considering digitizing them with Artec Micro. As it’s capable of capturing objects with an accuracy of up to 10 microns, the device can be used to develop models of components like screws and subassembly parts with low deviation, which as we’ll explain next, is vital to them being a reliable basis for Digital Twins.
Dimensional tolerance
In order for Digital Twins to be effective tools for measuring production performance, they first need to be based around accurate data. This is because any mismeasurement will skew resulting workflow analyses. Fortunately, there are now several 3D scanners capable of reaching the accuracy threshold needed to create usable Digital Twin models.
If you’re looking to develop Digital Twins at a small-to-medium scale, structured-light 3D scanning could be perfect for the job. When capturing more intricate parts like industrial fasteners and valves, their efficacy will likely depend on their level of dimensional tolerance – the amount of deviation they can tolerate while still functioning as designed.
The technology is certainly there to achieve this with handheld metrology-grade 3D scanners like Artec Space Spider, capable of creating accurate models of tiny, complex objects, as well as sections of larger ones, which deviate by as little as 0.05 mm from their true size.
Data processing
Another important aspect of Digital Twinning that can be easy to overlook is data processing. Once you’ve finished scanning, the pace and ease with which you can make sense of the resulting data and export it to other platforms will be pivotal to workflow efficacy. In practice, this means being able to transfer files in formats compatible with the programs commonly used during industrial analysis, while retaining vital image data.
Key point
With the right 3D scanning software, you can rapidly capture products, systems, or areas, and export resulting 3D meshes directly into Digital Twin platforms.
When it comes to adopting 3D scanning for the creation of Digital Twins, it’s also worth considering how easy said platforms are to use. These areas are where Artec Studio really comes into its own. Not only does the software process captured data into fully recreated virtual areas or product replicas and allow these to be exported in formats like STEP and IGES, but it streamlines the process of doing so.
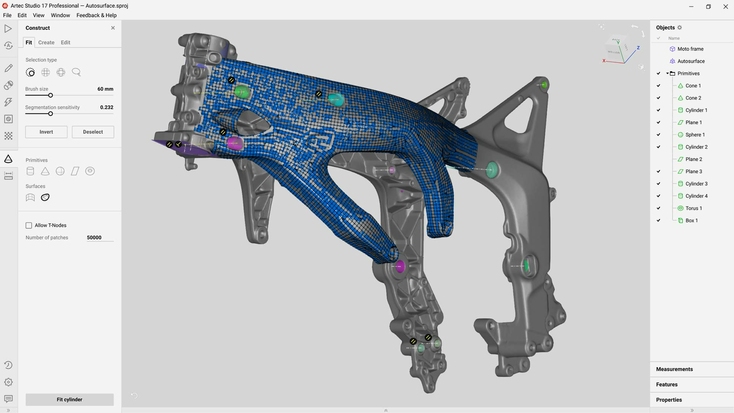
Artec Studio’s Autosurface feature turns organic shapes into CAD models in a single click
With just a few simple questions, Artec Studio’s Autopilot is able to select the right algorithms to deal with a given dataset. This helps new scanning users quickly get to grips with the technology, and automate their scan-to-mesh workflow. On the flip side, those wanting to tinker with the platform’s settings can still do so, as it can handle up to 500 million-polygon datasets, meaning it can deal with scans of almost any object or area.
How to develop a Digital Twin
So, Digital Twins can either be built using vast datasets or based around 3D scans of physical areas or objects. But what do these processes look like in practice? Data-based approaches tend to rely upon algorithms trained using data generated by the asset in question, enterprise resource planning (ERP) systems, and other documents and files, like CAD design sketches. With this data, such Digital Twins can uncover relationships between input and output, and use these findings to predict how future production runs might go.
By comparison, creating Digital Twins via reality capture is more straightforward. Simply set up a tripod scanner such as Ray II to automatically scan the factory floor, or use handheld scanners like Leo, to rapidly capture small-to-medium products from any angle. Doing so makes it easy to turn any object or structure into a digital model – a vital prerequisite to any functional Digital Twin – although if the genuine article is updated, these can need rescanning.
