BD Engineering社がArtec Leoでトヨタスープラを ドリフト車個別製作用MOD向けにデジタル化
課題:改造用部品産業市場向けの製品の個別製作を行う際に利用できる3Dモデルを作成するため、トヨタスープラ全体を分解して構成パーツをデジタル化すること。
ソリューション:Artec Leo、Artec Eva、及びArtec Studio
結果:非常に詳細なため、新しいサスペンションのジオメトリ、及びドリフトに利用するために再設計された差動装置と油圧ハンドブレーキの検査のための動的シミュレーション環境へ即座に使用できる、スープラのモデル。
なぜ、Artec 3Dなのか:手作業でパーツ毎に計測を行っていたなら、スープラのリバースエンジニアリングは現実的ではない、時間を要する作業となっていたであろう。 驚くべき速さを持つワイヤレスのArtec Leoにより、BD Engineering社は車両をほんの数時間の間にデジタル化することができた上、成果品としてのデータを利用し、今まで見たこともないドリフト用パーツ設計の基盤をArtec Studio上で簡単に製作することも実現させた。
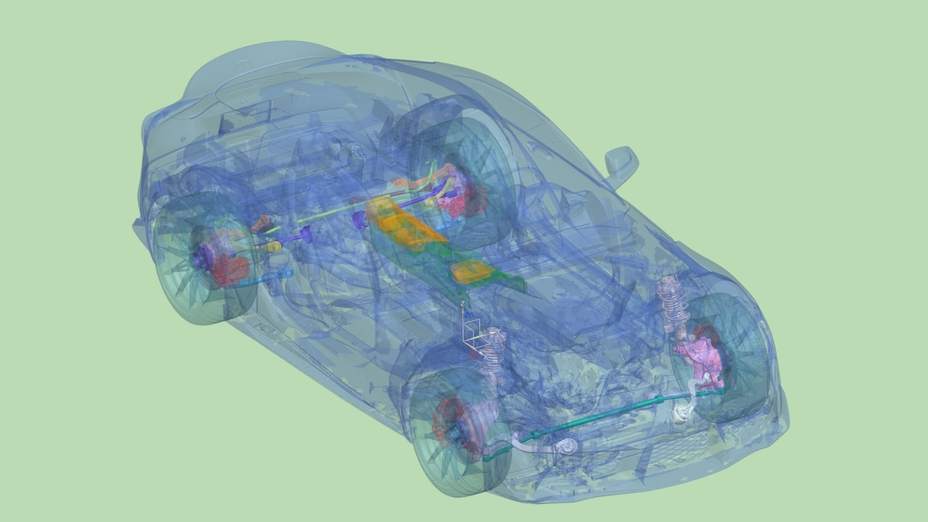
BD Engineering社のリバースエンジニアリング済みのトヨタスープラ、並びに改造計画。 画像は、BD Engineering社のご厚意で掲載
ご自身の望み通りの車両を組み立てることを夢見たことはお有りだろうか。急成長する百六十億ドル規模の米国自動車改造用部品産業市場が示すように、多くの人々がその経験をお持ちのようだが、その実現の難易度は本当のところ、どの程度なのだろうか。
カスタマイズの主な課題の一つは、車両のシャシーや車体との改造部品のシームレスな適合を確実なものとすることだ。委託者ブランド名製造事業者(OEM)は、そのほとんどが自身の貴重な設計データを改造用部品開発企業と共有することに積極的ではないが、このことで重大な問題が生じている。それは、ボンネット内部の部品の把握が車両の改造の際に困難となる点である。
エンジニア(及び自動車愛好家)にとっては幸いなことに、リバースエンジニアリング技術は急速に進歩しており、今ではパーツは数秒の間にデジタル化できる。改造業を営む企業の中には未だ個別製作の為に彫塑や鋳造を用い、ホイールガンに固執しているところもあるが、BD Engineering社はそのような企業ではない。同社は自動車産業やその他の分野で、境界を押し広げ続けている。それを支援しているのが、Artec社の3Dスキャニングである。
BD Engineering社での仕事の納め方