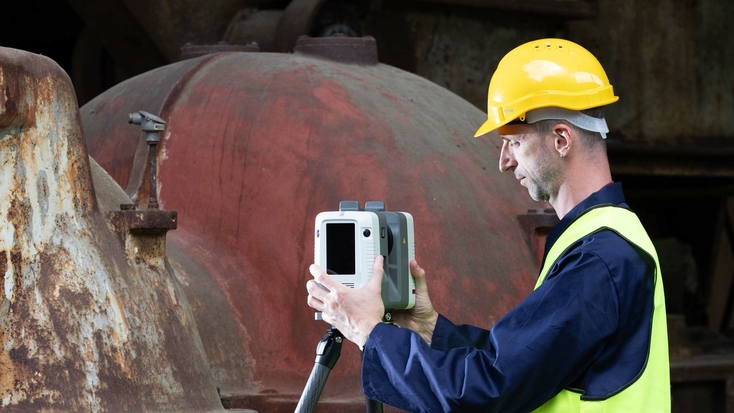
An engineer setting up Artec Ray II to create a Digital Twin of a large outdoor container
In some cases, it’s even possible to combine these two approaches and get the best of both worlds, by developing hybrid twins. Which object digitization method you opt for will largely depend on the application-specific factors listed earlier i.e. the accuracy, speed, and scale you need to capture at. However, once you’ve created a 3D model, this isn’t the end of the process: you still need to attach sensors to real-life counterparts and establish a data link.
Again, where these are attached will depend on your application, as with lifing, anomaly, thermal, and transient models, each requires different data inputs to function. Likewise, to get the most out of these Digital Twins, it’s worth investing in analytics and simulation programs, or considering bringing in data scientists if you intend on building a Digital Twin from data.
How do Digital Twins work?
Digital Twins are not just meant to look like a real product, system, or process, they need to behave like them as well. This requires twins to be linked to the genuine article, so the performance of the latter can be monitored and analyzed in real time.
Established via the attachment of sensors or actuators to performance-critical areas of products, these connections see data shared back and forth between product, twin, and whichever Manufacturing Execution System (MES) is in place. This constant flow of information is hugely beneficial to manufacturers as it allows them to identify process improvements and monitor how systems are operating.
Before products even enter batch manufacturing, users can also deploy this datastream to assess how they might behave during production and perform in end-use scenarios. Doing so allows Digital Twin users to iterate upon designs without having to physically make prototypes, an upside in terms of material saved and getting products to market more quickly.
Digital Twins and the ‘Internet of Things’
Moving on from how Digital Twins work, let’s now take a look at where deploying them can be beneficial. One of their highest-profile use cases revolves around the Internet of Things (IoT) – a broad term used to describe any interconnected set of electronic devices. In manufacturing circles, a trend towards IoT setups has long been forecast, but why are they advantageous?
Well, for one thing, integrating workflows can unlock greater automation, especially when AI is thrown into the mix. This reduces the number of human inputs required to operate them, in a way that improves productivity, while minimizing the risk of errors, which can be so costly to production quality. Drawing on historical data, it’s also possible for IoT setups to drop and raise throughput to meet client demand in a way that better utilizes resources.
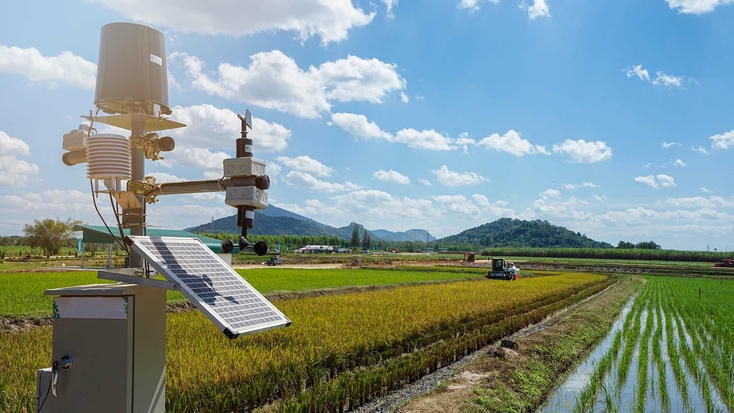
A concept image of AI-powered machinery automating farming as part of a Digital Twin setup
Meanwhile, in the longer term, it’s anticipated that connecting every machine in a given facility to an IoT network will unlock potential business opportunities. As reliance on human operators wanes, the possibility of fully automated ‘lights-out’ facilities grows. Additionally, with more information available on consumer preferences than ever before, IoT workflows provide adopters with a means of quickly capitalizing on emerging trends. All of this means the Digital Twin market is huge.
Key point
With the rise of Digital Twins, 3D scanning, VR, AI, and other advanced technologies, it has become possible to create fully interconnected Internet of Things workflows.
Digital Twin software
So that’s how Digital Twins work in theory, but how are they developed and deployed in practice? Let’s go through some of the leading platforms that continue to help manufacturers turn 3D models into Digital Twins and optimize their respective workflows.
Oracle IoT Asset Monitoring Cloud Service
Renowned software developer Oracle’s Digital Twin-dedicated Asset Monitoring Cloud Service allows users to closely monitor the utilization, location, and overall condition of their assets. All you need to begin using the platform is a dataset or 3D model on which a Digital Twin can be built. This can either be in the form of JSON metadata, or popular modeling files such as OBJ, and those created via widely-used programs like Autocad and Sketchup.
Once Oracle users have uploaded their models, they can utilize the software to inspect, orient and, if desired, divide assets into smaller parts with its Explode feature. It’s then possible to connect nodes to these sub-assets at the click of a button – although in order to gather live data on their performance, sensors have to be placed on relevant areas of the genuine object.
With its program, Oracle says users can create multiple different kinds of model, including Virtual and Predictive Twins, or engage in Twin Projection. Virtual Twins essentially use a semantics-led data model to compare how observed and desired attribute values match up to one another. When used around factory vehicles like forklifts, this can be a useful way of monitoring brake wear, tire wear, or arm length, and ensuring they remain fit for purpose.
Oracle Predictive Twins, on the other hand, rely on machine learning-developed analytical and statistical models, which constantly adapt to changing conditions on the factory floor. This means they can use live data to keep tabs on an asset, system, or process’ performance, and ultimately help identify trends, problems, and solutions, as well as their future maintenance needs. Twin Projection, in turn, allows businesses to build on these findings, introduce a remedial workflow, or if further analysis is needed, export them to other Oracle programs.
Amazon AWS IoT TwinMaker
You may not initially associate Amazon with industrial manufacturing, but the firm’s AWS subsidiary is an established player in the cloud services space. With its IoT TwinMaker platform, AWS claims that users can combine existing 3D models with real-world data to create Digital Twins of everything from industrial equipment to entire production lines.
According to AWS’ 3D model import guide, it’s now easy to convert files like the OBJs commonly exported from 3D scanning platforms, into TwinMaker-compatible GLTFs. Doing so is also said to be beneficial in other ways, such as improving the program’s loading times, and streamlining the way models are updated in its on-screen twin representations, or scenes.
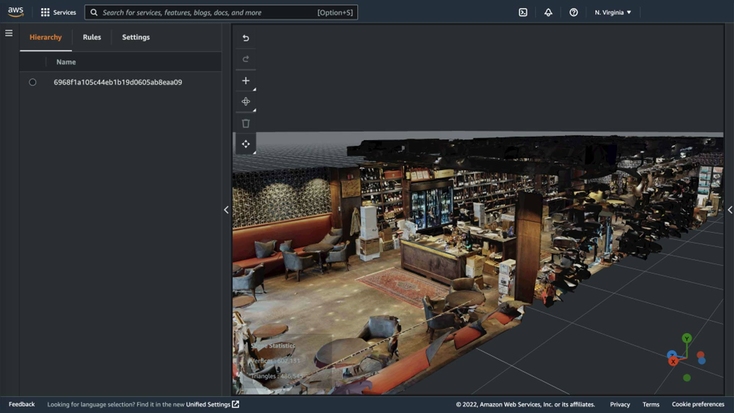
An example of a Process Digital Twin on AWS IoT TwinMaker. Image source: Amazon, AWS
After users have prepared their Digital Twin and connected it to its real-life counterpart, they can deploy AWS’ built-in analysis tools to get a holistic view of their production workflow, or use those of its partners. These include high-profile industrial software developers like Siemens and Ansys. The latter, which markets a Digital Twin Builder of its own, offers a particularly useful suite of software tools that allow users to test full virtual prototypes of asset, system, and process upgrades, without riskily putting them straight into practice.
Autodesk Digital Twin
Autodesk, another of the major players in the 3D software space, also offers a Digital Twin software, only its offering is geared primarily towards the construction sector. Built around the firm’s know-how as a Building Information Modeling (BIM)-compatible program developer, Autodesk Digital Twin enables users to pool design, operational, and construction data. This allows for better-informed decision-making about the way new infrastructure is erected, and on a wider scale, how it can be best integrated into the local area.