八年前、エンジニアであるアダム・バオ(Adam Bao)は自身の地方大学で車両の改造品の製造を開始した。しかし、情熱を持って始めたプロジェクトは、特殊部品市場協会(Specialty Equipment Market Association, SEMA)や東京オートサロンなどの最先端の自動車トレードショーで展示される個別製作車両を有する盛況企業である、現在のIllumaesthetic社へと急成長した。
同様に、このサクセスストーリーは産業界、医療業界、及び防衛分野の得意先からの受注へと繋がり、バオと共同創立者のニキータ・ラシュマノフ(Nikita Rushmanov)の新たな別の会社の立ち上げのきっかけとなった。それが、BD Engineering社である。同企業は3Dスキャニング、及び高度な製造機器を配備し、迅速なプロトタイプの製造や検査からオンデマンド製造に至るまで、取引先のあらゆる業務を支援している。
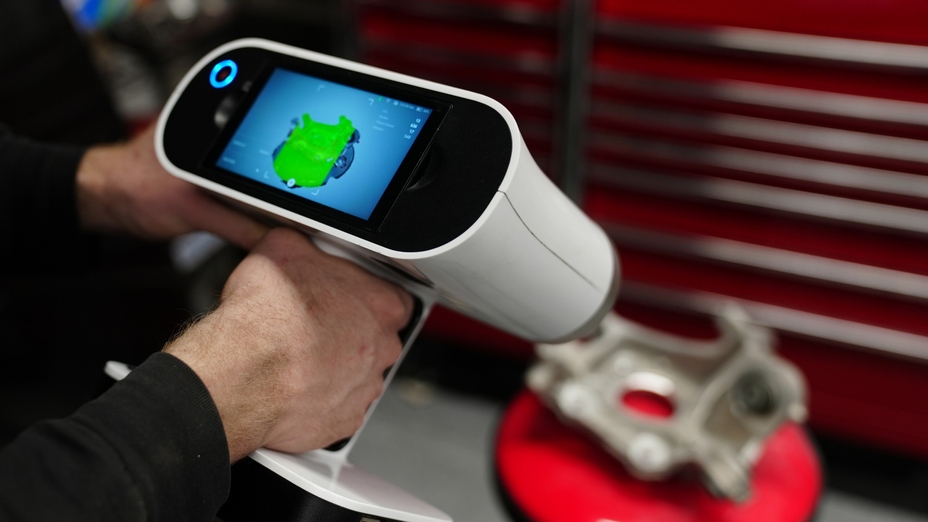
Artec Leo内蔵ディスプレイを利用してのサスペンション部品のデジタル化。画像は、BD Engineering社のご厚意で掲載
しかし、そもそもBD Engineering社はどのような経路を経て3Dスキャニングを採用するようになったのだろうか。当初、バオはスマートフォンによるフォトグラメトリを色々試し、オブジェクトをデジタル化してMODへの使用準備の整った設計ファイルを作成していた。この技術が時間を要する上に十分に正確ではないことに気付いたバオは、迅速で〇.一ミリメートルの精度を持つ3Dスキャナを基にして新たな手法を探し出した。その機器が、Artec Evaであった。
改造用部品産業における需要が増える中、BD Engineering社は後にIndicate Technologies社へ連絡を取った。このArtec社のゴールド認定パートナーは同企業の二か所の拠点を同時に経済的に成長させるため、ワイヤレスでAI駆動型のArtec Leoをアップグレードすることを勧めた。この提案は、その二か所が何百キロも離れているニューアークとロサンゼルスであるという前提があったにもかかわらず、なされたのである。
ラシュマノフは後に州の北部へ移転したが、二人は内蔵ディスプレイを備え、これまでになく簡単に自身の仕事内容を携えて出張することを可能とするLeoの一体型の特性により、カリフォルニアを横断して行ったり来たりしながら同機器を共同で使用できることに第一に気付いた。それ以来、この進取的な二人は自身の更に拡張されたワークフローに3Dスキャニングを統合したが、ただ普通にではなく、かなり独特の形で実現させた。