This could take the form of measuring and mitigating against risks, or improving ROI by optimizing on capital expenditure, and ensuring facility maintenance is carried out as efficiently as possible. The platform’s integration with Autodesk’s other programs also opens the door to greater file cross-compatibility, and opportunities to accelerate Digital Twinning.

A magnetic flow meter Digital Twin on Autodesk Tandem. Image source: Autodesk
Lastly, continually accumulating and analyzing construction data is bound to help users improve investment decisions, forecast planning needs, and predict failures, as the more data they have, the better informed they’re likely to be. Arguably, this could be said of those using other programs on the market as well, but the nature of building projects – which can be especially prone to overspends – makes these benefits that much more pronounced.
Key point
Many platforms are compatible with popular 3D scanning file types, and it’s only becoming easier to export these and build them up into Digital Twins.
Digital Twin applications
Manufacturing
Of all the areas it’s applied in, Digital Twinning has gained the most traction in manufacturing, where real-time data can be used to uncover shop floor performance gains, ensure product quality via simulations, and schedule predictive maintenance to reduce downtime. Another way the process helps manufacturers manage resources is via virtual warehousing, and 3D scanning offers them a perfect means of digitizing products and spares.
Digital Twins need not only be used as a basis for data gathering, they can also be utilized to create a digital database of spare parts and products. Such databases enable manufacturing on-demand, whether to meet in-house maintenance needs or spikes in client demand. Greater digitization also brings reduced warehousing costs, as manufacturers need to keep less stock on-hand. With this in mind, it can be said that the technology is becoming popular among manufacturers, as it offers them potential short and long-term financial gains.
Automotive
Many of the advantages seen in industrial manufacturing are also present in automotive. For instance, before new electric and autonomous vehicle prototypes enter full production, their designs can now be validated virtually via simulations, in a way that saves on costly trial and error. But that’s not to say the technology doesn’t have industry-specific benefits as well.
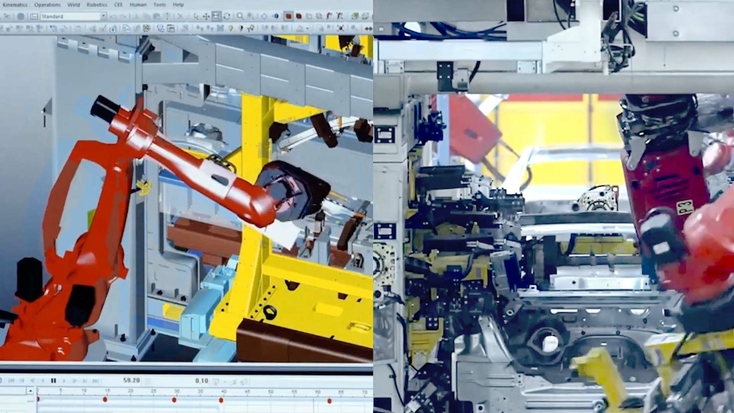
An automotive production line Digital Twin. Image source: Siemens
Most cars are manufactured via a highly complex workflow, in which multiple robotic arms work together to perform tasks such as part assembly, welding, coating, and painting. With Digital Twinning, it’s possible to simulate how these moving parts will come together prior to a process ever being commissioned, in a way that optimizes cycle times and productivity. Such twins also help make manufacturing modular, so automotive firms can change how systems behave, in order to build limited numbers of custom cars, as they’re requested.
Additionally, on the end-performance side of things, Digital Twins allow manufacturers to test how vehicles will fare in real-world conditions. In fact, at automotive giant Renault, its road cars are now subjected to everything from wind tunnel to crash testing, before they ever enter production. This allows the firm to leave nothing to chance and be certain of how they’ll perform in terms of engine output, aerodynamics, gear management, and more.
Aerospace
Unsurprisingly, given that Digital Twins were named by NASA in the first place, the technology continues to find significant aerospace applications, especially in R&D. With flight-ready parts having such fine tolerances, subjecting them to accurate simulations is vital to preventing critical failures and extending the lifespans of aircraft. Digital Twins facilitate this process, by enabling manufacturers to predict when parts will fail, based on historical data.
The same can be said for the space industry, where NASA has long used virtual representations of real components onboard the International Space Station to diagnose and fix failures that occur in orbit. In more recent years, the technology’s satellite-enhancing potential has become a subject of intensive research. With further R&D, it’s thought Digital Twinning could one day enable several constellations to be operated as a single unit. This could allow for the creation of a truly integrated satellite network, with applications in TV and cell signal communications, as well as defense coordination at a military level.
Key point
Digital Twins have their roots in aerospace, an industry where they continue to show promise around satellite integration.
Elsewhere in aerospace, NASA’s hybrid reality training program has already shown how 3D scanning can help prepare astronauts for working on other planets. Using both the Artec Eva and Space Spider, the agency has managed to create Digital Twins of several advanced tools, which are set for deployment on future missions off-world. These devices have been replicated with such realism that cadets can learn how to physically use them in VR.
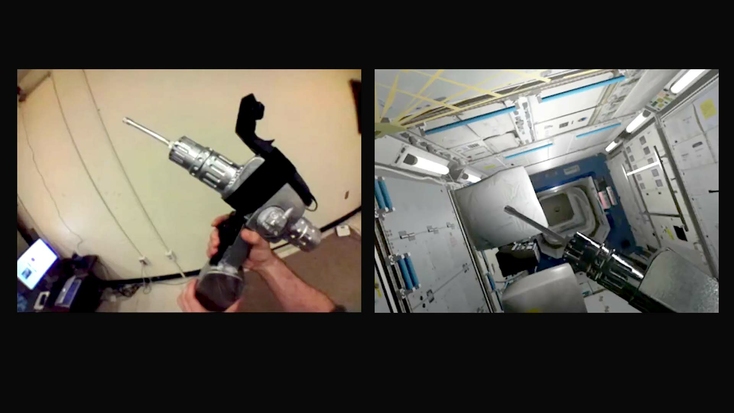
A tool designed for use in space (left) and its Digital Twin in a simulation (right). Image source: NASA
Healthcare
It may not be the first industry that comes to mind when you think of Digital Twins, but the technology is starting to gain traction in the healthcare sector. Here, they tend to be used at more of a process level, rather than for optimizing product performance. With hospitals often under pressure to balance capacity, resources, care models, and patient safety, Digital Twins are a boon for allowing schedules, beds, and operating room usage to be monitored in real time. This, in turn, makes educated decision-making easier for management.
In future, it’s hoped that Digital Twinning can also be adapted to model the human body, so doctors can get a deeper understanding of patients’ individual anatomies. With this insight, it may eventually be possible to develop patient-specific treatments, but there are hurdles still to clear in this pursuit. Attaining the data needed to make these models would require constant physiological testing, the likes of which remain invasive and (for now) unfeasible.
That said, there are already promising signs that 3D scanning can help clinicians better understand the human body. At Montpellier Medical University, for example, students are being trained in VR simulations filled with Digital Twins created using Artec Space Spider. These photorealistic models allow them to practice surgeries without relying on expensive, difficult-to-source cadavers. Arguably, the learnings from such projects are also taking us closer to achieving full-on patient Digital Twins.
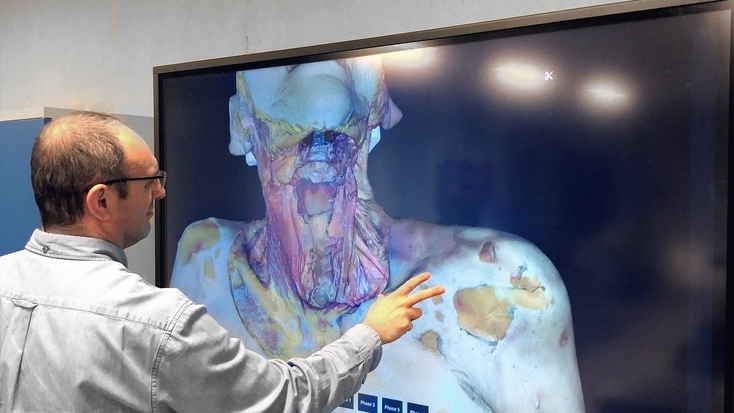
Professor Guillaume Captier interacting with a Digital Twin designed for healthcare training
Construction
Alongside the creation of Digital Twins in manufacturing facilities, laser scanners like Artec Ray II have also become a popular means of modeling in the construction space. With such long-range devices, you can capture and create live models of large building sites, which allow project planners to interact with structures virtually. This streamlines the managing of resources and stakeholder communication while facilitating informed decision-making.
Key point
With laser scanners like Ray II it’s possible to create Digital Twins that unlock unique construction planning insights.