「自動車産業においては、車両の片側半分のみをスキャンする人々を多く目にする」と、バオは話す。「それはあまり良い考えとは言えない。時計回りにスキャンすると、始まりと終わりが六インチから十二インチ程度ずれる。完全な円形ループを描いて動かないと、エラーが広がってしまうことに繋がる。それで我々は、『もういいや、車両全体をスキャンしよう』という結論に達した。これが本当の『ループを閉じる(=「仕事を仕上げる」の意)』ことだと言える」
「Artec Leoであれば、スキャンの下準備と車両全体のスキャンに要する時間の間に大した差は無いので、我々は『全体をスキャンしよう』と思い付いた」
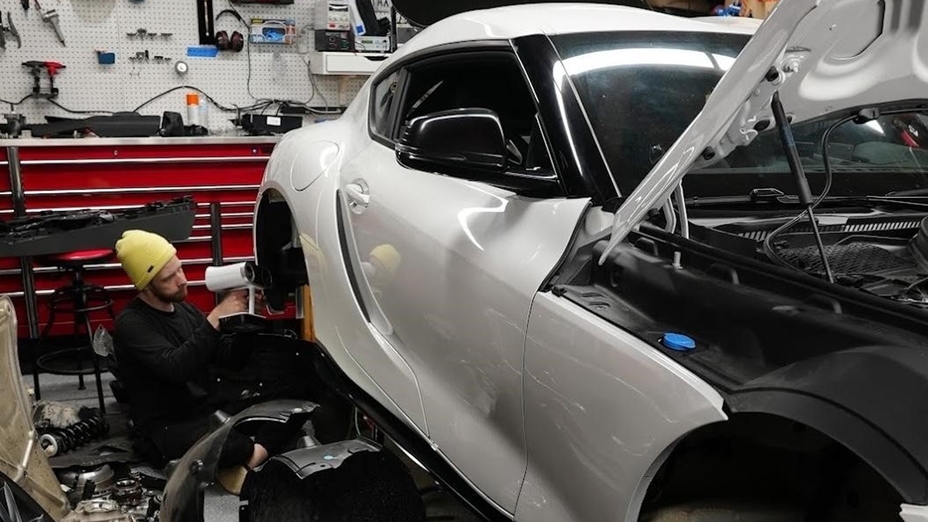
解体されたスープラをArtec Leoによりデジタル化する、BD Engineering社の共同創始者であるニキータ・ラシュマノフ。画像は、BD Engineering社のご厚意で掲載
新たな頂点へのドリフト
ゼネラルモーターズやBMWのような車両の車輪ゲージとテールライトの個別製作を行い、かの有名なスバル社のバンパーの改造にも携わった経験を持ちながら、llumaesthetic社での業務に飽き足らない二人は更なる高い目標を掲げた。それは、車両全体のリバースエンジニアリングである。
車両全体の外観のスキャンの初期段階で、バオはArtec Evaを利用すればホンダ・S2000全体をデジタル化することができる、と気付いた。その業務に要したのは僅か二時間であったが、車両への最小限のテープの貼り付けが作業を遅らせる結果となり、毎秒三千五百万ポイントの速さのLeoであればもっと速く完了できただろう、とバオは話す。
「当然、S2000上に付けるマーカーの数を最小限に抑えようという気に駆られた」とバオは言う。「そこで、最初は自分で必要だと思う量から始めたが、少し足りないと気付き、行ったり来たりを繰り返した。Leoなら非常に高速なため、十五分でヘッドライト、ミラー、ウィンドウや黒のプラスチック製のトリムを準備して、次の十五分でスキャンを完了することもできる」
BD Engineering社の最新のデジタル化の業務の一環として、ラシュマノフは自身の社用車である二〇二三年製GRトヨタスープラ全体をリバースエンジニアリングした。車両を解体し、サスペンションの部品一つ一つ、並びにそのサブフレームをスキャンすることで、ラシュマノフはドリフト向けに設計された、油圧ハンドブレーキを取り付ける大掛かりな改造を行うことができた。
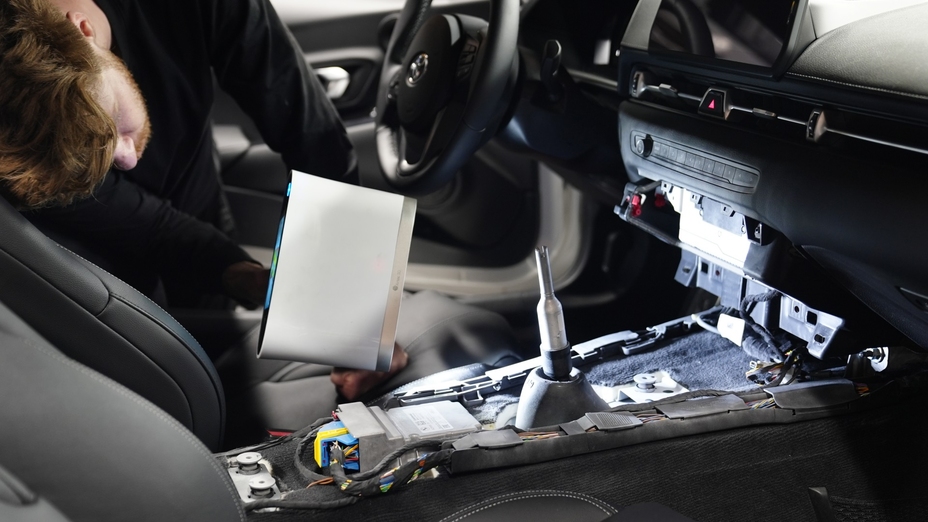
Artec Leoにより、トヨタスープラのハンドブレーキを3Dスキャンするラシュマノフ。画像は、BD Engineering社のご厚意で掲載
この工程は高速で操作しやすいLeoによって迅速かつ簡単に完了し、 Artec Studioの編集ツールセットも同様にメッシュの位置合わせを能率化し、設計上の制約を克服し、エクスポート時のサイズの低減のためにポリゴン数を減少させることに役立った、とラシュマノフは話す。
「Artec Studioは、大きな役割を担うことができる。実を言うと、利用過程は本当に楽しかった」と、ラシュマノフは言う。「Artec Studioのリバースエンジニアリングは設計上の制約すべてを一度に解決した上での再装備を可能とするため、その手法はかなり画期的である。所要時間も大幅に削減される」
「我々は新たなサスペンション部品のコストを計算上で最適化する動的シミュレーション環境を立ち上げる目的で、車両全体のリバースエンジニアリングを行った」
「スキャン・トゥ・ファクトリー」システムの確立
デジタル化され3Dプリントされたパーツへの需要が高まる中、BD Engineering社はIllumaesthetic社の従来の自動車産業基盤以外の取引先との業務を徐々に開始した。バオによると、『仲介サービス』として3Dプリンティングの枠を越えることで、このことを実現したという。
従来、OEMは実物大の3Dプリントの注文を発売前の宣伝用に、『二次元の生成画像ではなく、実際のパーツの写真で車両を売り込む』ために送ってきていた、とバオは話す。Illumaesthetic社はこのような取引先を今でも扱っているが、BD Engineering社はその他の得意先でこの技術を使い始めた。その一例は航空機体の製作で、軍事攻撃目標練習用ドローン作成用の鋳型の生成に利用される。
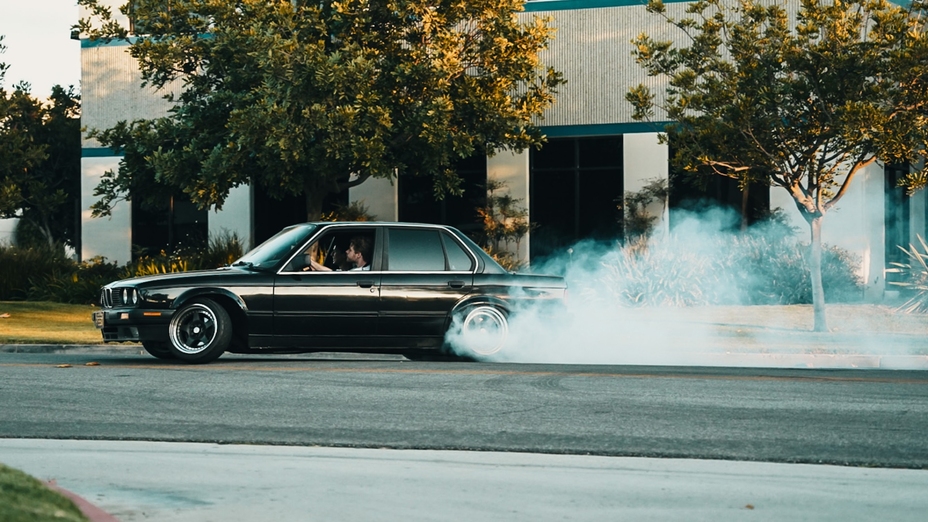
クラシックBMWで自身のドリフト技術を披露するラシュマノフ。画像は、BD Engineering社のご厚意で掲載
同社のスープラの改造に関しては、ラシュマノフは世界中のドリフト愛好家向けに製作・販売を行うことを将来的に予定している。また、同社は取引先がデジタル化のためのオブジェクトを持ち込めば、一カ月以内に外観パーツ、あるいは動作パーツが引き取り可能となる『スキャン・トゥ・ファクトリー(scan-to-factory)システム』の確立も目指している、と語る。
「当社の下には定期的に3Dスキャニングのためのオブジェクトが持ち込まれているが、これは我が社の仕事が他社を圧倒していることを取引先が周知しているからである。当社では必要なものを単にスキャンするだけではなく、オブジェクトを新たなレベルへと引き上げる」
ストーリーの背景で活躍するスキャナ
世界最高峰のポータブル3Dスキャナをお試しください。