Another aspect of the technology that makes it easy to integrate into construction workflows is the strong compatibility of Digital Twin platforms with CAD and BIM models, the latter of which are particularly popular tools in the sector. As in product manufacturing, you can attach sensors to different areas of these structural models, to plan how heating, ventilation, and air conditioning (HVAC) will be incorporated, and monitor how a build is progressing.
What challenges do Digital Twins face?
While we’ve covered off some of the application-specific challenges facing Digital Twins in the sections above, it’s also worth considering those relevant across the board. The largest roadblock to any Digital Twinning application is inaccuracy, as any significant deviation between model and object will skew your resulting data and analyses.
Using precision-oriented scanners like Space Spider is your best way of ensuring that you capture objects with metrology-grade accuracy, giving your twin the best chance of success. Structured-light and laser 3D scanning also help overcome another key barrier to adopting Digital Twins: cost. Investing in traditional imaging technologies alongside other Digital Twinning infrastructure can cost upwards of $1 million.
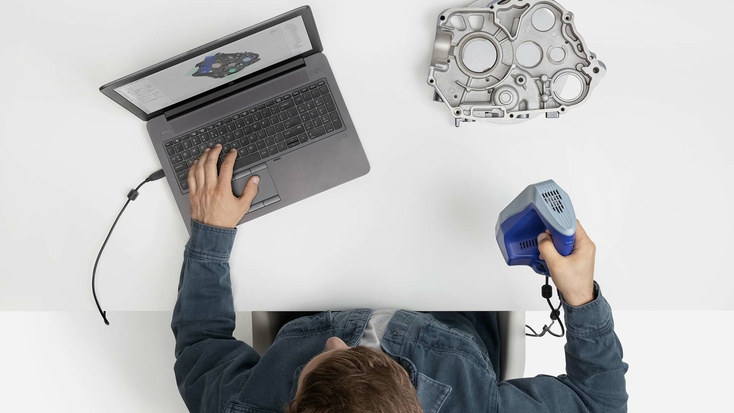
Artec Space Spider creating a Digital Twin of a complex metal component
Handheld scanners like the lightweight, accessible Artec Eva and the groundbreaking Artec Leo, on the other hand, come in well under that price and offer users the chance to upgrade their capabilities as their needs evolve.
Then there’s the lack of data standardization. Of course, you need a fair amount of data to build a Digital Twin, but not all of this is easy to access, and it can come in various different formats. Equally, twins will have different levels of efficacy depending on where they’re applied and factors like how many steps there are between data collection points.
These factors can make accurately weighing up Digital Twin benefits tricky. However, with platforms like Artec Studio, you can at least automate the processing of model data to streamline and accelerate data capture, before exporting models in widely accepted formats.
Key point
Advances in 3D scanning continue to accelerate the Digital Twinning process and drive its adoption in new industries.
The future of Digital Twins
It’s clear that Digital Twin technology still has some barriers to overcome before it can truly disrupt mainstream manufacturing and facility or city planning workflows. However, it has already demonstrated that it can unlock production throughput and repeatability gains, as well as process efficiencies in wider planning applications, and it remains under constant R&D.
Twins are only getting easier to create and becoming more capable, and they may soon be able to proactively source data as part of IoT setups. This progress is happening in tandem with the emergence of more capable, versatile, and accessible 3D scanners, which are helping to broaden adoption across industries. Such technological leaps are seeing more and more multinationals conduct Digital Twin experiments, with telecoms giants like Nokia seeking out new ways to boost coverage and utilize the wealth of data at their disposal.
Outside of industrial applications, the term Digital Twins is also taking on new meanings – and being used not just to describe virtual copies of products, but other objects too. As the Metaverse – a new virtual reality in which people and businesses can coexist – continues to unfold, it’s still unclear what direction it will take. But as it grows, so does demand for digitized versions of real people, places, and items, meaning that it could well be the next new frontier for the growing Digital Twin market.
More from
the Learning center
Starting out in the world of 3D scanning can be intimidating, but everything becomes clear once you take a moment to understand the technology behind it. From your own eyes (the original scanner!) to the latest 3D scanner on the market, here’s how it all works!
There are lots of factors that influence how much it might cost to 3D scan something. In this guide, we cover the main factors that contribute to the cost of 3D scanning, and look at whether it makes sense to get your own scanner, or if you should consider turning to a professional scanning service.
3D scanning is now more popular than ever, and businesses all over the world are embracing this versatile technology to boost productivity, eliminate unnecessary costs, and create new and exciting products and services.